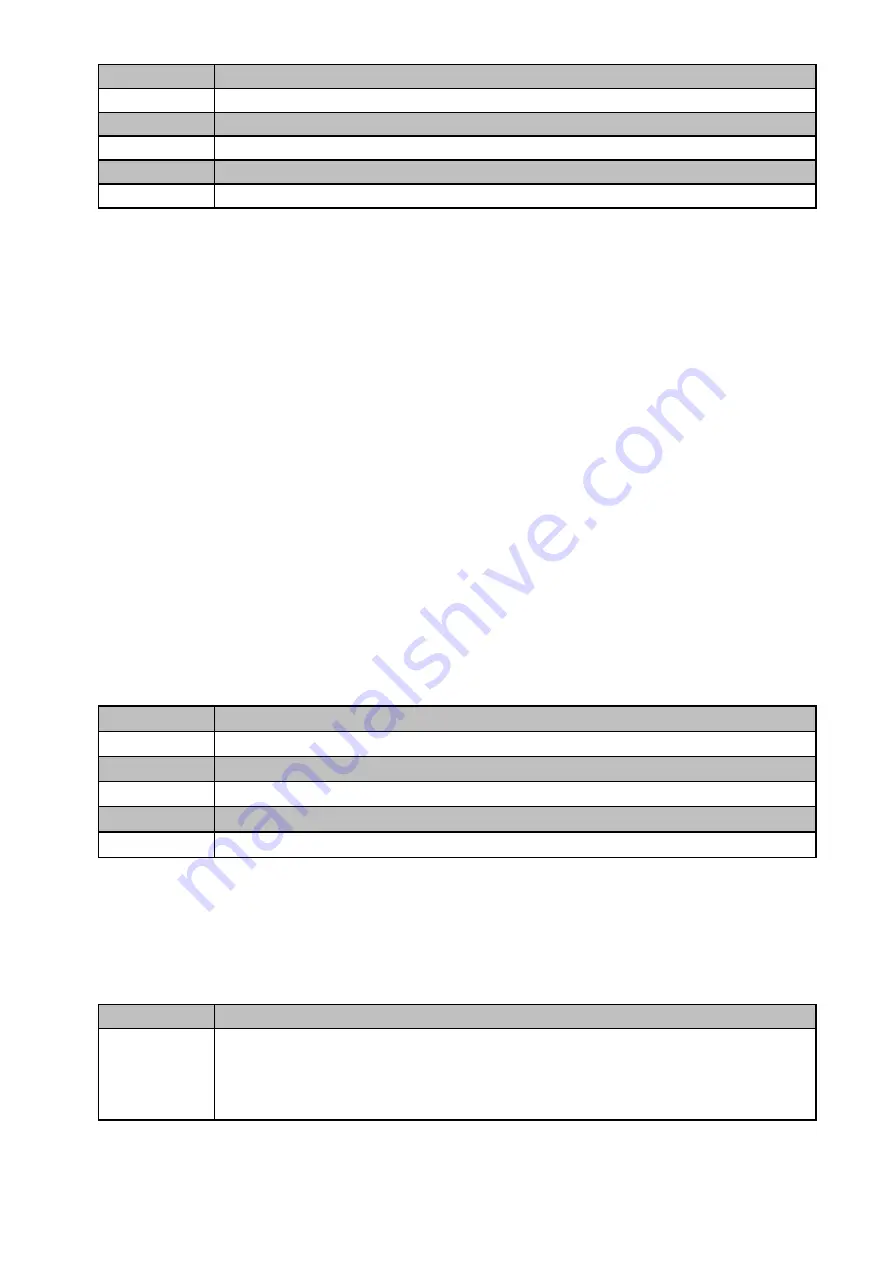
4
-
149
07- 07
DC Injection Braking Level
Range
【
0~100
】%
07- 08
DC Injection Braking time
Range
【
0.00~100.00
】Sec
07- 16
DC injection braking time at start
Range
【
0.00~100.00
】Sec
Set parameter 07-06, 07-08 and 07-16 for DC injection braking related function.
When inverter executes speed search function, DC injection braking function should be
disabled.
To enable DC injection braking during a start operation set the DC injection braking current
(07-07) and the DC injection braking time (07-16) at start to a value greater than 0. DC injection
braking at start can be used to prevent
“
wind milling effect
”
in fan applications.
To enable DC injection braking during a stop operation set the DC injection braking current
(07-07) and the DC injection braking time at stop (07-08) to a value greater than 0.
When parameter 07-16 is set to 0 sec (DC injection braking off). the inverter will start from the
minimum output frequency duration of DC injection braking during a stop operation. DC
injection braking at stop is disabled when parameter 07-08 is set to 0 sec. If output frequency is
less than 07-06, injection braking function will be enabled. Inverter output will be cut off and
then DC injection braking is started.
During stop operation: If the DC braking start frequency < minimum output frequency (01-08),
DC braking is active when the output frequency reaches the minimum output frequency level.
DC injection braking level can be set by parameter 07-07 in acceleration and deceleration, DC
injection current can be part of output rated current. (Suppose rated current of inverter is
100%)
Increasing the DC braking current (07-07) can reduce the motor stop time.
DC braking operation can be controlled via any one of the multi-function input terminals(03-00
to 05) function 33. Refer to figure 4.3.
57
for DC braking operation.
07- 34
Start short-circuit braking time
Range
【0.00~100.00】Sec
07- 35
Stop Short-circuit braking time
Range
【0.00~100.00】Sec
07- 36
Short-circuit braking current limited
Range
【0.0~200.0】%
PMSLV is available for short-circuit braking. Short-circuit braking is the way to switch IGBT to
produce braking torque. 07-06, 07-34 and 07-36 can adjust the braking process.
If 07-35=0, Inverter start from the minimum frequency.
The value of 07-36 is depend on differential motor rated current.
03-00~03-07=65 can control Short-circuit braking.
07- 09
Stop Mode Selection
Range
【0】:
Deceleration to stop
【
1】:
Coast to stop
【2】:
DC braking to stop
【
3】:
Coast to stop with timer
When a stop command is issued the inverter stops according to the stop mode selected. There are
four types of stop modes.
Note:PM motor only can select
“
deceleration to stop mode
”
and
“
coast to stop mode
”
.
Summary of Contents for E510-201-SH
Page 1: ......
Page 28: ...3 14 b 200V 2HP 1 3PH 200V 3HP 20HP 400V 3HP 25HP IP20 NEMA1 ...
Page 29: ...3 15 c 200V 25HP 400V 30HP d 200V 30HP 40HP 400V 40HP 75HP ...
Page 51: ...3 37 3 5 Standard Wiring 10V AI1 AI2 AGND E P P ...
Page 72: ...4 6 4 1 4 Example of keypad operation Example 1 Modifying parameters ...
Page 74: ...4 8 4 1 5 Operation control ...
Page 206: ...4 140 Acceleration Deceleration calculation of mode 2 ...
Page 316: ...4 250 6 Timer mode 6 FLASH Timer mode 2 7 Timer mode 7 FLASH Timer mode 3 ...
Page 424: ...REVISIONS Date Manual Number Revision May 2017 4KA72X645T01 First edition ...
Page 425: ......