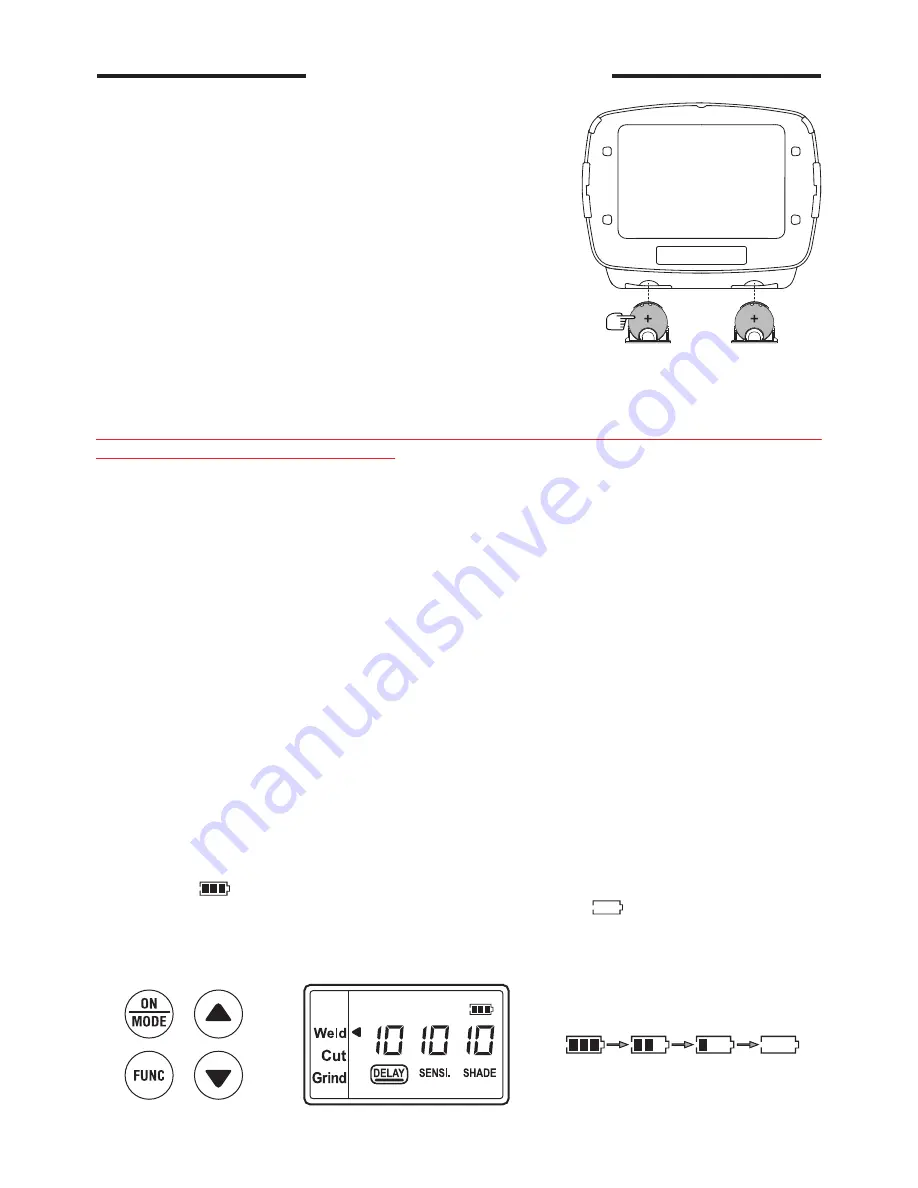
CARTRIDGE OPERATION
•
BATTERY INSTALLATION
Slide the battery holder out of the auto darkening filter,
(remove the used battery when replacing battery), put
new CR2450 batteries inside the battery holder, and put
the battery holder back into the auto darkening filter.
Please make sure the anode and cathode of the battery
are installed correctly (See fig.13).
• POWER ON / OFF
This auto darkening filter will automatically turn on when
pick it up.
Sensitivity level setting 0 - 9: The welding helmet will be
automatically off after 15 minutes not being used.
Sensitivity level setting =10: The filter will be darkening all
the time to meet some specially welding application under
both WELD MODE and CUTTING MODE. With this
setting, the welding helmet will not automatically turn off after 15 minutes of not being used.
To save power, remember to set the sensitivity value between 0 - 9 and keep the filter
in dark place when not being used.
• DIGITAL SCREEN ACTIVATION
Press any of four button to activate the digital screen (See fig.14a). After 6 seconds, digital
screen will automatically turn to standby mode. Short press the button again will active the
screen once more and previous settings will remain.
• MODE CONTROL
Short Press “ON / MODE” button to select the mode appropriate for the work activity
(See fig.14a):
Weld Mode
− used for most welding applications. Push “FUNC” button to adjust shade
number, sensitivity, and delay settings properly before welding. In this mode the lens turns to
dark immediately when you start welding.
Cutting Mode
− used for cutting applications. Push “FUNC” button to adjust shade number,
sensitivity, and delay settings properly before cutting. In this mode the lens turns to dark
immediately when you start cutting.
Grind Mode
− used for grinding applications. In this mode the lens shade is fixed shade No.
4. Can not adjust shade number, sensitivity, and delay settings.
• BATTERY INDICATOR
The symbol “ ” show the current state of the battery (See fig.14b). The volume of batteries
has four levels symbol to appear (See fig.14c). The symbol “ ” appears on the display
screen
before 1−2 days of battery life remains, the CR2450 lithium batteries should be
replaced in time. The symbol of the Battery Indicator is not real-time, should be updated
after pressing “ON / MODE” button shortly.
Be sure Positive (+) side of
battery faces up.
fig.14a
fig.14b
fig.14c
fig.13
• VARIABLE SHADE CONTROL
After turn on the lens, short press “FUNC” button to choose “SHADE”, and adjust the lens
shade number. Use “ ” and “ ” buttons to select the lens shade in the dark state. The shade
range for each mode are as follows:
Cutting Mode
−
Shade 5 ~ 8 (See fig.15a)
Weld Mode
−
Shade 9 ~ 13 (See fig.15b)
Grind Mode
−
No. 4 only (See fig.15c)
Select the proper shade number for your welding / cutting process, by referring to the “Shade
Guide Table” on page 19.
• SENSITIVITY CONTROL
Press “FUNC” button to choose “SENSITIVITY”. Use “ ” and “ ” buttons to make the lens
more or less sensitive to arc light of different welding processes. Sensitivity setting 5-10 is
the normal setting for everyday use. The sensitivity ranges for each mode are as follows:
Cutting Mode
(Shade 5 ~ 8) /
Weld Mode
(Shade 9 ~ 13)
−
Sensitivity 0 ~ 10 (See fig.16a /
16b)
Grind Mode
− No sensitivity adjustment
As a simple rule for optimum performance, it is recommended to set sensitivity to the
maximum at the beginning and then gradually reduce it, until the filter reacts only to the
welding light flash and without annoying spurious triggering due to ambient light conditions
(direct sun, intensive artificial light, neighbouring welder's arcs etc.).
It may be necessary to adjust helmet sensitivity to accommodate different lighting conditions
or if lens is flashing On and Off. Adjust helmet sensitivity as follows: Adjust helmet sensitivity
in lighting conditions helmet will be used in.
• Press “ ” button to lower setting to 0.
• Face the helmet in the direction of use, exposing it to the surrounding light conditions.
• Press “ ” button repeatedly until the lens darkens, then press “ ” button until
lens clears.
Helmet is ready for use. Slight readjustment may be necessary for certain applications or if
lens is flashing on and off.
• DELAY CONTROL
Press “FUNC” button to choose “DELAY”, begin lens delay adjustments. Use the Lens Delay
Control “ ” and “ ” buttons to adjust the time for the lens to switch to the clear state after
welding or cutting.
Cutting Mode
(Shade 5 ~ 8) /
Weld Mode
(Shade 9 ~ 13)
−
Delay 0 ~ 10 (See fig.17a / 17b)
Grind Mode
− No sensitivity adjustment
The delay is particularly useful in eliminating bright after-rays present in higher amperage
applications where the molten puddle remains bright momentarily after welding. Use the
Lens Delay Control buttons to adjust delay from 0 to 10 (0.1 to 1.0 second). When welding
stopped, the viewing window automatically changes from dark back to light but with a
pre-set delay to compensate for any bright afterglow on the workpiece. The delay time /
response can be set from Level 0 to level 10. It is recommended to use a shorter delay
with spot welding applications and a longer delay with applications using higher currents.
Longer delays can also be used for low current TIG welding, and TIG / MIG / MAG pulse.
•
ADJUSTING THE FIT OF THE HELMET
The overall circumference of the headband can be made larger or smaller by rotating the
knob on the back of the headband (See adjustment “Y” in fig.18). This can be done while
wearing the helmet and allows just the right tension to be set to keep the helmet firmly on
the head without it being too tight.
•
If the headband is riding too high or too low on your head, adjust the strap which passes
over the top of your head. To do this release the end of the band by pushing the locking pin
out of the hole in the band. Slide the two portions of the band to a greater or lesser width
as required and push the locking pin through the nearest hole (See adjustment “W” in
fig.18).
•
Front and back bands will automatically self-adjust according to headform, and soft pads
suit forehead and back of head perfectly, which will bring more comfort (See fig.19a). Test
the fit of the headband by lifting up and closing down the helmet a few times while wearing
it. If the headband moves while tilting, re-adjust it until it is stable.
•
ADJUSTING THE DISTANCE BETWEEN THE HELMET AND THE FACE
Step 1: Press down and hold the “LOCK” latch on both sides (See fig.19b) and it can be
slide back and forth.
Step 2: Loosen the “LOCK” latch and keep it snap into slots. Please make sure the
distance between the lens to both eyes are equal, to avoid uneven darkness.
• ADJUSTING VIEW ANGLE POSITION
Tilt adjustment is located on right side of helmet. Loosen the right headgear tension knob
and adjust the lever forward or back to the proper position. Re-tighten the right headgear
tension knob (See fig.19c).
13