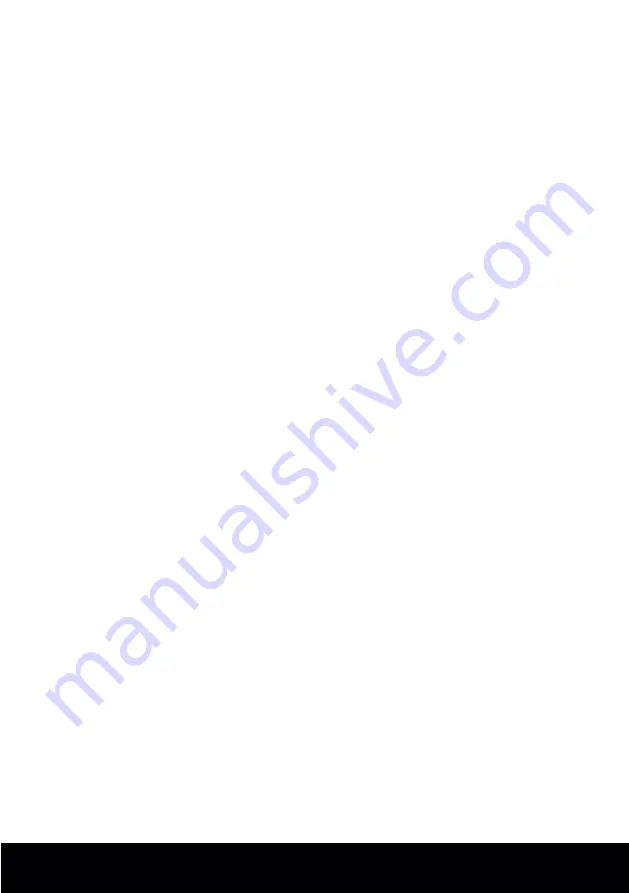
m
7.2 Attaching the table length and width
extensions (Fig. 10-14)
•
Loosely attach the table width and length
extensions (14/15) to the saw bench (1) with
the hex screws (c), washers (a) and nuts (b).
(Figure 12-13).
•
Screw the supports (23) loosely to the housing
of the bench saw and to the table width/
length extensions. (Short supports for width
extension, long supports for length extension)
(Fig 13-14).
•
Adjust the table width and length according to
the saw bench (1).
•
Finally, tighten all screws.
•
Turn the saw and base frame around and set it
on the floor.
7.3 Assembling/disassembling the saw
blade guard (Fig. 2, 15-16)
•
Set the saw blade guard (2) with screw (24)
from above onto the splitter (4), so that the
screw sits firmly in the oval hole (25).
•
Do not tighten the screw (24) too much; the
saw blade must be able to move freely.
•
Attach the extractor hose (3) to the extractor
adapter (16) and to the extraction port of the
saw blade guard (2) and screw them to the
extractor adapter with the safety clamp (16).
•
Connect a suitable chip extraction system to
the extractor adapter (16).
•
To dismantle, proceed in reverse order.
Caution: Before starting to saw, the saw
blade guard (2) must be lowered onto to the
workpiece.
7.4 Replacing the table insert (Fig. 17-18)
•
If the table insert is worn or damaged, it
should be replaced, otherwise risk of injury is
increased.
•
Take off the saw blade guard (2) (see 7.3)
•
Remove the 2 countersunk screws (26)
•
Remove the worn table inserts (6)
•
Assembly of the new table inserts is to be
carried out in reverse order.
7.5 Adjusting the splitter (Fig. 19-20)
•
Caution: Pull out the power plug.
•
Set the saw blade (5) to max. cutting depth.
•
Adjust and lock the cutting depth into the 0°
position (see Fig. 8.2).
•
Disassemble the saw blade guard (see 7.3)
•
Remove the table inserts (6) (see 7.4)
•
Loosen the fixing screws (27).
7.5.1 Setting for maximum cuts
•
Push up the splitter (4) until the gap between
the saw table (1) and the upper edge of the
splitter (4) is at 10cm.
•
The distance between saw blade (5) and
splitter (4) should be a maximum of 5mm. (Fig.
20)
•
Re-tighten the screws (27) and assemble the
table inserts (6) (see 7.4).
19
After Sales Support TEL: 1300 922 271 EMAIL: service.australia@einhell.com
7.6 Assembly/Changing the saw blade
(Fig. 21)
•
Caution: Pull out the power plug first.
•
Detach the saw blade guard (2) (see Fig. 7.3).
•
Remove the table inserts by loosening the 2
countersunk screws (see 7.4)
•
Loosen the nut (
Caution!
Turn the nut in the
direction in which the saw blade rotates) by
using a wrench (24mm) on the nut and another
wrench (10mm) on the motor shaft to apply
counter-pressure.
•
Remove the outer flange and withdraw the old
saw blade diagonally from the inner flange.
•
Clean the blade flange thoroughly before
fitting the new blade.
•
Mount and fasten the new saw blade in reverse
order.
•
Caution: Note the running direction. The
cutting angle of the teeth must point in
running direction, i.e. forwards (see the arrow
on the blade guard).
•
Refit and set the table insert (6) and the saw
blade guard (2) (see 8.4, 8.5)
•
Check to make sure that all safety devices
are properly mounted and in good working
condition before you begin working with the
saw again.
8. Operation
8.1 ON/OFF Switch (Fig. 22/pos. 11)
•
The saw can be switched on by pressing the
green button “I”. Before starting to saw, wait
until the saw blade has reached its maximum
rotation speed.
•
In order to switch the saw off again, the red
button “0” must be pressed.
8.2 Cutting depth (Fig. 22)
•
By turning the hand crank (8), the saw blade
(5) can be adjusted to the desired cutting
depth.
Anticlockwise direction:
Larger cutting depth
Clockwise direction:
Smaller cutting depth
8.3 Setting the angle (Fig. 22)
•
Loosen the locking grip (9)
•
Set the desired angle on the scale by turning
the handle.
•
Lock the locking grip to the desired angularity.
8.4 Parallel stop
8.4.1. Stop height (Fig. 23-26)
•
The stop rail (e) of the parallel stop (7) has two
different guide faces.
•
According to the thickness of the material to
be cut, the stop rail must be used according
to Fig. 25 for thick material (over 25mm
workpiece thickness), and according to Fig.
26 for thin material (under 25mm workpiece
thickness.