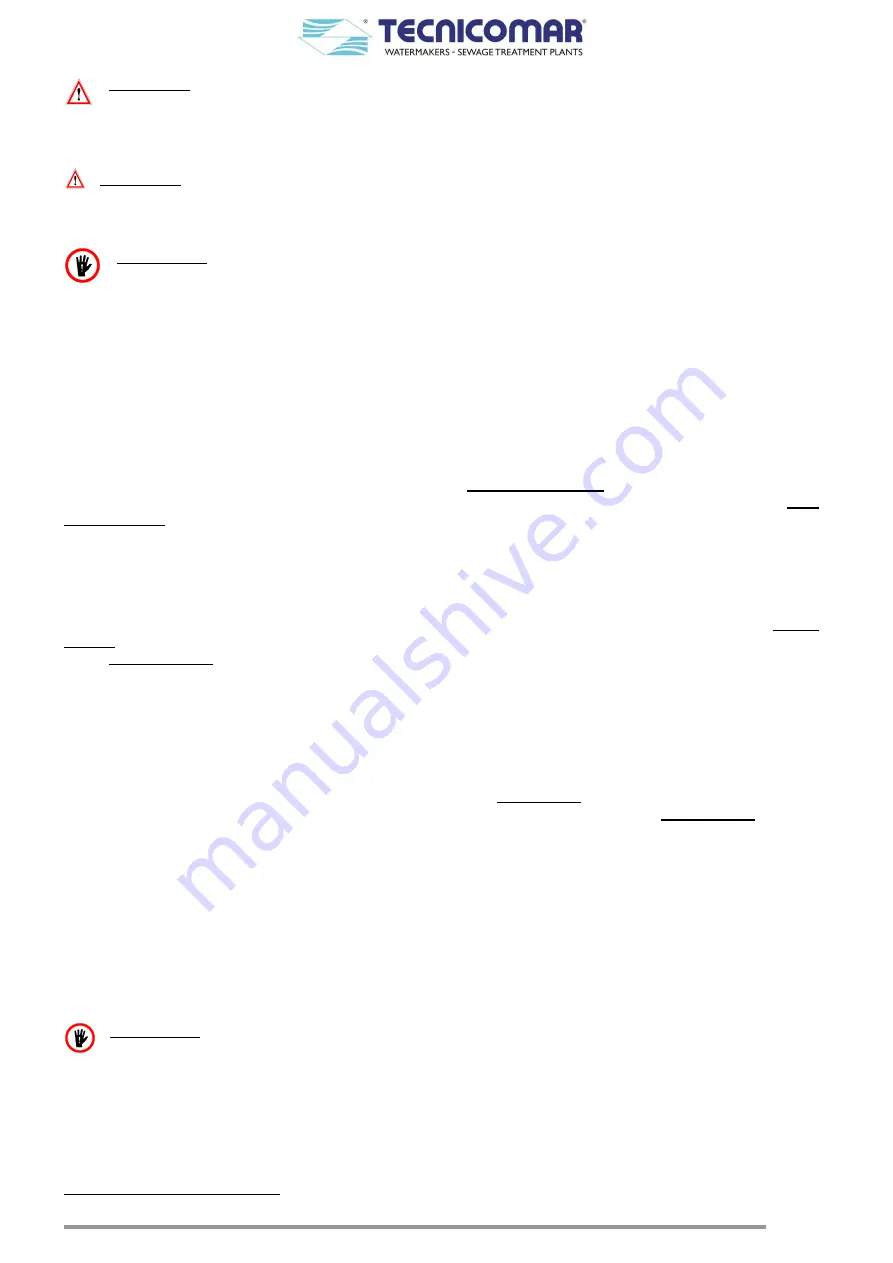
62
WARNING:
When pump is not used, never forget liquid inside pump casing during cold weather!
Water may freeze and break the pump casing.
Before restarting the unit, check that the shaft is not jammed and fill the pump casing completely with liquid.
Each 3 months, if necessary, lubricate the mechanical seal. If after seal lubrication, the pump continues to leak replace the seal.
When it is necessary to replace the mechanical seal, clean well, with water or with ethyl alcohol, the seat on the delivery case.
WARNING:
Do not use grease, soap, hand cream etc. These products will damage the mechanical seal of the pump.
Each 6 months open the inspection cover or the casing and check inside. Remove possible foreign parts blocked inside the
casing. Flush the pump with clean water before draining. Clean the pump and the motor. If necessary, check more frequently.
Each 5-10 years make a general pump recondition.
ATTENTION
: Never run the pump dry. Start the pump only after filling completely with liquid. FILL THE PUMP
WITH LIQUID BEFORE STARTING. NEVER LET THE PUMP RUN DRY.
14.2.3
Treatment Tank Level probes instructions
To ensure the correct functioning of the plant, it is recommended to make periodic inspections of the probe to check the
presence of any incrustations on each floating element; and to clean well the probe to remove the incrustations, if present.
14.2.4
Pressure switch
The pressure switch installed on the main unit treatment tank is maintenance free. However, tests should be carried out once a
year, to verify the correct setting of the pressure threshold (refer to
High Pressure Alarm
section).
If the pressure switch threshold is not that indicated in the attached Test report, it is recommended to re-set it (refer to
High
Pressure Alarm
section). If the pressure switch does not work properly, it is recommended to replace it.
14.2.5
Dosing Systems (H
2
O
2
& ECOFLOC) instructions
Check each dosing pump operating condition at least every 6 months, pump head position, screws, bolts and seals.
While each dosing pump is running, especially verify the correct setting of the flow regulation knob (refer to the
System
Settings
section); and the ignition of the injection pulse LED, of the 100% flow full-scale LED and of the power on LED (refer
to the
System Settings
section). Also check the injected solution concentration in the pipework, a reduction of this
concentration could be caused by the wearing of the valves, in which case they need to be replaced; or by the clogging of the
filter which then has to be cleaned. It is suggested to periodically clean off the hydraulic parts (valves and filter).
Periodically check the tank for any leakage or damage and repair or replace it if necessary.
Check the level of the chemical solution inside the tank, and refill it before the liquid ends up.
While the ECOmar S STP is running periodically check that each dosing pump is correctly running; if it is not running verify
the cause of the problem, fix it and restart the pump.
To check the cause of problem, firstly check the correct connection of each dosing pump (refer to attached Electrical Drawings).
Then verify the correct setting of the flow regulation knob and of the Dosing Timer parameter. At this point, if the dosing
pumps does not still start, press the pump START pump and activate it in manual mode (refer to
Manual mode
section) to
verify its functioning. If the problem is still not solved, dismount the suction and discharge valves of the interested dosing
pump, clean them and replace. If this check is not successful, check clogging of the filter and clean or replace it clogged or
damaged. Finally if all the previous checks have been not successful, the dosing pump is damaged and must be replaced.
14.2.6
Seawater pump instructions
Before any maintenance, disconnect the power supply and make sure the pump cannot be accidentally switched on.
Periodically check that the pump works within its field of performance, and that absorbed current shown on the name-plate is
not exceeded. When the pump is located above the water level (suction lift operation), make sure that the suction pipe and the
pump are always totally filled with liquid.
ATTENTION
: Never run the pump dry. Start the pump only after filling completely with liquid. FILL THE PUMP
WITH LIQUID BEFORE STARTING. NEVER LET THE PUMP RUN DRY.
The mechanical seal does not require any preventive maintenance and must be replaced only if the pump is leaking. When the
pump is not used, empty it completely if freezing may be expected. Flush the pump with clean water before draining. Remove
the drain plug and totally empty the pump.
Before restarting the unit, check that the shaft is not jammed and fill the pump casing completely with liquid.
For pump dismantling close the suction and delivery valves and drain the pump casing before dismantling the pump.
For dismantling and re-assembly see construction in the cross section drawing.
*
Only for ECOmar S supplied with Treatment Tank in PP.