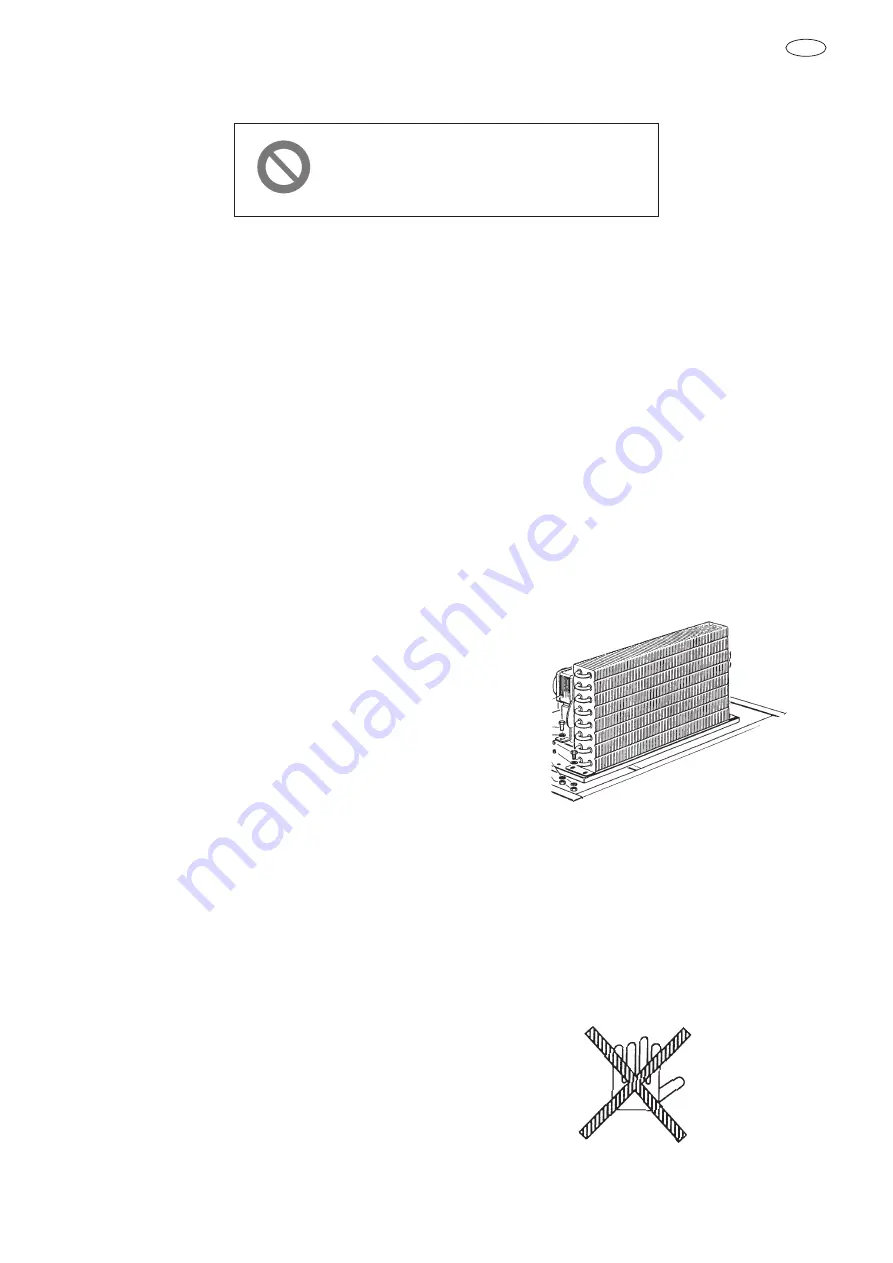
GB
57
The information and instructions given in this
section address all persons operating the
appliance: the user, the maintenance techni-
cian and non-specialised personnel.
Ensure that the electrical power to the
system has been disconnected before
carrying out any cleaning or maintenance
work on the appliance.
8.1
GENERAL SAFETY REGULATIONS
Recall the following regulations to ensure
that all cleaning and routine maintenance
operations are conducted safely.
- do not touch the machine with moist or
wet hands or feet;
- never operate the machine while bare-
foot; - do not insert screwdrivers, cooking
utensils or any other object between the
guards and moving parts.
- before performing cleaning or routine
maintenance operations, disconnect the
machine from the power supply at the
master switch and by pulling out the
plug;
- never pull on the power cable to discon-
nect the machine from the power supply.
Removal of guards and safety devices
for the purposes of routine maintenance
is strictly prohibited. The manufacturer
declines all responsibility for accidents
causedby failure to observe the above
regulation.
Before starting up the appliance, clean
the inside of the cell thoroughly, as
described in par. 8.3.
8.2
CLEANING THE CONDENSER
To ensure correct and efficient air con-
denser operation, it must be kept clean to
allow free circulation of air. This operation
should be performed at least once a
month. Use a non-metal brush to remove
all dust and debris from the condenser
blades.
Use a vacuum cleaner to prevent the
dust removed from being dispersed in
the surrounding area. To remove greasy
deposits, use a brush dipped in alcohol.
NEVER USE POINTED OR ABRASIVE
INSTRUMENTS TO SCRAPE APPLIANCE
SURFACES.
PERFORM THIS OPERATION ONLY
AFTER THE APPLIANCE HAS BEEN
SHUT DOWN
IMPORTANT
The condenser has sharp edges. Always
wear protective gloves, goggles and masks
when carrying out the above operations.
8. MAINTENANCE AND CLEANING
W
W
W
W
A
A
A
A
R
R
R
R
N
N
N
N
II
II
N
N
N
N
G
G
G
G
!!
!!
!!
!!
!!
!!
THESE OPERATIONS MUST BE PERFORMED
BY A CERTIFIED INSTALLATION
TECHNICIAN ONLY.