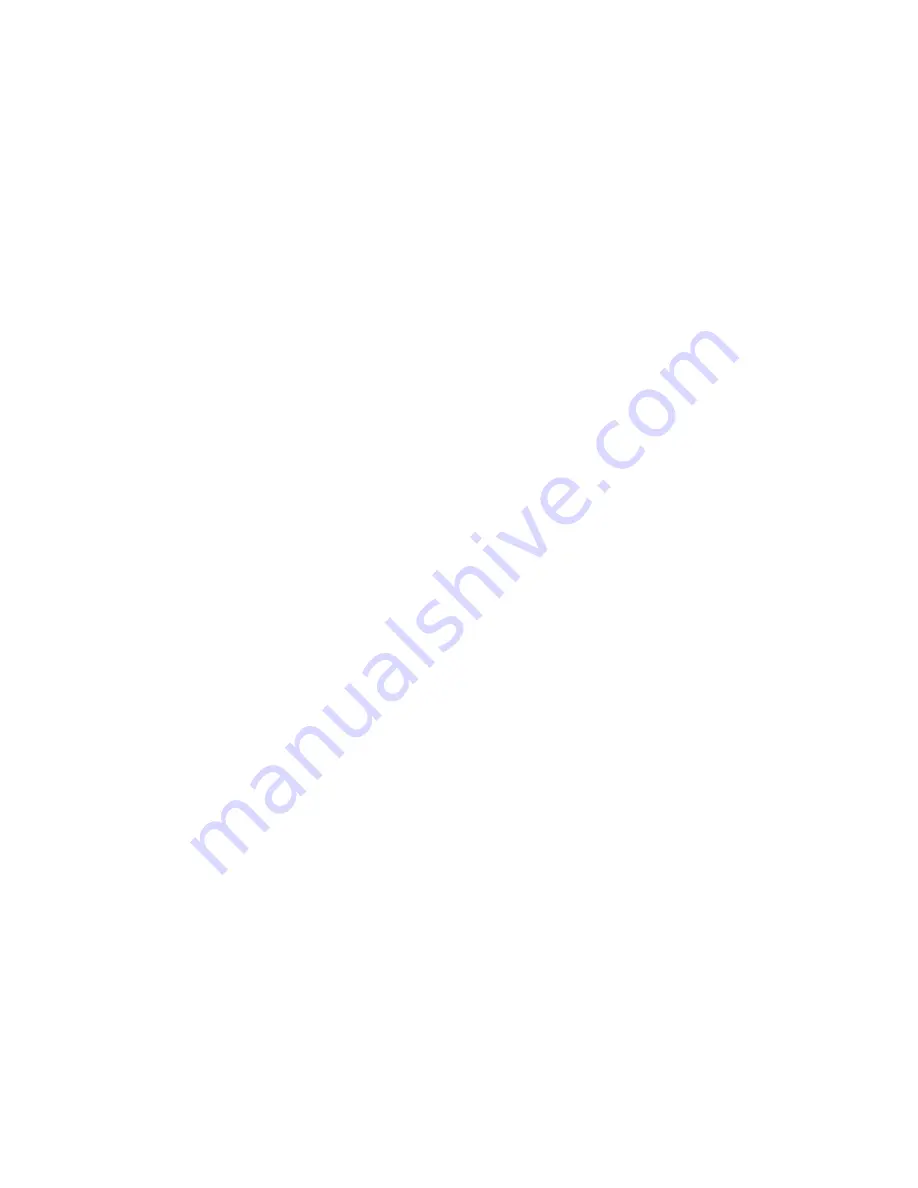
[Technical Documentation]
PRESSURE REGULATORS AND INDICATORS
It should also be pointed out that if the machine is stopped for periods of any
length the pressure roller must not be activated, so that it is not in contact
with the calendar, since if this should happen, the neoprene with which this
roller is constructed may become deformed and loose its surface uniformity.
This deformation will cause the plastic not to adhere to the paper in a uniform
manner, therefore causing incorrect lamination.
TEMPERATURE REGULATION
Working temperature for the machine depends on the size of the printed
sheet being laminated and on the speed.
For one and the same sheet format, at greater speed we will require a higher
temperature, for example, for a sheet of a determined format we will require a
higher temperature if the working speed is 15 m/min than if it were only 7
m/min.
This is due to the fact that the exposure time, that is to say, the time the
sheet is in contact with the temperature and pressure rollers is less the higher
the speed, so that in this case we must provide more heat for the final result
to be correct.
In any event practice will in the long run be what defines the correct working
temperature, which will very much depend on the characteristics of the
product being laminated.
It should be pointed out that as we have already explained, in order to heat
the machine before laminating, it is convenient to set the temperature at 40-
50 degrees with calendar in operation. With this what we achieve is that the
initial working temperature is very stable.
We should consider that for practical effects it is preferable to begin working at
80-90ºC and increase this gradually if necessary.
If we do this in the reverse order we run the risk of melting the plastic due to
excessive heat, and we will also suffer a delay due in the first place to the
thermal inertia of the oil, which takes longer to cool off than to heat up; and