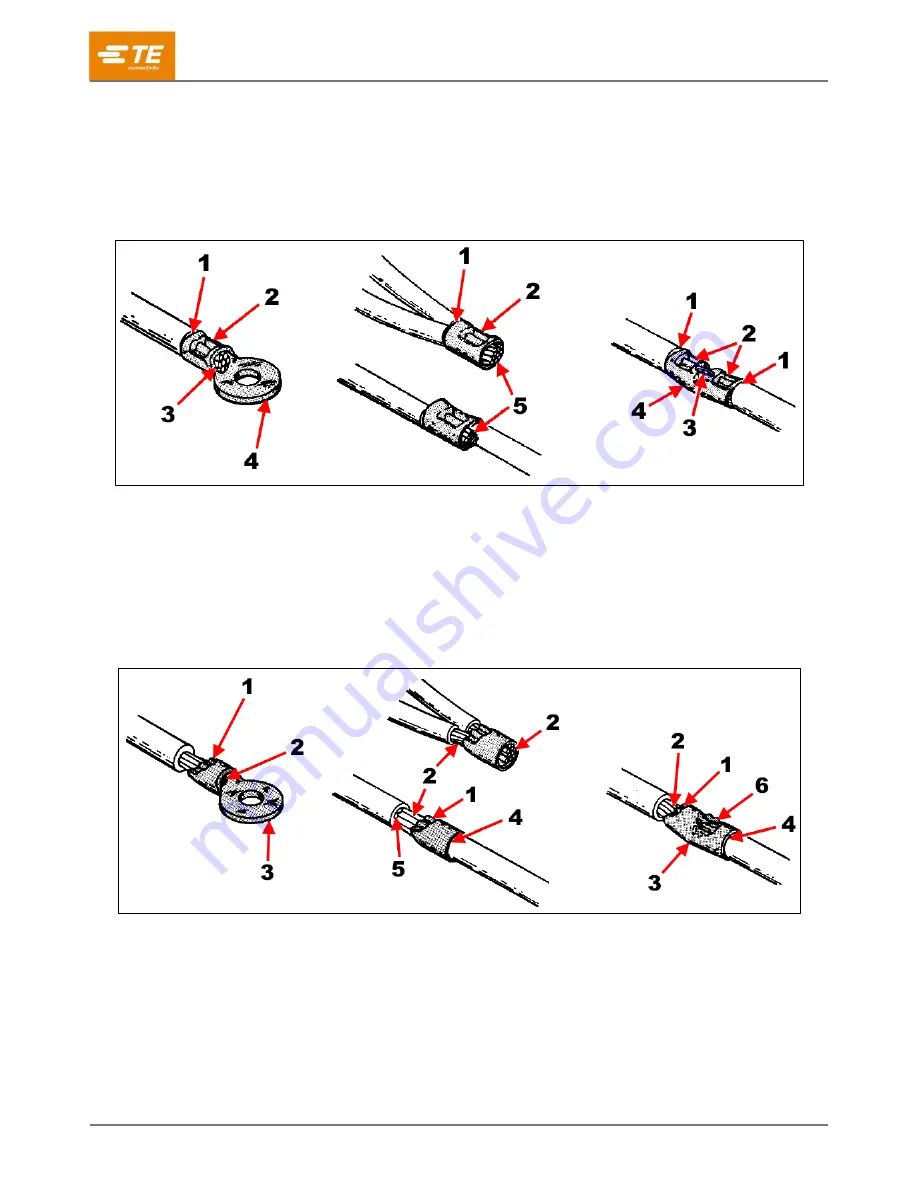
408-1697
Rev
D
6
of 11
6.
INSPECTING THE CRIMP
Inspect crimped terminals and splices by checking the features described in Figure 7 and Figure 8. Use only
the terminals and splices that meet the conditions shown in Figure 7. Poor crimps (Figure 8) can be avoided
through careful use of the instructions in sections 2 through 5, and by performing regular die maintenance as
instructed in section 7, MAINTENANCE AND INSPECTION.
Figure 7: Features of a good crimp (ACCEPT)
1
Wire insulation does not enter wire barrel.
2
Crimp is centered. Crimp can be off center, but
not off the end of the wire barrel
.
3
Wire is visible through inspection hole of butt splice. Wire is flush with (or extends slightly
beyond) end of terminal wire barrel.
4
AWG wire size matches wire size stamped on terminal or splice and crimping dies.
5
On parallel splice, bare wire ends are flush with (or extend slightly beyond) end of barrel.
Figure 8: Features of a poor crimp (REJECT)
1
Crimp is off end of wire barrel.
2
Wire is not inserted far enough into terminal or splice. End of wire is not visible through
inspection hole of butt splice, or is not flush with (or slightly beyond) end of terminal wire
barrel or parallel splice.
3
AWG wire size does not match wire size stamped on terminal or splice crimping dies.
4
Wire insulation enters barrel.
Check for incorrect strip length.
5
Nicked or missing conductor strands.
6
Excessive flash on terminal or splice indicates wrong combination of wire, terminal,
splice, or tooling.