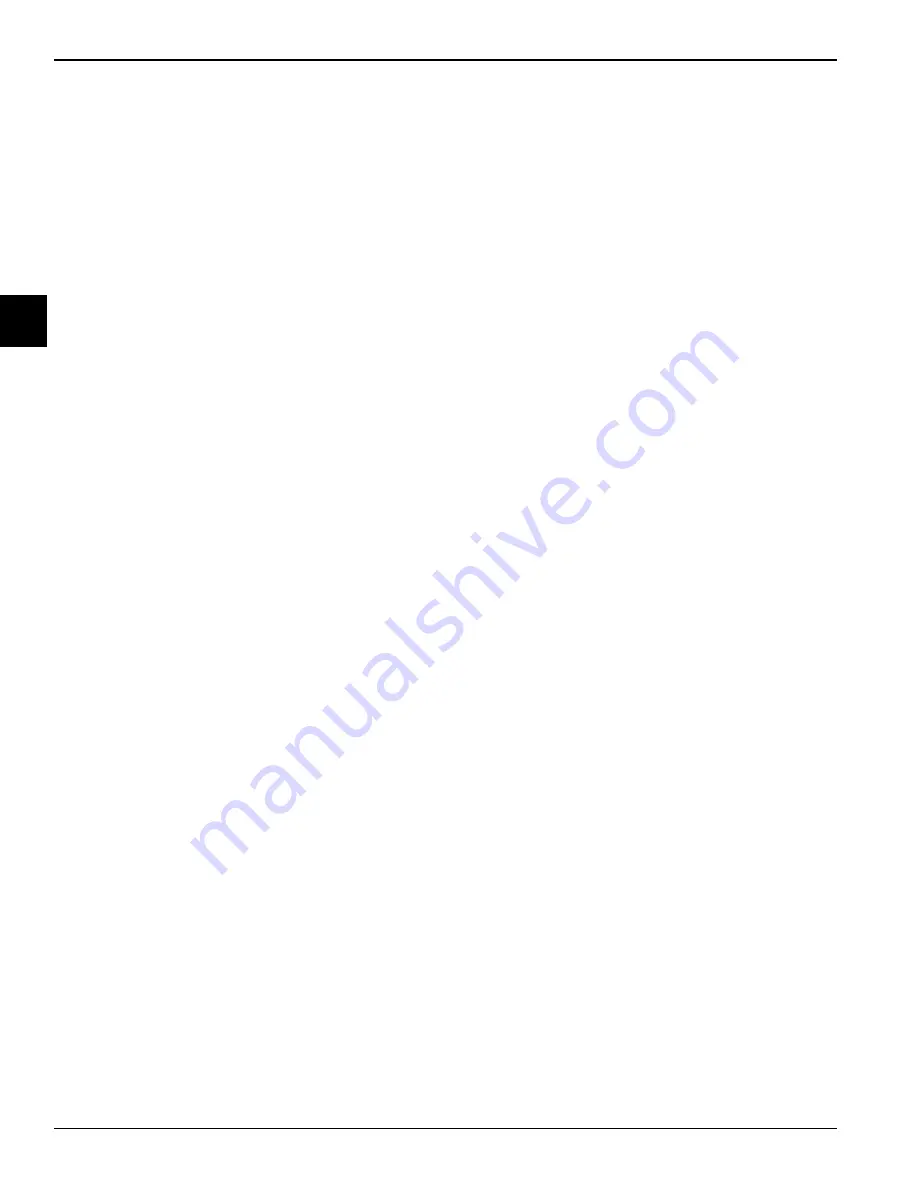
2-2
TO THE OPERATOR
Model 8756
To the Operator
2
Compressor Warranty Disclaimer
The refrigeration compressor(s) on this machine are
warranted for the term stated in the Limited Warranty
section in this manual. However, due to the Montreal
Protocol and the U.S. Clean Air Act Amendments of
1990, many new refrigerants are being tested and
developed, thus seeking their way into the service
industry. Some of these new refrigerants are being
advertised as drop-in replacements for numerous
applications. It should be noted that in the event of
ordinary service to this machine’s refrigeration system,
only the refrigerant specified on the affixed data label
should be used.
The unauthorized use of alternate
refrigerants will void your Taylor compressor warranty. It
is the machine owner’s responsibility to make this fact
known to any technician he/she employs.
It should also be noted that Taylor does not warrant the
refrigerant used in its machine. For example, if the
refrigerant is lost during the course of ordinary service to
this machine, Taylor has no obligation to either supply or
provide replacement refrigerant either at billable or
unbillable terms. Taylor will recommend a suitable
replacement if the original refrigerant is banned,
obsoleted, or no longer available during the five (5) year
Taylor warranty of the compressor.
From time to time Taylor may test new refrigerant
alternates. Should a new refrigerant alternate prove,
through Taylor’s testing, that it would be accepted as a
drop-in replacement for this machine, then the disclaimer
in this Compressor Warranty Disclaimer section will not
apply to the use of the alternate refrigerant approved by
Taylor.
To find out the current status of an alternate refrigerant as
it relates to your compressor warranty, call Taylor or your
local authorized Taylor distributor. Be prepared to provide
the model/serial number of the machine in question.
Summary of Contents for Horizon 8756
Page 18: ...4 6 OPERATOR PARTS IDENTIFICATION Model 8756 Operator Parts Identification 4 Notes ...
Page 22: ...5 4 USER INTERFACE Model 8756 User Interface 5 Notes ...
Page 40: ...6 18 OPERATING PROCEDURES Model 8756 Operating Procedures 6 Notes ...
Page 46: ...8 4 TROUBLESHOOTING GUIDE Model 8756 Troubleshooting Guide 8 Notes ...
Page 48: ...9 2 PARTS REPLACEMENT SCHEDULE Model 8756 Parts Replacement Schedule 9 Notes ...
Page 52: ...10 4 LIMITED WARRANTY ON EQUIPMENT Model 8756 Limited Warranty on Equipment 10 Notes ...
Page 56: ...11 4 LIMITED WARRANTY ON PARTS Model 8756 Limited Warranty on Parts 11 Notes ...
Page 58: ...12 2 WIRING DIAGRAMS Model 8756 Wiring Diagrams 12 Notes ...