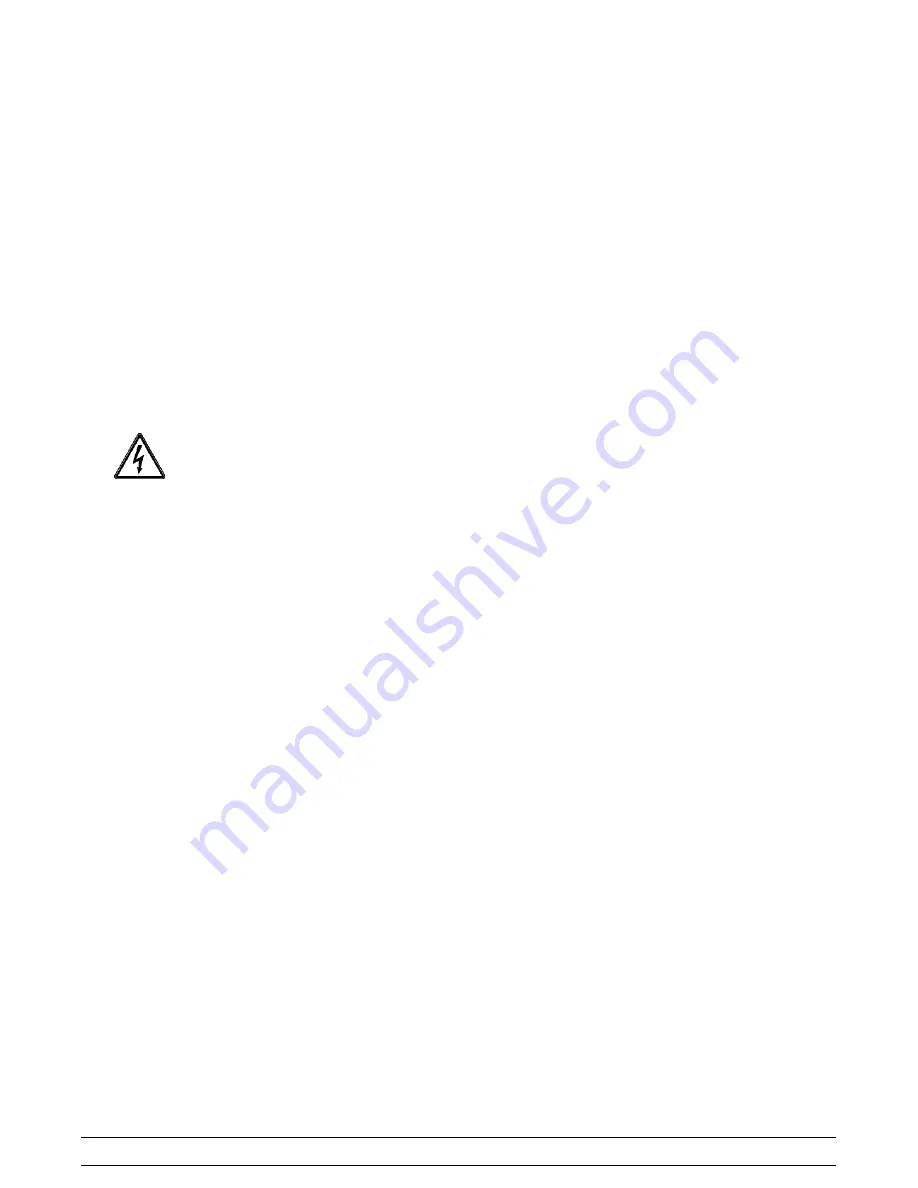
32
Model C713
Important: Operator Checklist
j
4. Dispose of o-rings and seals if they are worn,
torn, or fit too loosely, and replace with new
ones.
j
5. Follow all lubricating procedures as outlined in
“Assembly”.
j
6. If your machine is air cooled, check the
condensers for accumulation of dirt and lint.
Dirty condensers will reduce the efficiency
and capacity of the machine. Condensers
should be cleaned
monthly
with a soft brush.
Never
use screwdrivers or other metal probes
to clean between the fins.
Note:
For machines equipped with an air
filter, it will be necessary to vacuum clean the
filters on a monthly schedule.
Caution: Always disconnect
electrical power prior to cleaning the
condenser.
Failure to follow this instruction
may result in electrocution.
j
7. If your machine is water cooled, check the
water lines for kinks or leaks. Kinks can occur
when the machine is moved back and forth for
cleaning or maintenance purposes.
Deteriorated or cracked water lines should be
replaced only by an authorized Taylor
distributor.
Winter Storage
If the place of business is to be closed during the
winter months, it is important to protect the freezer
by following certain precautions, particularly if the
building is subject to freezing conditions.
Disconnect the freezer from the main power source
to prevent possible electrical damage.
On water cooled freezers, disconnect the water
supply. Relieve pressure on the spring in the water
valve. Use air pressure on the outlet side to blow out
any water remaining in the condenser.
This is
extremely important.
Failure to follow this
procedure may cause severe and costly damage to
the refrigeration system.
Your local Taylor Distributor can perform this winter
storage service for you.
Wrap detachable parts of the freezer such as
beater, blades, drive shaft, and freezer door, and
place them in a protected dry place. Rubber trim
parts and gaskets can be protected by wrapping
them with moisture-proof paper. All parts should be
thoroughly cleaned of dried mix or lubrication which
attract mice and other vermin.
It is recommended that an authorized service
technician perform winter storage draining, to insure
all water has been removed. This will guard against
freezing and rupturing of the components.
Summary of Contents for c713
Page 49: ...Model C713 059899 27 7 25 11 ...
Page 50: ...Model C713 059899 33 7 25 11 ...
Page 51: ...Model C713 059899 40 7 25 11 ...
Page 52: ...Model C713 059899 58 7 25 11 ...