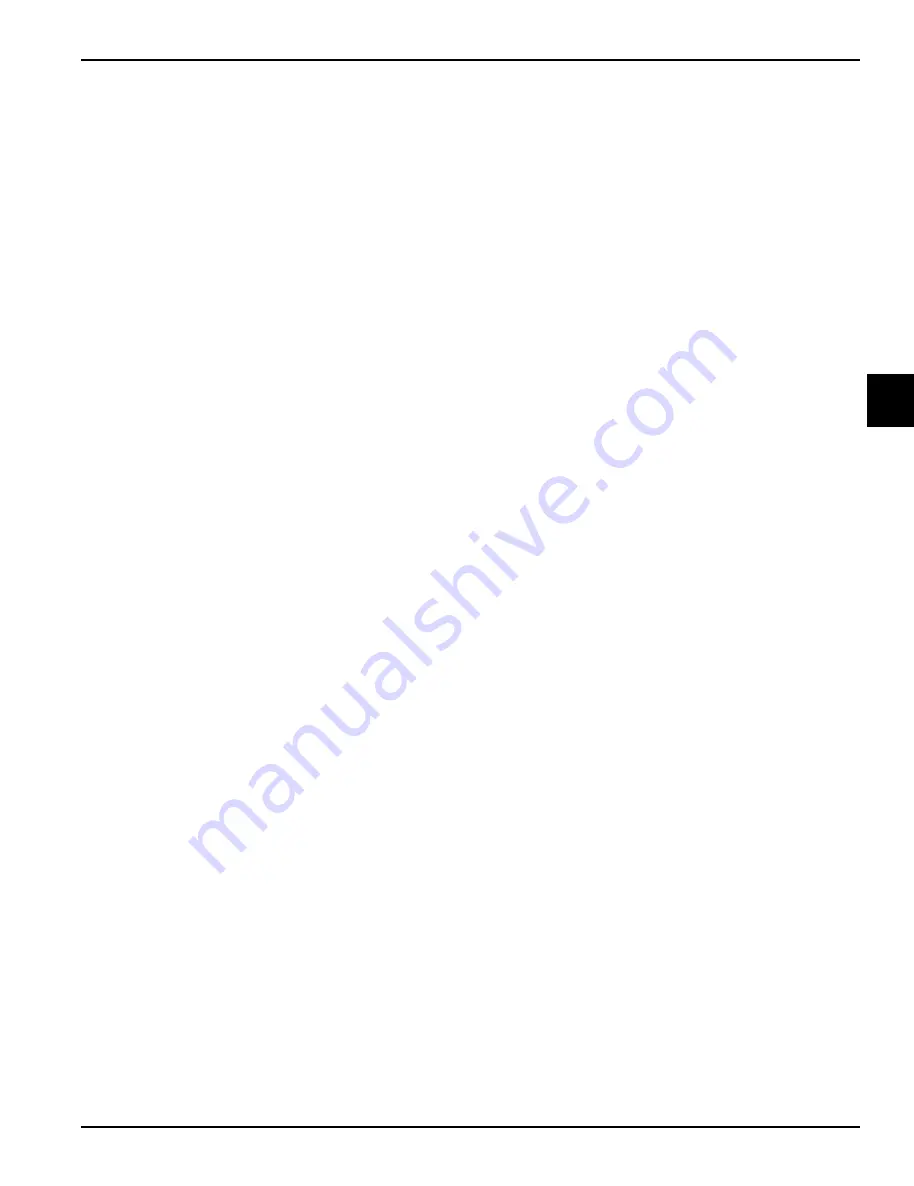
SAFETY
3-3
Model 632
Safety
3
DO NOT
obstruct air intake and discharge openings:
The minimum required air space on all sides is
3” (76 mm). A deflector is provided to prevent
recirculation of warm air. Failure to follow this instruction
may cause poor freezer performance and damage to the
machine.
For Indoor Use Only:
This machine is designed to
operate indoors, under normal ambient temperatures of
70°F to 75°F (21°C to 24°C). The machine has
successfully performed in high ambient temperatures of
up to 104°F (40°C) at reduced capacities.
DO NOT
run the machine without product. Failure to
follow this instruction can result in damage to the
machine.
NOISE LEVEL:
Airborne noise emission does not
exceed 78 dB(A) when measured at a distance of 39
inches (1.0 m) from the surface of the machine and at a
height of 63 inches (1.6 m) from the floor.
All manuals and user guides at all-guides.com