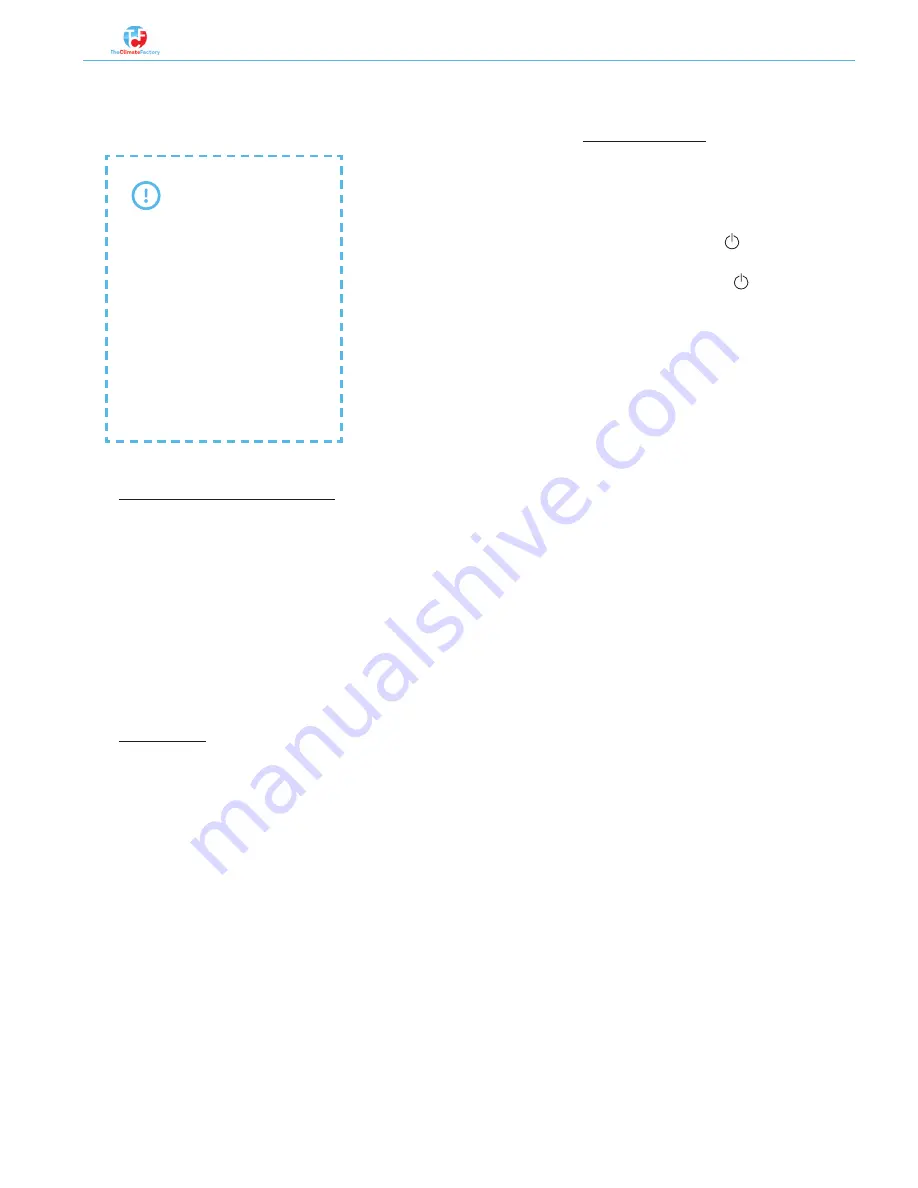
ANL - ANLH 020-202
28
8. CHECKS AND FIRST START-UP
8. CHECKS AND FIRST START-UP
8.1. PREPARING FOR FIRST START-UP
It is reminded that for units of this se-
ries, if requested by the Aermec client
or the legal owner and only on ITA-
LIAN territory, free start-up is provided
by the regional Aermec technical as-
sistance service. The start-up must be
previously agreed based on the inten-
ded time of completion of installation.
Before the start-up all the works (elec-
trical and hydraulic connections, fi lling
and venting of air in the system) must
be completed.
8.2. START-UP
8.2.1. PRELIMINARY CHECKS
BEFORE POWERING UP
Check:
1. All safety precautions have been
followed.
2. The unit has been appropriately
fi xed to the support base.
3. Minimum clearance spaces have
been observed.
4. Power supply cables are correct-
ly sized and capable of suppor-
ting the electrical requirements of
the unit (see section on electrical
data) and that the unit is correctly
earthed.
5. All electrical connections are co-
rrectly terminated and tightened.
8.2.2. CHECKS TO BE DONE
WHEN POWERED UP
1. Apply power to the unit by tur-
ning the main isolator to the ON
position. The display will power
up after several seconds after
applying power, check that the
operating status is on OFF (OFF
BY KEYB on the lower part of the
display).
2. Check with a tester that the
power supply voltages on the
phases U-V-W are 400V ±10%,
check that the phase imbalance
is not greater than 3%.
3. Check that the connections made
by the installer comply with the
documentation.
4. Check that the compressor crank-
case heater(s) are operating by
measuring the increase of oil
sump temperature. The heater(s)
must be in operation for at least
12 hours before starting the com-
pressor, and in all cases the sump
oil temperature must be 10-15 K
above ambient temperature.
HYDRAULIC CIRCUIT
1. Check that all hydraulic connec-
tions have been correctly insta-
lled, that the instructions on the
labels have been followed, and
that a mechanical fi lter has been
installed on the inlet to the eva-
porator. (Mandatory component
otherwise the warranty will be
voided).
2. Confi rm that the pump(s) are
operating and that the fl ow rate
is suffi cient to make the contact
on the fl ow switch.
3. Check the water fl ow rate by
measuring the differential pres-
sure across the evaporator inlet
and outlet and calculating the
fl ow from the evaporator pressu-
re drop diagram provided in the
documentation.
4. Check the correct functioning of
any fl ow switch installed; close the
isolating valve on the evaporator
outlet and observe the result on the
unit display panel; open the valve
and reset the fl ow trip alarm.
WARNING
Before carrying out the following
checks ensure the unit is discon-
nected from the power supply.
Ensure that the main isolator is
in the OFF position and locked
in that position with appropria-
te warning label attached.
Before starting the procedures
check for the absence of volta-
ge with a voltmeter or phase
checker.
8.3. FIRST START-UP
After having rigorously followed the abo-
ve checks it is possible to start the unit:
1. Close the electrical panel.
2. Turn the main isolator to ON.
3. Press the key ON for 3 se-
conds to start the unit.
4. Pressing the key ON displays
the water temperature and the
operating mode of the unit.
5. Check the operating setpoint pa-
rameters and reset any alarms
present. After a few minutes the
unit will start.
8.3.1. CHECKS WITH THE UNIT
RUNNING
REFRIGERANT CIRCUIT CHECK:
• That the compress
or input current
of the compressors is less than that
indicated in the table of electrical
data.
• That in three phase models the
compressor noise is not abnormal,
indicating a reverse rotation. In this
case reverse one of the phases.
• That the voltage values are within
the determined limits and that the
phase imbalance (three phase
power) is less than 3%.
• Presence of any refrigerant leaks,
in particular from connections to
gauges, pressure transducers and
pressostats. (Vibrations during
transportation may have loosened
connections).
• Superheat
Compare the compressor suction
temperature with a contact tempe-
rature sensor reading with the tem-
perature of the low pressure gauge
(saturated
• suction temperature corresponding
to the evaporating pressure). The
difference between these two tem-
peratures is the superheat value.
The optimal values are between 4
and 8 K.
• Discharge temperature
If the values of sub-cooling and
superheat are normal the tempe-
rature measured in the discharge
line from the compressor must be
30/40 K above the condensing
temperature.