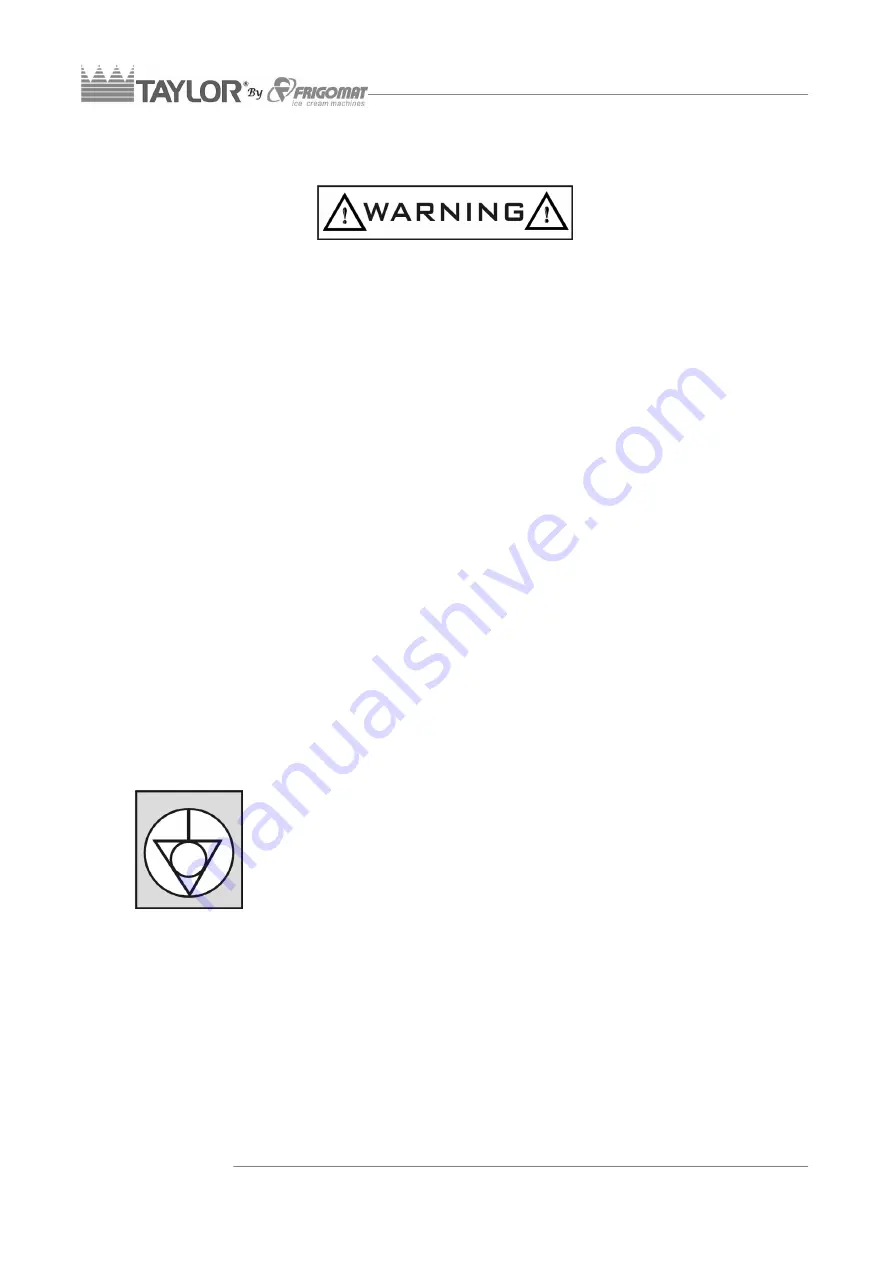
9 - ENGLISH
4.5 ACTIVATION (INTENDED FOR QUALIFIED PERSONNEL)
TAYLOR declines all and any liability for damage caused by failure to comply with the
following indications. This lack of compliance causes the warranty to terminate.
Connection of the machine to the water mains must be performed in compliance with
national regulations of the Country where the machine is installed.
To commission the machine, bring it to the place of use, checking what is requested for its
installation:
•
Make sure the appliance is positioned on a solid, stable, flat and levelled surface.
•
If
required,
adjust the rear feet.
•
Leave at least 10 cm between the machine and the walls or other obstacles.
•
Check the exact correspondence between the voltage and power of the mains
compared to the values carried on the data plate applied on the rear panel;
•
Connect the machine to the electrical power supply system. Install an omnipolar master
switch upstream the appliance with minimum contact opening of 3 mm of adequate
power, with a fuse and circuit breaker protective system. Use an approved interlocking
plug to allow only the open circuit to connect and disconnect.
•
The cable must be well laid, without being rolled-up or overlapped. It must not be
exposed to blows or tampering. It must not be in the vicinity of liquids or water and heat
sources. It must not be damaged in any way. If so, before connecting the machine to
the mains, have it replaced by qualified personnel with another section and type 3G1.5
H05VV-F
•
For safety purposes, make sure the earthing system to which the machine plug is
connected is compliant with standards and perfectly efficient.
•
If needed, carry out an equipotential bonding, using the screw
placed on the rear of the machine below the frame and
marked with the symbol shown to the left.
•
Operating temperature should be between 15° and 35°C.
•
Humidity should be between 30 and 60%.
Summary of Contents for Frigomat CH02 Series
Page 1: ...MANUALE D USO E MANUTENZIONE OPERATING INSTRUCTION AND MAINTENANCE Serie Series CH02 05...
Page 30: ...APPENDICI 2 9 2 Schema circuito frigorifero Refrigerant circuit diagram...
Page 33: ...5 APPENDICI CH02 s05 Tav 1...
Page 35: ...7 APPENDICI CH02 s05 Tav 2...
Page 37: ...9 APPENDICI CH02 s05 Tav 3...
Page 39: ...11 APPENDICI CH02 s05 Tav 4...
Page 41: ...NOTE NOTES NOTES BEMERKUNG NOTA...
Page 42: ......