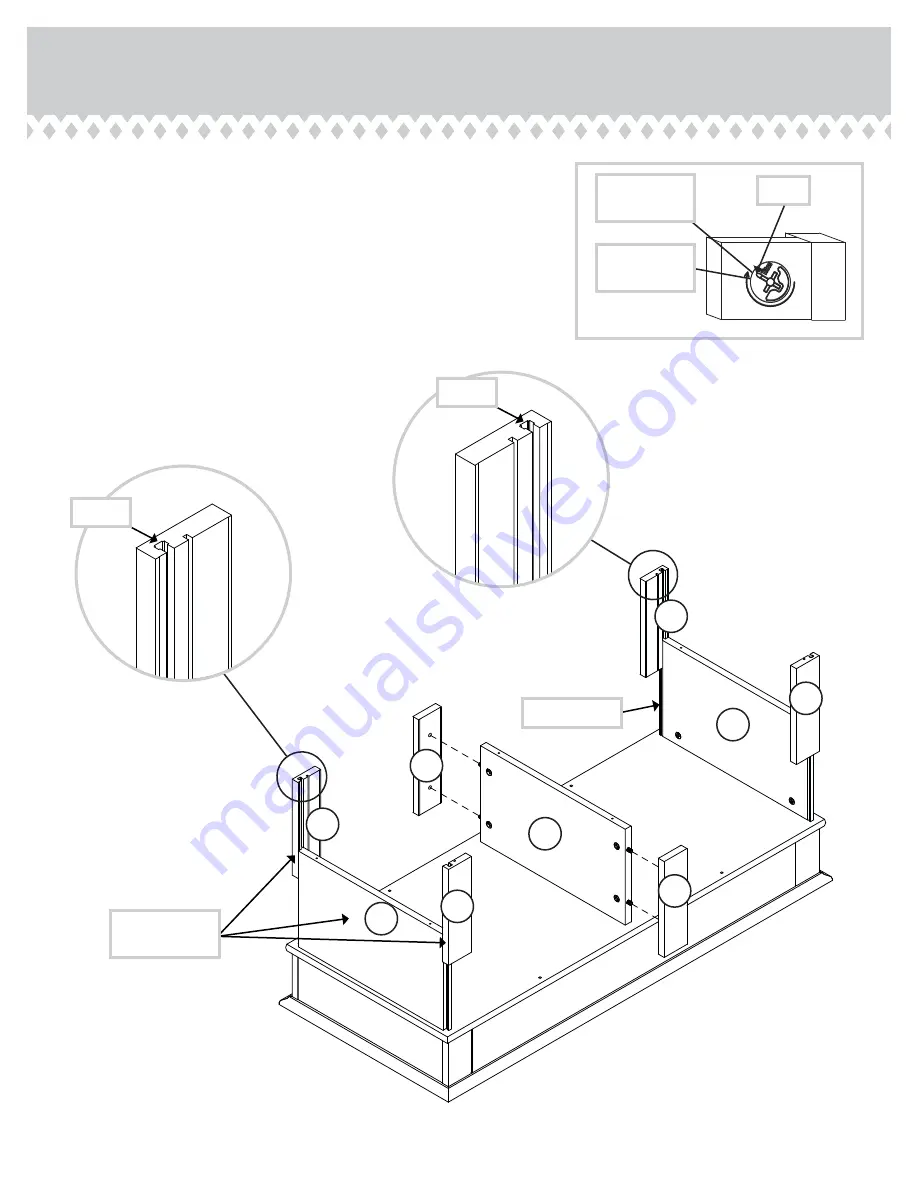
Step
å
Fasten the UPRIGHT MOLDINGS (N) to the UPRIGHT (D).
Tighten four HIDDEN CAMS.
å
Slide the END MOLDINGS* (M) onto the notched edges
of the LOWER ENDS (C).
å
*U.S. Patent No. 5,499,886
Step 9
Page 14
Arrow
Minimum
190 degrees
Maximum
210 degrees
C
C
D
M
N
M
N
M
M
These surfaces
should be even.
Notched edge
Groove
Groove