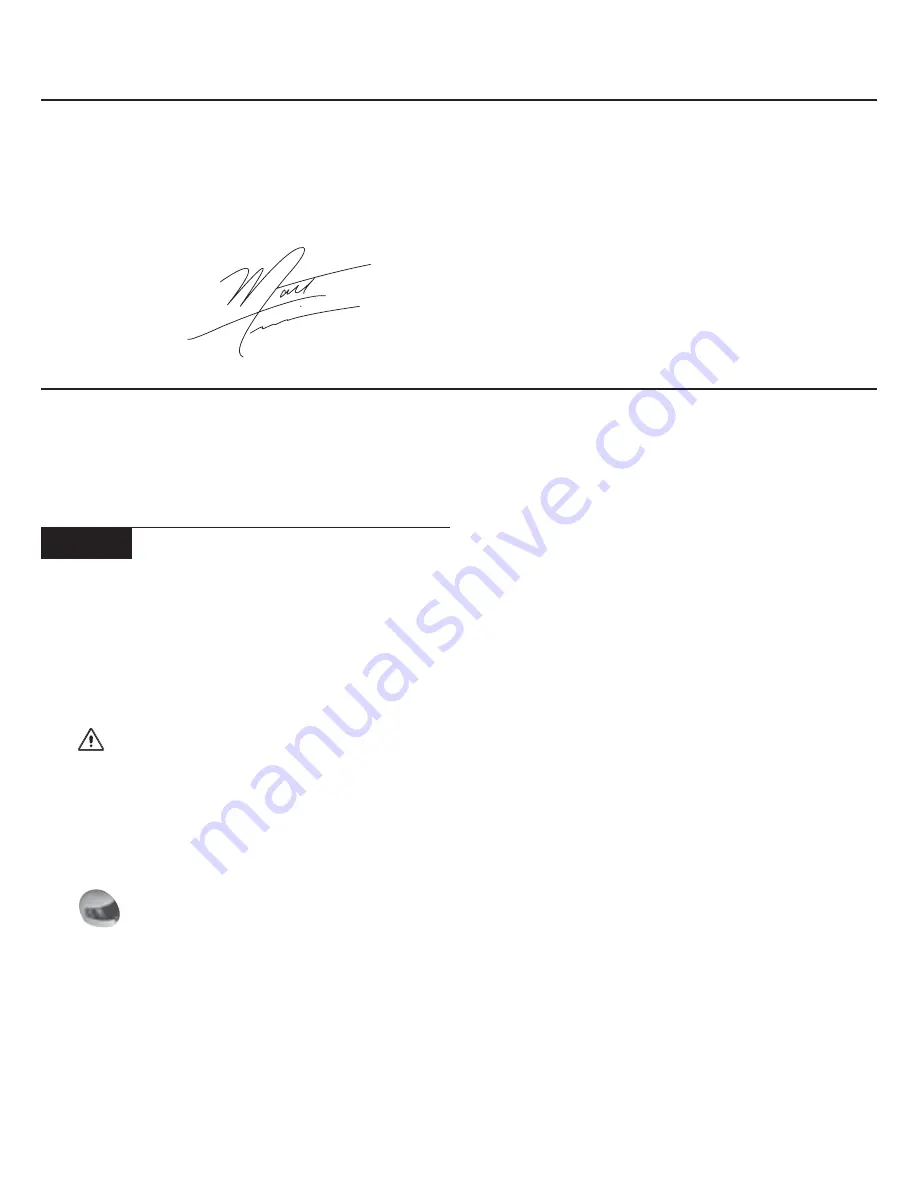
i
.
1. INTRODUCTION
TRIPLE-XT COMPLETED KIT DIMENSIONS
Length: 16.195"
Front Width: 12.725"
Rear Width: 12.875"
Height: 5.505"
Wheelbase: 11.050"
All dimensions at ride height.
Weight will vary depending on accessories.
NOTES & SYMBOLS USED
Figure 1
This is a common figure number found at the beginning
of each new illustration throughout the manual.
!
Step 1. - Each step throughout the entire manual has a
check box to the left of it. As you complete each step, mark the
box with a check. If you need to take a break and return to build-
ing at a later time you will be able to locate the exact step where
you left off.
*NOTE:
This is a common note. It is used to call attention to
specific details of a certain step in the assembly.
IMPORTANT NOTE:
Even if you are familiar with
Team Losi kits, be sure and pay attention to these notes. They
point out very important details during the assembly process. Do
not ignore these notes!
!
This wrench designates a performance tip. These tips
are not necessary, but can improve the performance of your
Triple-XT
truck.
In illustrations where it is important to note which
direction parts are facing, a helmet like this one will be included
in the illustration. The helmet will always face the front of the car.
Any reference to the right or left side will relate to the direction of
the helmet.
KIT/MANUAL ORGANIZATION
The kit is composed of different bags marked A through G. Each
bag contains all of the parts necessary to complete a particular
section of the
Triple-XT
. Some of these bags have subassembly
bags within them. It is essential that you open only one bag at a
time and follow the correct assembly sequence, otherwise you may
face difficulties in finding the correct part. It is helpful to read
through the instructions for an entire bag prior to beginning as-
sembly. Key numbers (in parenthesis) have been assigned to each
part and remain the same throughout the manual. In some illus-
trations, parts which have already been installed are not shown
so that the current steps can be illustrated more clearly.
For your convenience, an actual-size hardware identifica-
tion guide is included with each step. To check a part, hold it
against the silhouette until the correct part is identified. In some
cases extra hardware has been supplied for parts that may be
easy to lose.
The molded parts in the
Triple-XT
are manufactured to de-
manding tolerances. When screws are tightened to the point of
being snug, the parts are held firmly in place. For this reason it is
very important that screws not be overtightened in any of the
plastic parts.
To ensure that parts are not lost during construction, it is
recommended that you work over a towel or mat to prevent parts
from rolling away.
IMPORTANT SAFETY NOTES
1. Select an area for assembly that is away from the reach of
small children.
Some parts in this kit are small and can be swallowed
by children, causing choking and possible internal injury.
2. The shock fluid and greases supplied should be kept out
of childrens' reach.
They are not intended for human consumption!
3.
Exercise care
when using
any
hand tools, sharp instruments,
or power tools during construction.
4.
Carefully read all manufacturers' warnings and cautions
for
any glues, chemicals, or paints that may be used for assembly and
operating purposes.
Thank you for choosing the Team Losi
XXX-T Francis Edition
. Over the past year and a half I, along with Team
Losi engineers and staff members, have done extensive testing and tuning to give you the truck you just purchased. The set-up
included in this kit contains many of the specialty parts used on my 2001 ROAR Nationals and 2000 Winter Championships
winning truck. As you build your new
XXX-T Francis Edition
kit, be sure to read and follow the instructions carefully and
don't forget to check out the tuning tips in the back of this manual. I hope you will enjoy and wish you much success with your
new Team Losi
XXX-T Francis Edition
. See you at the track!
Good Luck!
XXX-T Matt Francis Edition
Summary of Contents for XXX-T Matt Francis Edition
Page 2: ......