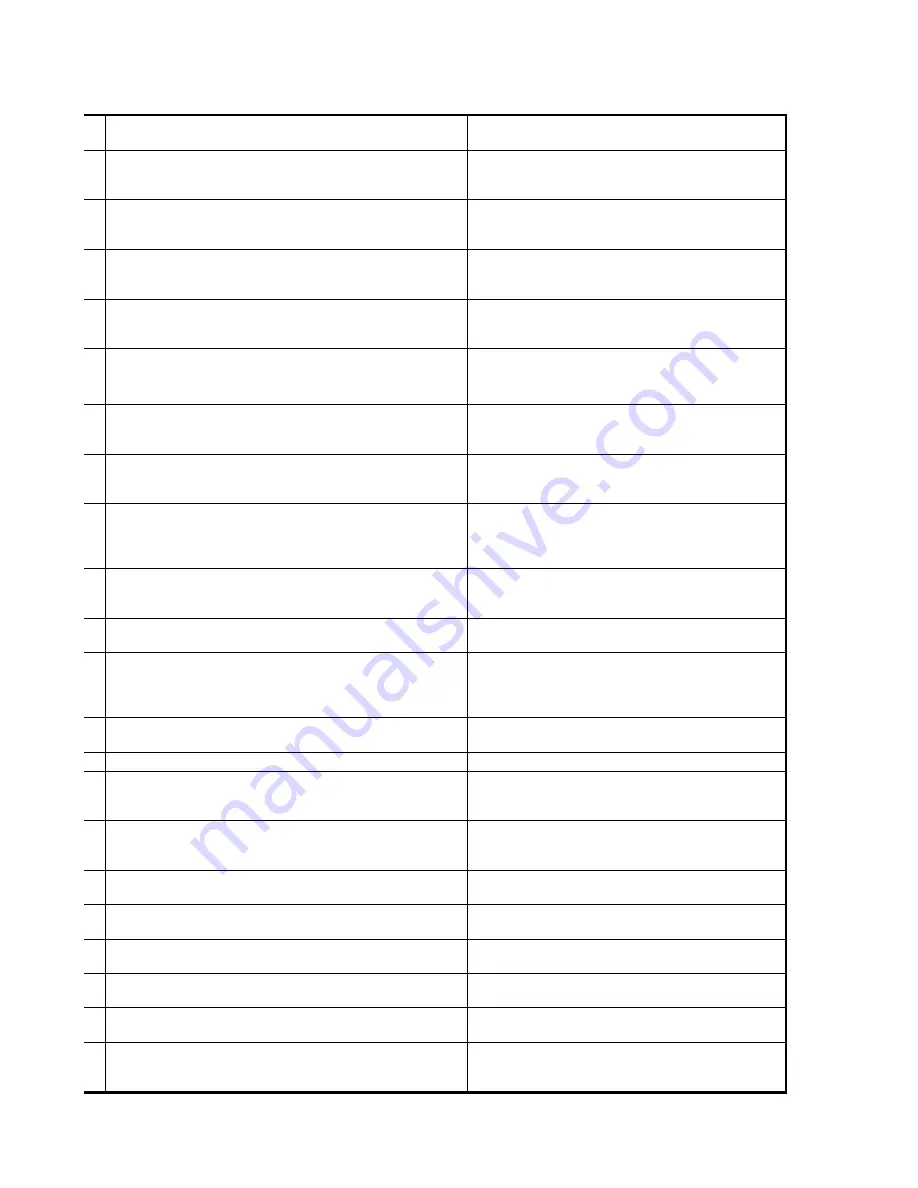
4-5
Error Causes
Action to Be Taken
•
Input voltage drop
•
Measure the main circuit DC voltage, if the
voltage is lower allowance level, regulate the
input voltage.
•
Input voltage rise
•
Measure the main circuit DC voltage, if the
voltage is higher than allowance level, regulate
the input voltage.
•
Overload
•
Cooling fan fault. Ambient temperature rises.
•
Clogged filter.
•
Check for the fan, filter and the ambient
temperature.
•
Machine error or overload
•
Check the use of the machine.
•
Set a higher protection level (Cn-32).
•
Insufficient Accel./Decel. Time
•
Overload
•
Excessive load impact occurs while operating
•
Increase Accel./Decel. Time.
•
Check the load.
•
Operation sequence error
•
3-wire/2-wire selection error
•
Check the circuit of system
•
Check the setting of system parameters Sn-25,
26, 27, and 28.
•
External noise
•
Excessive vibration or impact on Communication wire
•
Not properly contacted
•
Check the parameter setting, including Sn-01, Sn-02.
•
Check if the comm. wire is not properly contacted.
•
Restart, if fault remains, please contact to us.
•
Comm. between digital operator and inverter has not
been established after system starts for 5 seconds.
•
Communication is established after system starts, but
transmission fault occurs for 2 seconds.
•
Re-plug the connector of the digital operators.
•
Replace the control board.
•
External B.B. signal is input.
•
After external BB signal is removed, execute the
speed search of the inverter.
•
Inverter KVA setting error.
•
Set proper KVA value. Be aware of the
difference of
230
V and
460
V
•
The value of Sn-25~Sn-28 is not in ascending order (Ex.
Sn-25= 05, Sn-28= 02, those are improper setting).
•
Set speed search command of 21 and 22 simultaneously.
•
Set these values by order (the value of Sn-25
must be smaller than those of Sn-26, 27, 28)
•
Command 21 and 22 can not be set on two multi-
function-input contacts simultaneously.
•
The values of Cn-02~Cn-08 do not satisfy
F
max
≥
F
A
≥
F
B
≥
F
min
.
•
Change the settings.
•
Upper limit and lower limit setting is incorrect.
•
Change the settings.
•
Improper ASR parameter setting or over-torque
protection level.
•
Check the ASR parameter and over-torque
protection level.
•
The circuit of PG is not properly connected or open-
circuit.
•
Check the wiring of PG.
•
Improper ASR parameter setting or over-torque
protection level.
•
Check the ASR parameter and over-torque
protection level.
•
Bad communication during operator and inverter.
•
The connector is not properly connected.
•
Check if the connector is not properly connected.
•
Operator EEPROM error.
•
Disable load function of operator.
•
Replace the operator.
•
Incorrect inverter data format
•
Communication noise.
•
Download the data to the operator again.
•
Check if the connector is not properly connected.
•
Communication noise
•
Check if the connector is not properly connected.
•
Inverter capacity and motor rating are not properly matched.
•
The wiring between inverter and motor is disconnected.
•
Motor load unbalance.
•
Correct the inverter/motor capacity ratio, wiring
cable and motor load.