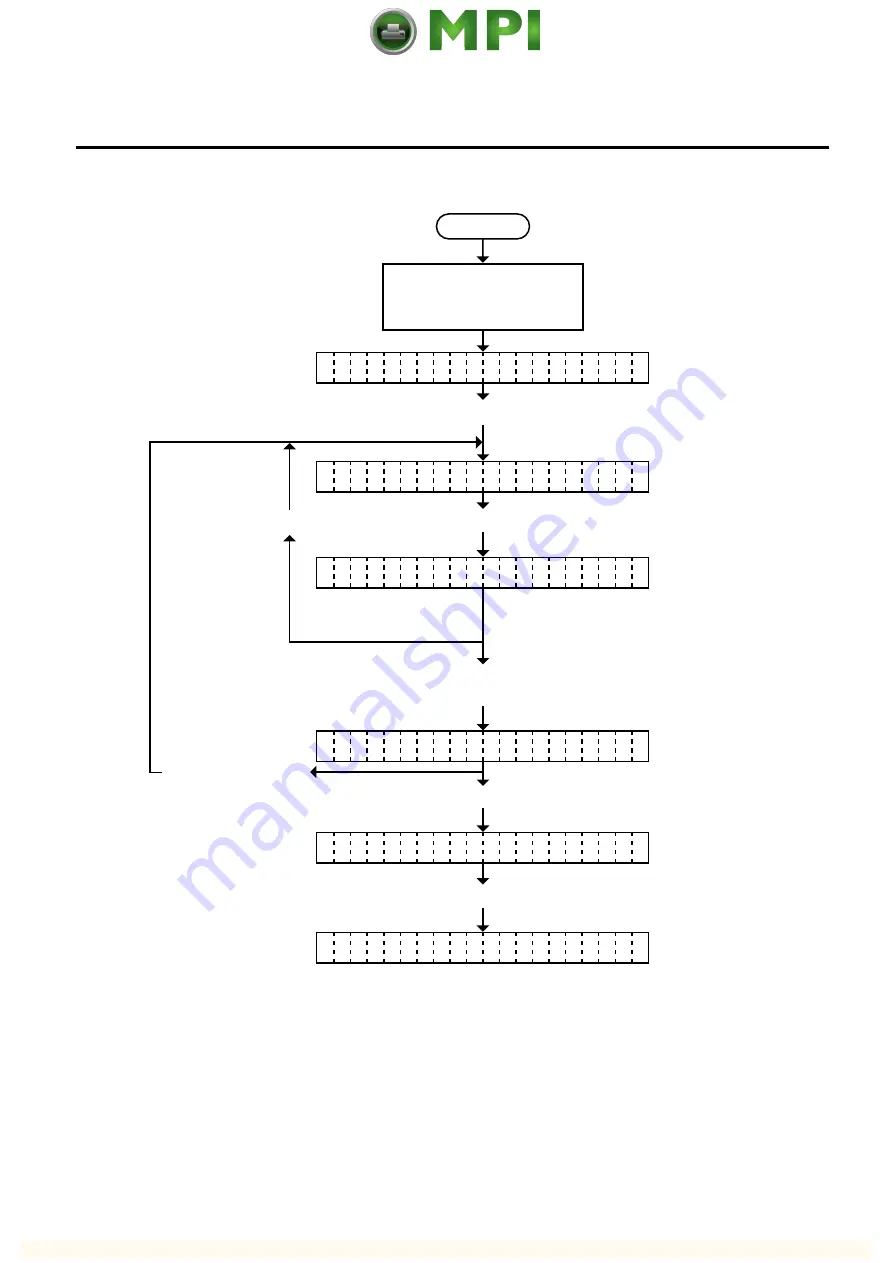
6-57
EM18-33017
6. DIAG. TEST OPERATION
Power off
Turn on the power while
holding down the [FEED]
key and [PAUSE] key.
< 1
D I A G N O S T I C
V 1 . O A
>
Press the [FEED] key four times.
< 5
R A M
C L E A R
>
C O
P L E T E
M
P A
A M E T E R
C L E A R
R
N O
R A M
C L E A R
Press the [PAUSE] key.
Press the [PAUSE] key.
Press the [FEED] key twice.
(or press the [RESTART] key.)
Press the [PAUSE] key.
Turn off the power (See NOTE 1)
Press the [FEED]
key and
[RESTART] key at
the same time.
NOTE:
Confirm that “COMPLETE” is displayed, then turn the power off.
6.6 RAM CLEAR MODE
6.6.2
Parameter Clear