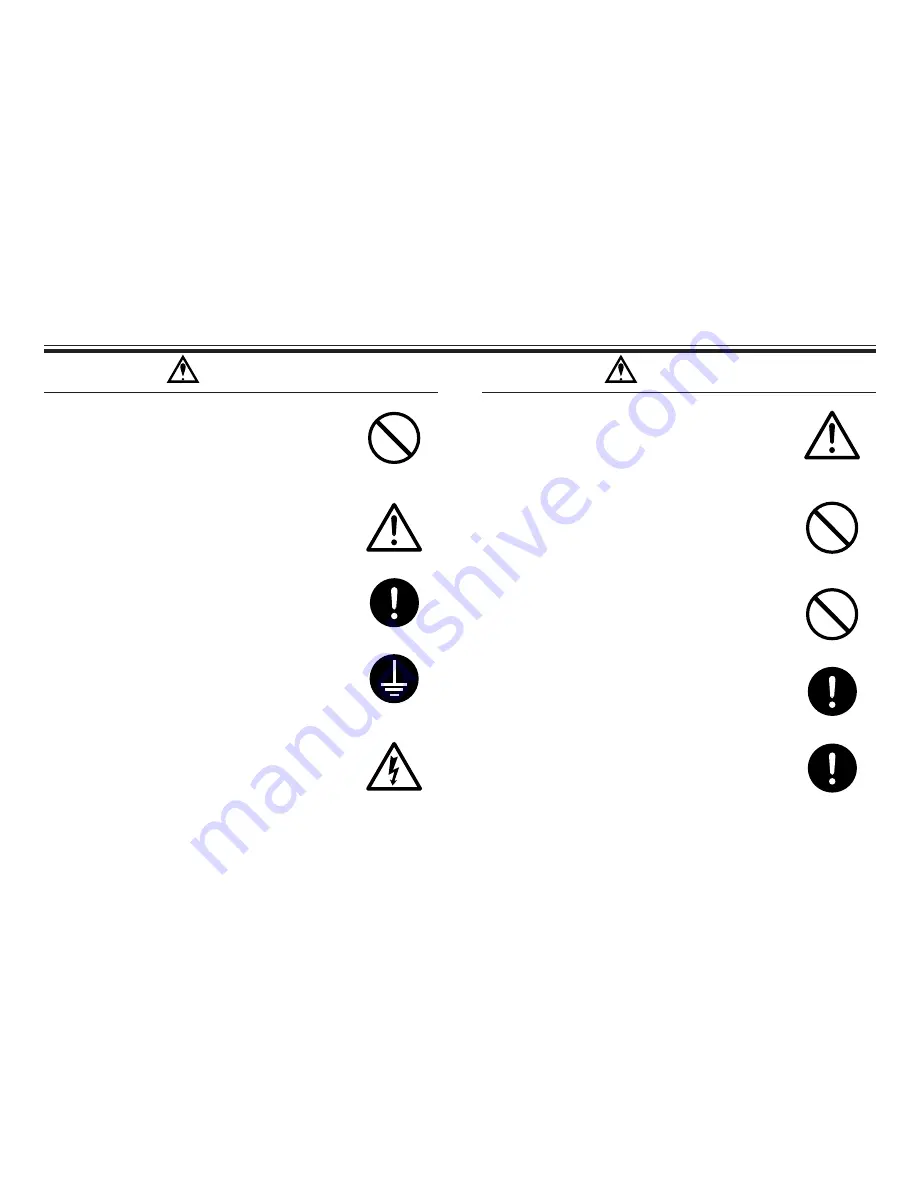
- 2 -
●
Operating site must be free of water and
humidity.
The pump is not designed to be water-proof or dust-proof.
The use of the pump in places where water splashes or
humidity is high may result in an electrical shock or short
circuit.
●
Do not damage power cable.
Do not scratch, damage, process, or pull the power cable
forcibly. An extra load onto the cable, such as heating the
cable or placing something heavy on the cable, may dam-
age the cable and finally cause a fire or an electrical shock.
●
Do not cover the motor.
Running a covered motor may accumulate heat inside the
motor and cause a fire or a mechanical failure. Ventilate
the motor sufficiently.
●
Arrange grounding.
Do not operate the pump without connecting the grounding
wire. Otherwise, an electrical shock may result. Make sure
the grounding wire is connected with the grounding termi-
nal.
●
Install an earth leakage breaker (option).
The operation of a pump without using an earth leakage
breaker may cause an electrical shock. Please purchase an
optional leakage breaker and install in the system.
Prohibited
●
Power cable cannot be replaced.
Never use a damaged or affected power cable. Otherwise,
a fire or an electrical shock may result. Handle the power
cable carefully, as it cannot to be replaced by a new cable.
(The complete motor must be replaced in that circum-
stance.)
●
Limited operating site and storage.
Do not install or store the pump in the following places:
* Places where a flammable gas or material is used or
stored.
* Places where the ambient temperature is extremely high
(40°C or higher) or extremely low (0°C or lower).
●
Do not drain the liquid in the site.
The liquid discharged out of the pump, including a haz-
ardous chemical liquid, must be drained into a special con-
tainer. Never drain such liquid directly onto the floor in or
near the operation site.
●
Disposal of used pump.
Disposal of used or damaged pumps must be done in
accordance with the relevant local laws and regulations.
(Consult a licensed industrial waste products disposing
company.)
●
Countermeasure for static electricity.
When low electric conductivity liquid such as ultra-pure
water and flour inactive liquid(e.g.Fluorinert
TM
) are han-
dled,the static electricity may be generated in pump,which
may cause static discharge and break down of pump. Take
countermeasure to avoid and remove static electricity.
Caution
Grounding
Electrical Shock
Caution
Prohibited
Prohibited
Caution
Caution
Summary of Contents for FSSR1
Page 1: ...Issue 1 02 07 FSSR1 Venturi Scrubber Unit OPERATOR S MANUAL ...
Page 7: ...1 Appendix 1 Scrubber Layout ...
Page 8: ...A3 ...
Page 9: ...Appendix 2 Operating and Maintenance Instructions for Pump ...
Page 10: ...Read this manual before use of product MD SERIES Instruction Manual IWAKI Magnetic Drive Pump ...