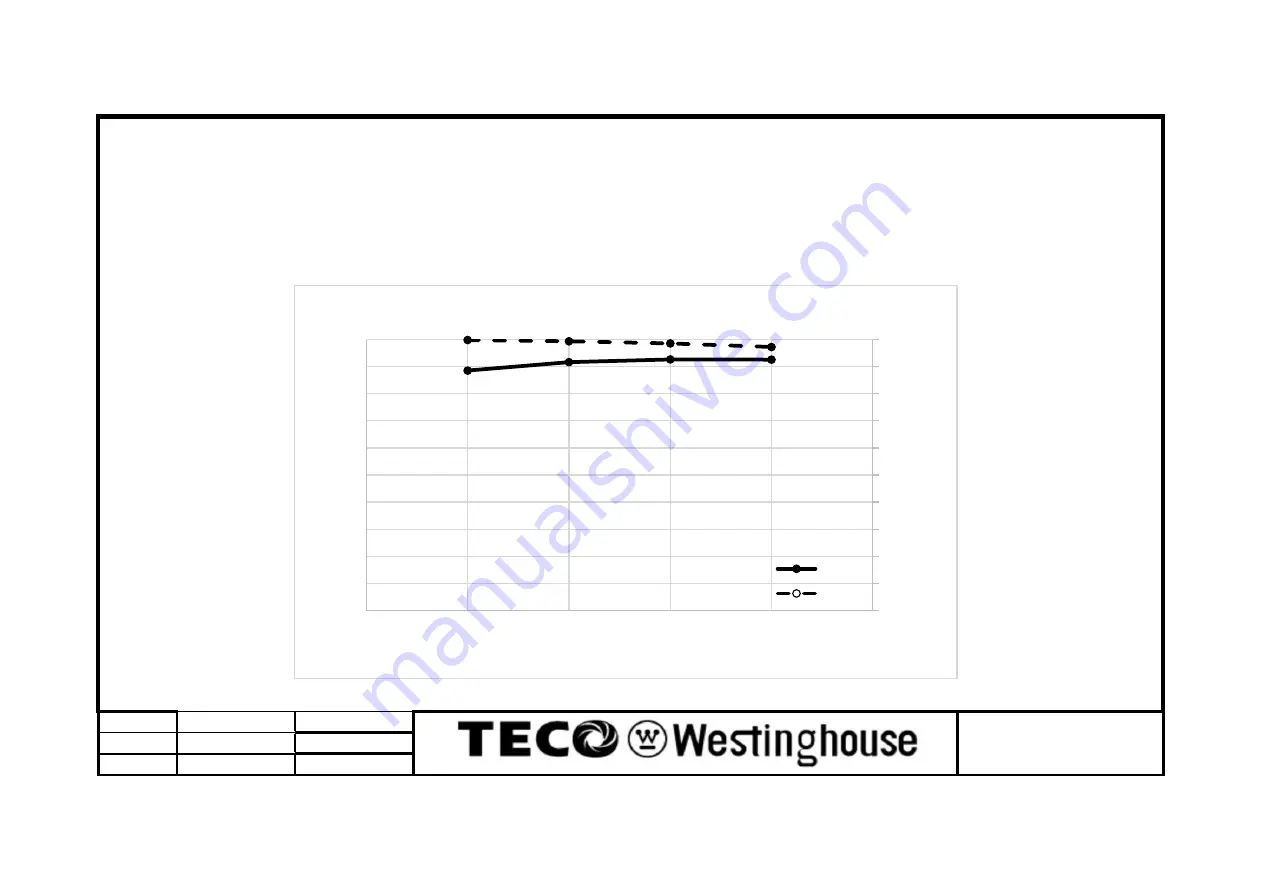
NO.: TDTPM19701006
TYPE: DVEM
POLE: 6
HP : 10
VOLT.: 460
APPD.
Wanghy
20190726
DWG NO.
Rev.00
CHKD.
Mingte
20190726
DWN.
P.J. Huang
20190726
TDTPM19701006
Efficiency&Power Factor
Efficiency & Power Factor CURVE
0
10
20
30
40
50
60
70
80
90
100
0
10
20
30
40
50
60
70
80
90
100
0
25
50
75
100
125
P
ow
e
r
Fa
ct
or
(%)
Ef
fi
ci
e
n
cy(
%)
Load(%)
Efficiency & Power Factor Curve(10 HP_1800rpm)
Eff.
PF
Summary of Contents for MAX-PM
Page 1: ......
Page 3: ......
Page 4: ......
Page 7: ...1BW0 A1 C LD 426 High Efficiency Permanent Magnet Synchronous Motor Instruction Manual ...