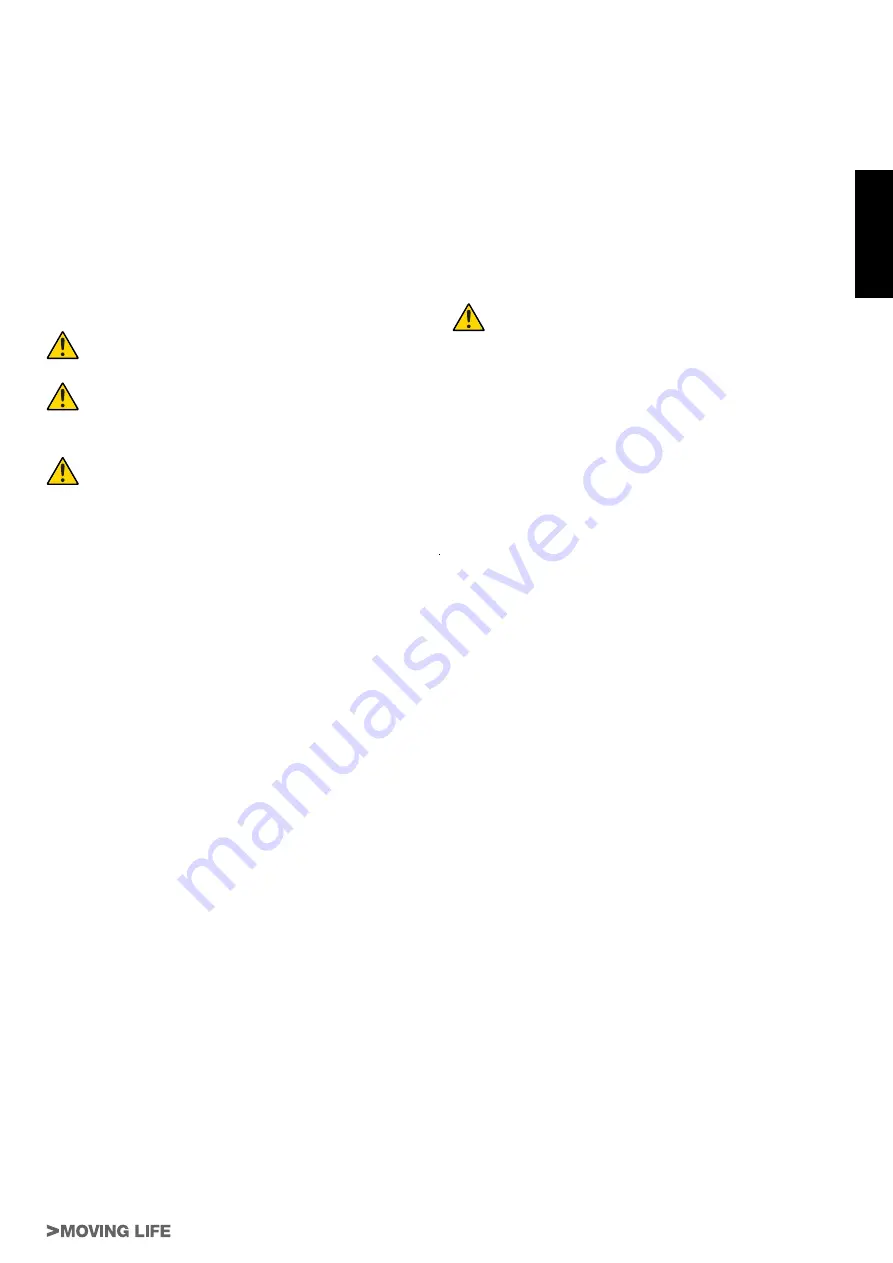
13
MASTER Series
EN
G
LI
SH
Cable sections:
MASTER12Q
MASTER18QR
MASTER20QR(M)
MASTER20T
MASTER-R
a
3 x 1,5 mm²
3 x 1,5 mm²
4 x 1,5 mm²
b
4 x 0,5 mm²
4 x 0,5 mm²
4 x 0,5 mm²
c
2 x 0,5 mm²
2 x 0,5 mm²
2 x 0,5 mm²
d
4 x 0,5 mm²
4 x 0,5 mm²
4 x 0,5 mm²
e
2 x 0,5 mm²
2 x 0,5 mm²
2 x 0,5 mm²
f
3 x 0,5 mm²
3 x 0,5 mm²
3 x 0,5 mm²
g
2 x 0,5 mm²
2 x 0,5 mm²
2 x 0,5 mm²
h
RG58
RG58
RG58
i
2 x 0,5mm²
2 x 0,5mm²
2 x 0,5mm²
l
(Gearmotor)
4 x 1,5mm²
m
(Limit switches)
3 x 0,5mm²
Place the control unit (external versions) in the immedi-
ate vicinity of the motors
.
Be careful not to run cables for auxiliary devices in-
side raceways housing other cables supplying power
to large loads or lights with electronic starters
.
In the event control pushbuttons or indicator lights are
installed inside homes or ofices several metres from
the actual control unit, it is advisable to decouple the
signal by means of a relay in order to avoid induced
interference
.
ADJUSTMENT OF THE ELECTRONIC/ELECTRIC CLUTCH
WARNING: Check that the impact force value measured at the
points foreseen by the EN 12445 standard is lower than that
indicated in the EN 12453 standard.
The adjustment on
MASTER12Q
is already preset during the pro
-
gramming of the control unit and can in any case be set (see in
-
structions K123M).
The adjustment of
MASTER18QR
and
MASTER-R
can be per-
formed through the control unit, see instructions K126MA.
The adjustment of
MASTER20QR
and
MASTER20QM
can be
performed through the control unit, see instructions D705M.
The adjustment of
MASTER20T
can be performed through the
control unit, see instructions D703M.
ELECTRICAL CONNECTIONS
Note: the MASTER series has a microswitch that cuts-out the
motor when the casing is opened, A ig. 25 (the control unit
remains live).
Make sure that the gearmotor is disconnected from the power
supply before performing any operations.
To make the connections, remove the gearmotor casing, pass
the cables through the holes on the base plate (when used) and
through the lower section of the gearmotor. Then arrange the ca
-
bles for the connection to the control unit terminal block that is
located in the electrical components support.
The distance between the control unit and the motor must not ex
-
ceed 10 – 12 m.
Use cables with a minimum section of 2.5 mm² for the power circuit
of the MASTER12Q-18QR-R and 1.5 mm² for the MASTER20QR-
M and MASTER20T, and 0.5 mm² for the control circuit.
Consult the related instructions booklet for the control unit con
-
nections:
- K123M
MASTER12Q;
- K126MA
MASTER18QR and MASTER-R;
- D705M
MASTER20QR and MASTER20QM.
- D703M
MASTER20T;
Note: the thermal protection (for MASTER20T only) must be
wired in series to the common of the limit switch (terminal 19
of the D703M board).
12V BATTERY INSTALLATION
If one wishes to it a battery to the
MASTER12Q-18QR-R
gearmo
-
tor in order to guarantee power in the event of blackout, remove
the casing and it the battery into its location; then connect the
power supply cables to the tongues.
Note: when using in battery the performance of the MASTER-
R (24v DC) is the same as the MASTER12Q, with the same
speed both opening and closing.
MANUAL RELEASE
In the absence of the mains power supply, remove the lock cover,
insert the special key and turn it as indicated in ig. 21.
Then pull the lever outwards in order to manually manage the gate,
as shown in ig. 22.
DC versions feature a safety micro-switch in the re-
lease lever (“A”, pic. 22). In case the gate operator
stays released for more than 5 seconds, the operator
will perform a cycle at a slow speed to reset the op-
erating parameters to the values originally saved (see
“Restoring automatic operation”).
LIMIT SWITCH
The MASTER series has been designed to operate with a micros
-
witch electromechanical limit switch device.
The cables are connected as indicated in ig. 25:
1= grey (common);
2= grey (common);
3= orange (L.S. close - contact N.C.);
4= red (L.S. open - contact N.C.);
5= grey (common).
If the movement continues when the gears rotate in a clock-wise
direction and the spring moves as shown in ig. 26, invert the red
and orange wires on the control unit terminal block.
In order to connect the magnetic limit switches to other control
units, wiring must be as follows:
- black (L.S. open - contact N.C.);
- brown (L.S. close - contact N.C.);
- blue (Common).
GENERAL WARNINGS
Integrate the gate safety in accordance with the present regula
-
tions.
- Choose short paths for the cables and keep the power and
control cables separated;
- Make sure that the equipment is correctly grounded;
- Abide by the present regulations for the setup of the gearmo
-
tor’s maximum torque;
- An external switch should be itted in compliance with the Eu
-
ropean safety standards in order to turn off the power supply to
the gate for maintenance purposes;
- Make sure that all devices are eficient and in working order;
- Post clearly legible signs informing that the gate is motorised.
USE
The MASTER series gearmotors have been designed for the
movement of horizontally sliding gates weighing up to 1000 Kg
for
MASTER-R
, 1200 Kg for
MASTER12Q
, 1800 Kg for
MAS-
TER18QR
, and 2000 Kg for
MASTER20QR
,
MASTER20QM
and
MASTER20T
.
Use of the equipment for aims or circumstances different
from those stipulated is prohibited.
The following functions can be selected by means of the control
unit:
automatic
: the gate is opened and closed following a command
input;
semiautomatic
: the gate is opened or closed following a com
-
mand input;
The gate can be manually controlled by means of a
manual re-
lease
in the event of a power failure. In the event of a power fail
-
ure, normal functioning of the
MASTER12Q
,
MASTER18QR
and
MASTER-R
model is guaranteed by means of a buffer battery.