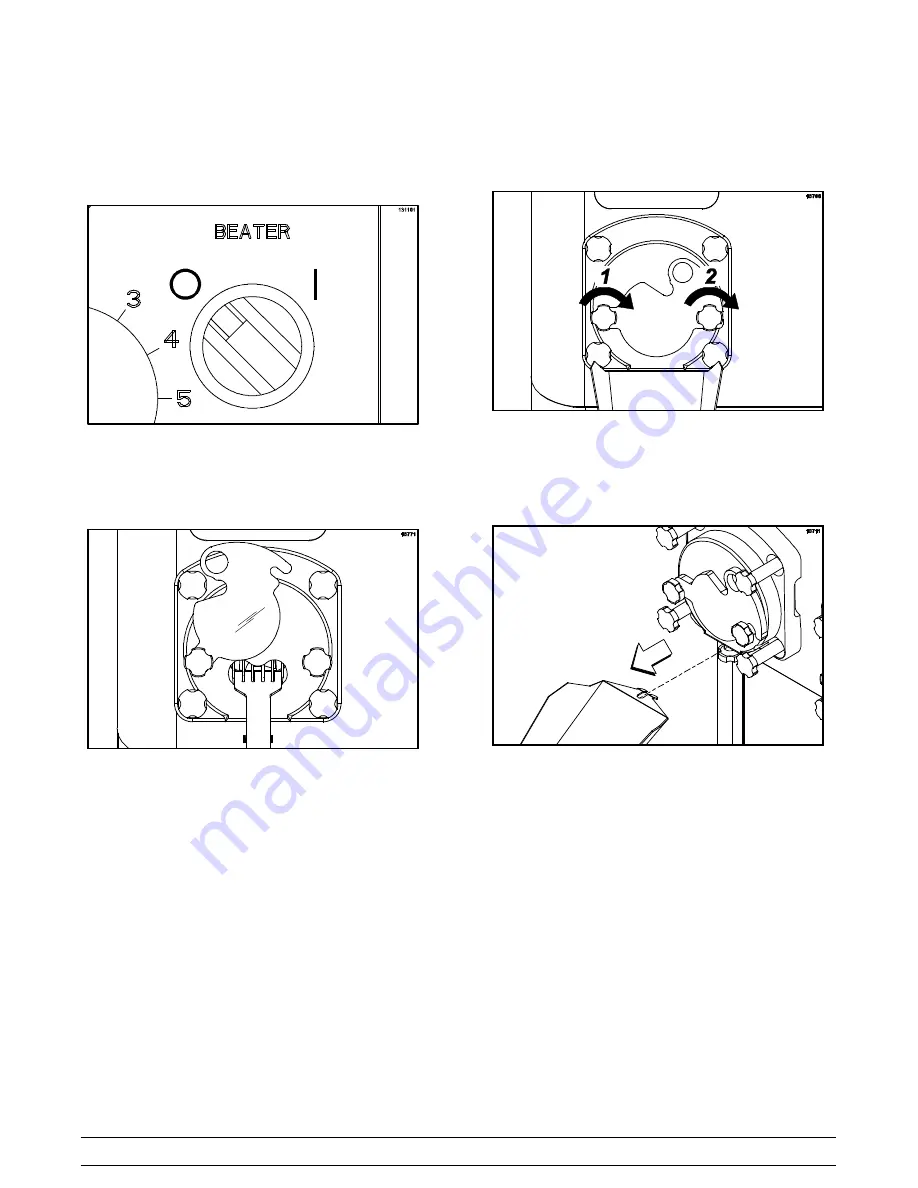
24
Model C043
Operating Procedures
150629
Step 3
When the frozen custard stops flowing,
(takes approximately two minutes) place the beater
motor switch in the OFF position.
Figure 43
Step 4
Use the rake to remove as much custard from the
product door as possible.
Figure 44
Step 5
Close the draw arm plate. Make sure the left stud
nut is snug and then the right stud nut.
Figure 45
Step 6
Remove the custard chute and take it to the sink for
cleaning and sanitizing.
Figure 46