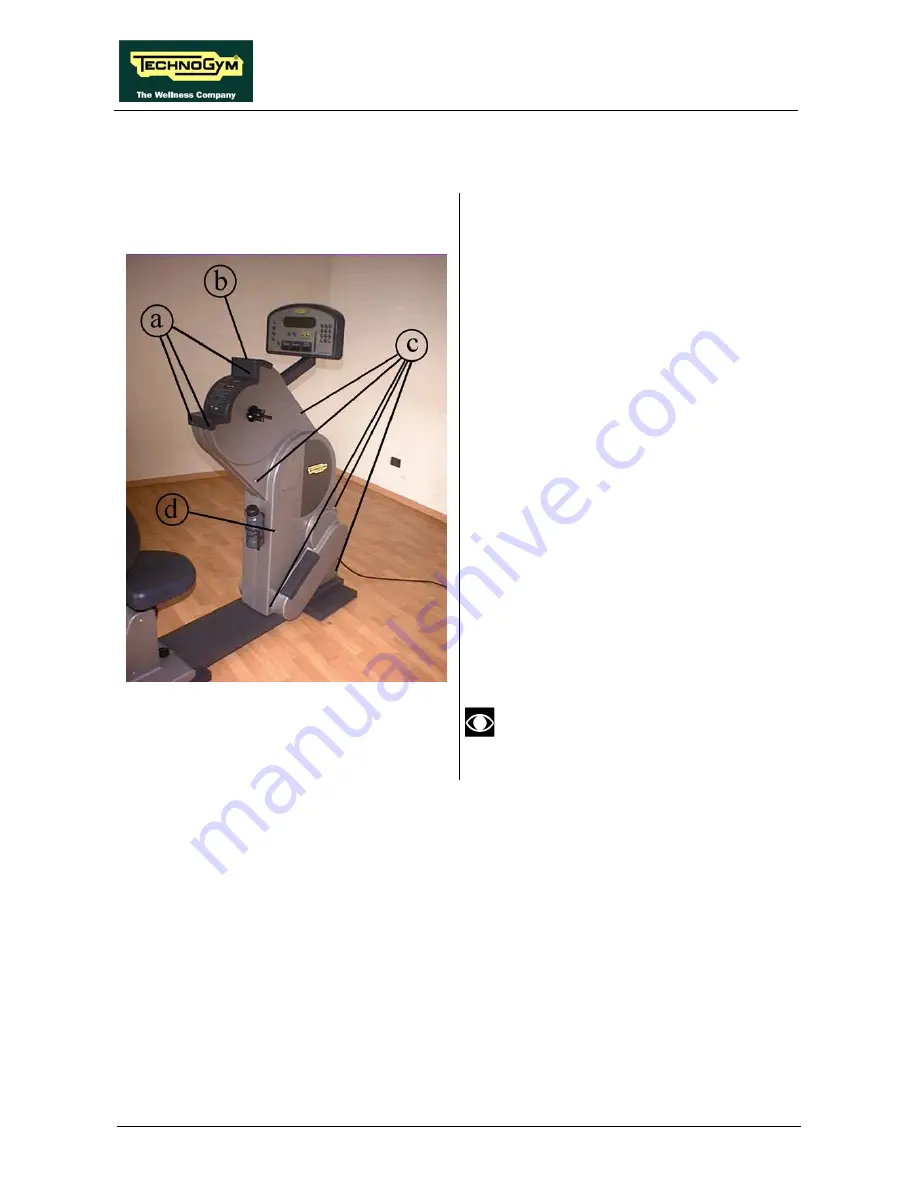
TOP 600 XTPRO: Service & Maintenance Manual - rev. 2.0
Page 7.6
7.6. DISASSEMBLING THE RIGHT AND LEFT SIDE CASINGS
Figure 7.6-1
Carry out the procedure described in paragraph
7.5. “Disassembling the arms”.
1. Remove the 4 screws
a
which secure the
lexan instruction panel
b
, using a large
Phillips screwdriver.
2. Remove the lexan instruction panel
b
.
3. Remove the 5 self-tapping screws
c
which
fix the LEFT GUARD to the frame, using a
large Phillips screwdriver.
4. Remove screw
d
using a large Phillips
screwdriver, while using another large
Phillips screwdriver to hold the opposing
screw on the RIGHT GUARD in place.
5. Remove the LEFT GUARD.
6. Unscrew the 5 self-tapping screws which fix
the RIGHT GUARD to the frame, using a
large Phillips screwdriver.
7. Remove the RIGHT GUARD.
To reassemble the GUARDS, carry out the
above steps in reverse order.
It is also possible to disassemble only
one of the 2 GUARDS.
Summary of Contents for Top 600 XTPRO
Page 1: ...SERVICE MAINTENANCE MANUAL REV 2 0...
Page 2: ......
Page 4: ......
Page 8: ...TOP 600 XTPRO Service Maintenance Manual rev 2 0 Page iv Page intentionally left blank...
Page 18: ...TOP 600 XTPRO Service Maintenance Manual rev 2 0 Page 2 8 Page intentionally left blank...
Page 26: ...TOP 600 XTPRO Service Maintenance Manual rev 2 0 Page 4 2 Page intentionally left blank...
Page 58: ...TOP 600 XTPRO Service Maintenance Manual rev 2 0 Page 7 18 Page intentionally left blank...
Page 70: ...TOP 600 XTPRO Service Maintenance Manual rev 2 0 Page 9 6 Page intentionally left blank...
Page 82: ......
Page 83: ...TOP 600 XTPRO Service Maintenance Manual rev 2 0 Page intentionally left blank Page 11 1...
Page 84: ......
Page 93: ......