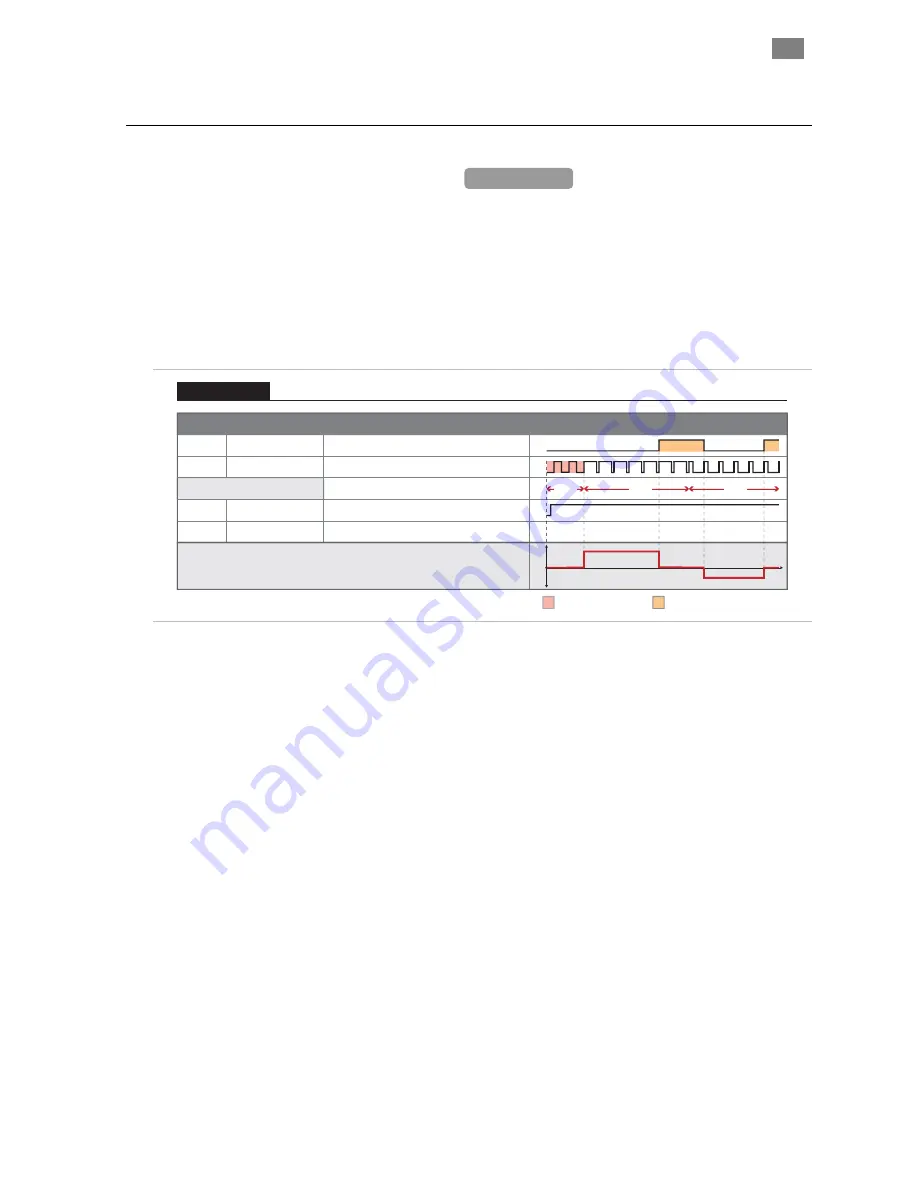
C
L E A R
P
A T H
M C / S D
U
S E R
M
A N U A L
R
E V
.
3 . 0 9
9 1
T
EKNIC
,
I
NC
. T
EL
.
(585)
784-7454
F
OLLOW
D
IGITAL
T
ORQUE
C
OMMAND
(B
I
-P
OLAR
PWM
C
OMMAND
)
M
ODE
D
ESCRIPTION
Connect a digital PWM waveform from your PLC or other device, and
ClearPath will produce torque proportional to the duty cycle of the PWM
waveform.
Assert the Enable Input to energize the motor. Control motor torque by
applying a PWM signal to Input B. Motor torque changes in proportion to
the duty cycle of the applied PWM signal. Assert the Inhibit signal (Input
A) to immediately turn off torque. See figure below and read text for
timing and PWM requirements.
Signal
Function
Input Type
Input A
Motor torque vs. time
Input B
Enable
Inhibit (optional)
Torque/Direction
Enable
NA
NA
Trigger
Logic: High=Inhibit on Low=Inhibit off
Pulse: Variable PWM
Logic: High=Enable Low=Disable
0
1
0
1
t
tq
Example Timing
Notes:
Asserting Inhibit Input causes immediate jump to zero torque. See text for
information on deadband set up and application.
0
1
0
1
Inside deadband
Inhibit on
Duty cycle of applied PWM signal (%)
Follow Digital Torque Command (Bi-Polar PWM Command)
Torque Control
90%
50%
20%
I/O
F
UNCTIONS
Enable Input -
Asserting this input energizes the motor shaft.
Input A -
This input forces the torque to zero regardless of the input
PWM duty cycle.
Input B -
This input is connected to a PWM signal whose duty cycle
represents the desired torque.
Output (HLFB) -
See HLFB section for available modes.
Notes:
•
PWM input frequency range: 20 Hz to 30 kHz.
•
If the PWM signal is off for 50mS (or more) the PWM input is
considered off. This is interpreted by ClearPath as a zero-torque
command.
•
Disable time = 10 mS
•
To command ClearPath to zero torque, assert the Inhibit): Input
(Input A). Deassert Input A to resume normal operation.
or
•
Set a PWM deadband: to help reliably command zero torque.
Refer to text on following pages for details on deadband setup.
MCVC + MCPV
Available on