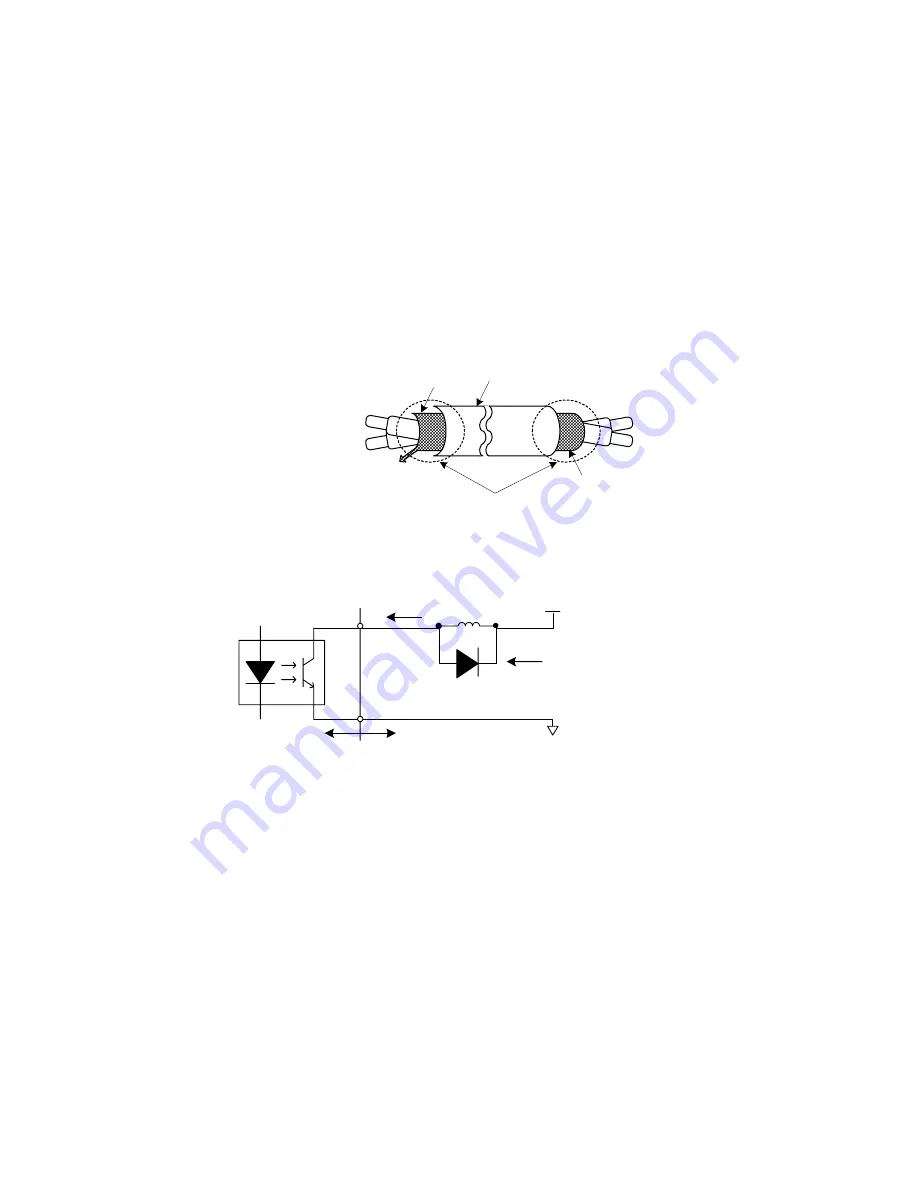
1-15
■
External circuit wiring precaution:
(A) Control circuit wiring:
(1)
Separate the control circuit wiring from main circuit wiring (R/L1, S/L2, T/L3, U/T1,
V/T2, W/T3) and other high-power lines to avoid noise interruption.
(2)
Separate the wiring for control circuit terminals RA-RB-RC (R1A-R2B-R2C) (contact
output) from wiring for terminals
c
~
j
, A01, A02, GND,
DO1, DO2 ,
DOG 15V
(or
+12V, -12V)
, VIN, AIN, AUX, GND, IP12, IG12, A (+), A (-),
S(+) and S(-)
.
(3)
Use the twisted-pair or shielded twisted-pair cables for control circuits to prevent
operating faults. Process the cable ends as shown in Fig. 3. The max. wiring distance
should not exceed 50 meter.
Connect to shield
sheath terminal E
Shield sheath
Armor
Do not
connect here
Insulated with tape
Fig. 3.
Processing the ends of twisted-pair cables
When the digital multi-function output terminals connect serially to an external relay, an
anti-parallel freewheeling diode should be applied at both ends of relay, as shown below.
free-wheeling diode
(100V, >100mA)
48V max.
50 mA max.
7200MA
external wiring circuit
Fig. 4.
The Optical-couplers connect to external inductive load
(B) Wiring the main circuit terminals:
(1)
Input power supply can be connected to any terminal R/L1, S/L2 or T/L3 on the
terminal block. The phase sequence of input power supply is irrelevant to the phase
sequence.
(2)
Never connect the AC power source to the output terminals U/T1, V/T2 and. W/T3.
(3)
Connect the output terminals U/T1, V/T2, W/T3 to motor lead wires U/T1, V/T2, and
W/T3, respectively.
(4)
Check that the motor rotates forward with the forward run source. Switch over any 2
of the output terminals to each other and reconnect if the motor rotates in reverse with
the forward run source.
(5)
Never connect a phase advancing capacitor or LC/RC noise filter to an output cir
cuit.
MA7200