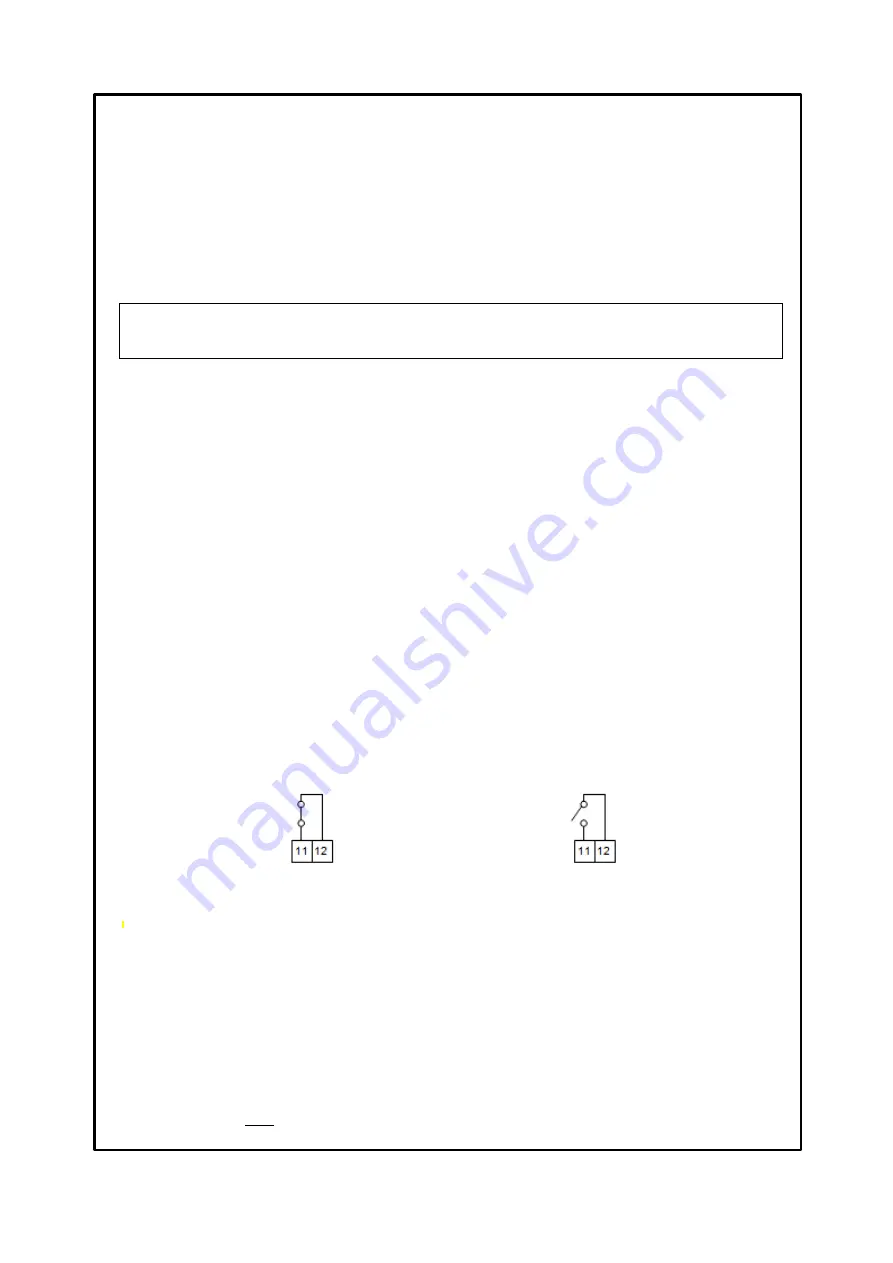
16
FO 935 ETH
ALARMS AND VENTILATION
Carry out the electrical connections on the removable terminal blocks only after disconnecting them from the unit.
When the control unit is in one of the modes indicated below it does not perform any thermal monitoring, moreover the
relays will all be disabled. The fault contact switches and the fault LED flashes.
•
Programming viewing display.
•
PRG programming.
•
Relay test.
The ALARM and TRIP relays only switch when the set temperature thresholds are exceeded.
The FAULT (fault) contact, programmed in active failsafe mode (default YES), opens (11-12) when the appliance is
powered, only if during the access phase the control unit does not detect anomalies, and keeps the switching until when
one of the following events occurs:
•
Data memory fault (Ech message).
•
FO sensor fault (FCC-FOC-FLT)
•
CFO 521 concentrator disconnected (TEC)
•
Insufficient supply voltage.
•
During the power on reset after programming (PRG), displaying of the data (VIS) and relay test.
The FAULT failsafe mode can be disabled FAULT failsafe "NO" see programming step 30-31 page 20.
NOTE: in order to avoid unwanted system outages, do not connect the FAULT relay to the transformer tripping circuit.
FAULT AND RESET MESSAGE SEQUENCE
Find below the sequence of fault messages and RESET function condition.
1) ECH
2) TEC
3) FO FCC
4) FO FOC
5) FO FLT
The FAN1 and FAN2 contacts can be used to control the cooling fans, or they can be inserted in the conditioning system
of the transformer room, see paragraph cooling fan control on page 18.
NOTE: always disconnect the unit before performing any electrical connections.
eeprom fault
concentrator communication bus fault
min. temperature full scale exceeded
max. temperature full scale exceeded
broken or disconnected fibre optic sensor
erasable message
non-resettable condition
non-resettable condition
non-resettable condition
non-resettable condition
POWER SUPPLY
The FO 935 ETH can be supplied by 85 to 260 Vac-Vdc, 50/60 Hz irrespectively of polarity in Vdc (terminals 40 - 42).
This particularity is obtained thanks to the use of a tested power supply, of new conception and realisation,
which frees the installer from any uncertainty regarding the correct Vac or Vdc power supply.
The earthing cable must always be connected to terminal 41.
When the control unit is powered directly by the secondary of the transformer to be protected, it can be burnt out by high
intensity overvoltages.
These problems occur if the main switch is closed and the transformer does not have the load (no load test).
The above is much more evident when the 220 Vac voltage is taken directly from the bars of the secondary
of the transformer and there is a fixed capacitor battery for power factor correction of the transformer itself.
If an existing control unit must be replaced with a new one, to guarantee its correct and safe operation, the
connecting terminals must be replaced with the new terminals supplied.
FAULT CONTACT OPERATION (failsafe active)
FAULT 11-12 NC: ALARM FAULT OR POWER OFF
FAULT 11-12: NO POWER ON OR NO FAULT
To protect the control unit against line overvoltages, the PT-73-220 electronic arrester, designed by TECSYSTEM S.r.l. for
this specific purpose, is recommended. Alternatively, it is advisable to use 110 V AC supply voltages or, even better, 110
VDC.