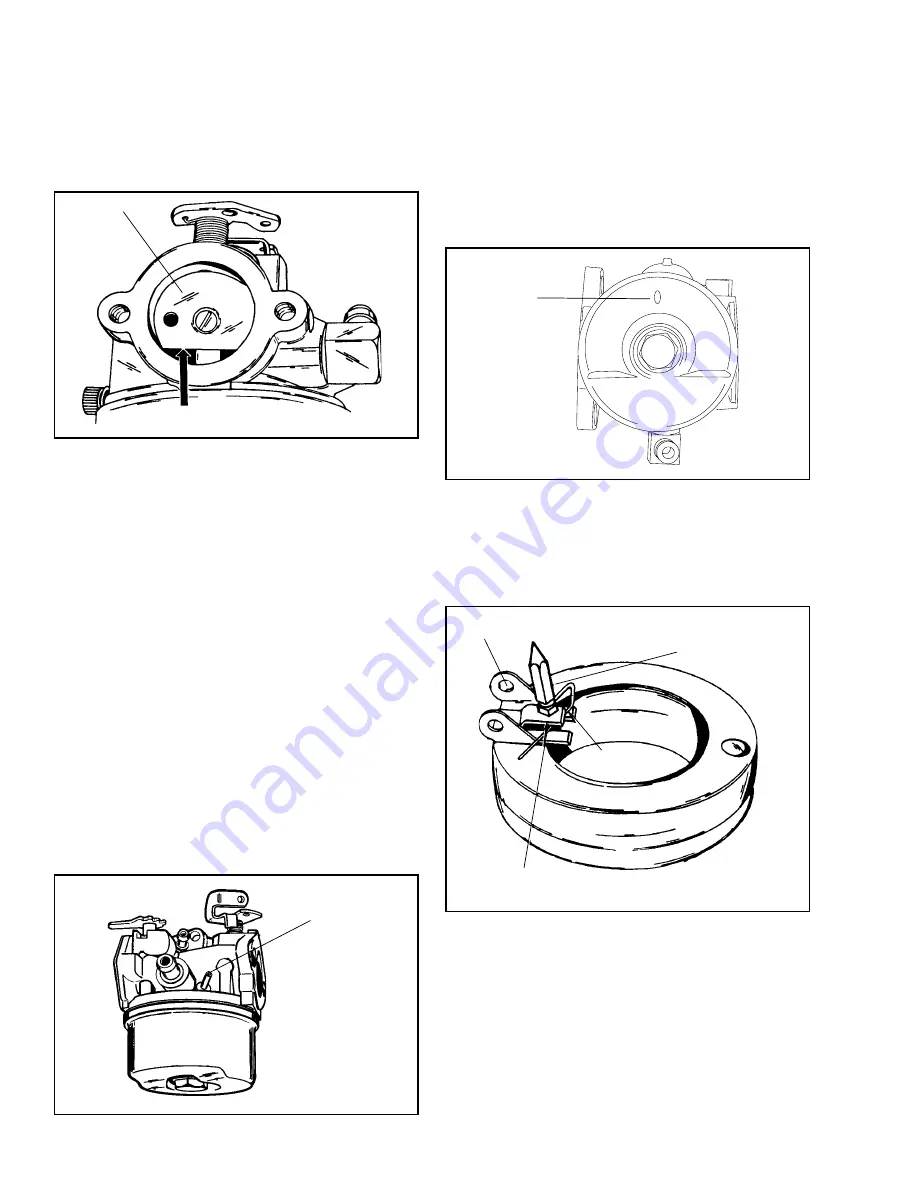
8
CHOKE.
Examine the choke lever and shaft at the
bearing points and holes into which the linkage is
fastened, and replace if worn or damaged. The choke
plate is inserted into the air horn of the carburetor in
such a position, that the flat side of the choke is down.
Before disassembly note the direction of choke plate
movement. Choke plates will operate in either direction.
Make sure it is assembled properly for your engine.
ADJUSTING SCREWS.
Remove the adjusting screws
from the carburetor body and examine the point, replace
the screws if damaged. Tension is maintained on the
screw with a coil spring. Examine and replace the
O ring seal(s) if damaged.
NOTE:
If screws are made of plastic, dip the end of
the screw in oil before installation to prevent damage.
FUEL BOWL RETAINING NUT.
The fuel bowl retaining
nut has a fixed main jet incorporated in the nut. This
small jet must be clean for proper fuel metering. Clean
by using compressed air.
DO NOT USE WIRE OR
HARD OBJECTS FOR CLEANING.
CARBURETOR VENTING.
Float-type carburetors must
have atmospheric air pressure acting against the fuel
in the fuel bowl. These vents can be external, with a
hole drilled through the side of the carburetor casting
or internal where atmospheric air is picked up in the
air horn near the air cleaner. Regardless of the type,
these vents must be clear and free from dirt, paint,
grease, etc.
HIGH TILT FLOAT STYLE
carburetors use an external
main air bleed.
FUEL BOWL.
The fuel bowl must be free of dirt and
corrosion. When disassembling a carburetor for repair,
always replace the fuel bowl O ring. Lubricate the
O ring with a small amount of oil for easier installation.
Install the float bowl by placing the detent portion
opposite of the hinge pin. Make sure the deepest end
of the bowl is opposite of the inlet needle. The bowl
has a small dimple located in the deepest part. The
purpose of this dimple is to minimize the chances of
the float sticking to the bottom of the bowl caused by
stale fuel.
CHOKE PLATE
DOWN TOWARD FUEL BOWL
MAIN AIR BLEED
FLOAT.
Remove the float by pulling out the float hinge
pin. Lift the float away from the carburetor body. This
will also lift the inlet needle out of the seat.
Examine the float for damage. Check the float hinge
bearing surfaces for wear, as well as the tab that contacts
the inlet needle. Replace any damaged or worn parts.
INLET NEEDLE
EXAMINE FLOAT HINGE FOR WEAR
AT BEARING SURFACES
INLET NEEDLE
CLIP
REMOVE FLOAT TO MAKE ADJUSTMENTS.
BEND THIS TAB TO ADJUST
DETENT
Float sticking can occur due to fuel deposits (gum or
varnish). This can be corrected by loosening the carburetor
bowl nut one full turn and rotating the bowl 1/4 turn in
either direction. Return the bowl to it's original position
and retighten the bowl nut.
Summary of Contents for AH520 -
Page 67: ...64...