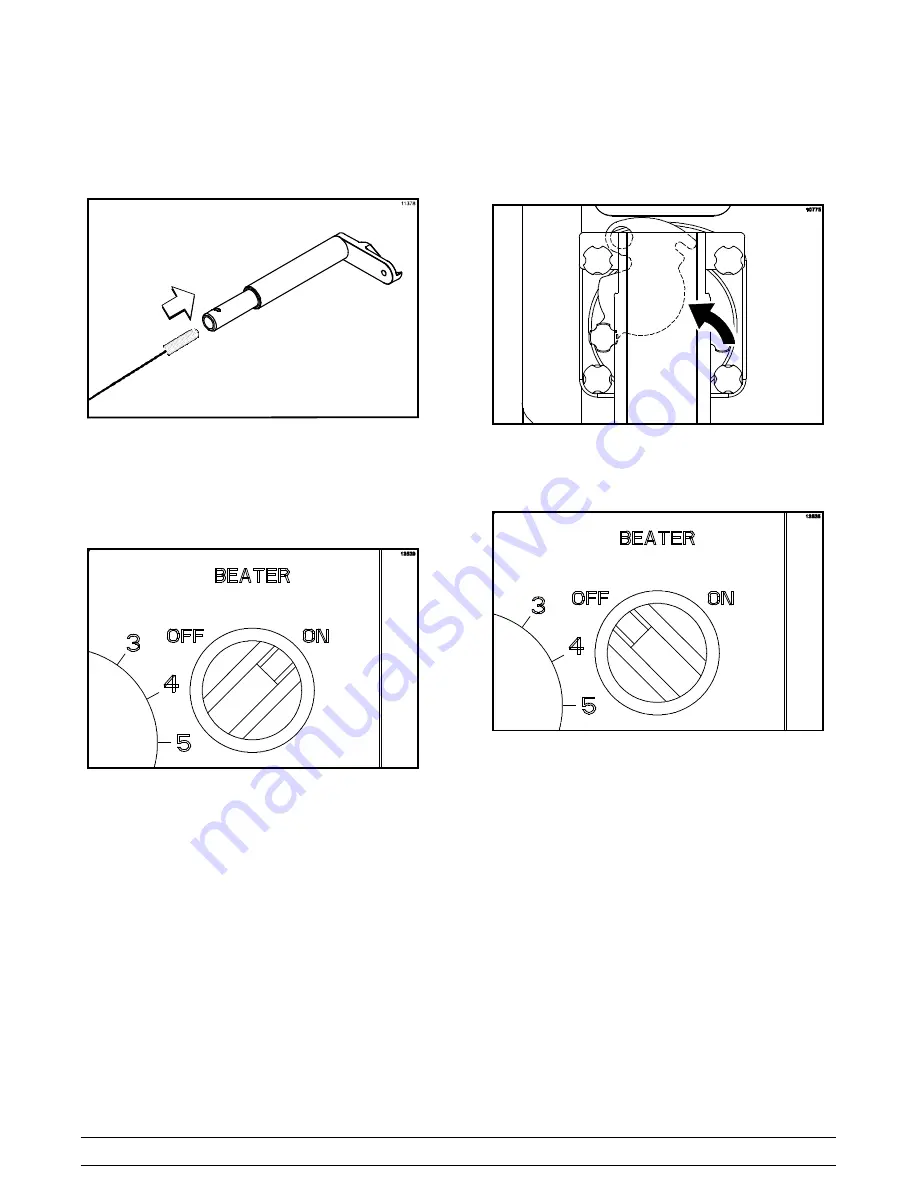
34
Model C043
Operating Procedures
Step 7
Using the double-ended brush, clean the inside of
the feed tube.
Figure 85
Step 8
Place the beater switch in the “ON” position. Set the
timer for five minutes.
Figure 86
Step 9
After five minutes has elapsed, open the draw arm
plate and drain all the solution from the freezing
cylinder.
Figure 87
Step 10
Place the beater switch in the “OFF” position.
Figure 88
Step 11
Repeat these steps for each freezing cylinder.
Summary of Contents for Model C043
Page 1: ...Model C043 General Market Custard Machine Operating Instructions 068359 M 7 22 10 ...
Page 11: ...7 Model C043 Safety Notes ...
Page 14: ...10 Model C043 Operator Parts Identification Beater Door Hopper Assemblies Figure 2 ...
Page 57: ...C043 063943 33A Rev 7 10 ...
Page 58: ...C043 063943 33B Rev 7 10 ...