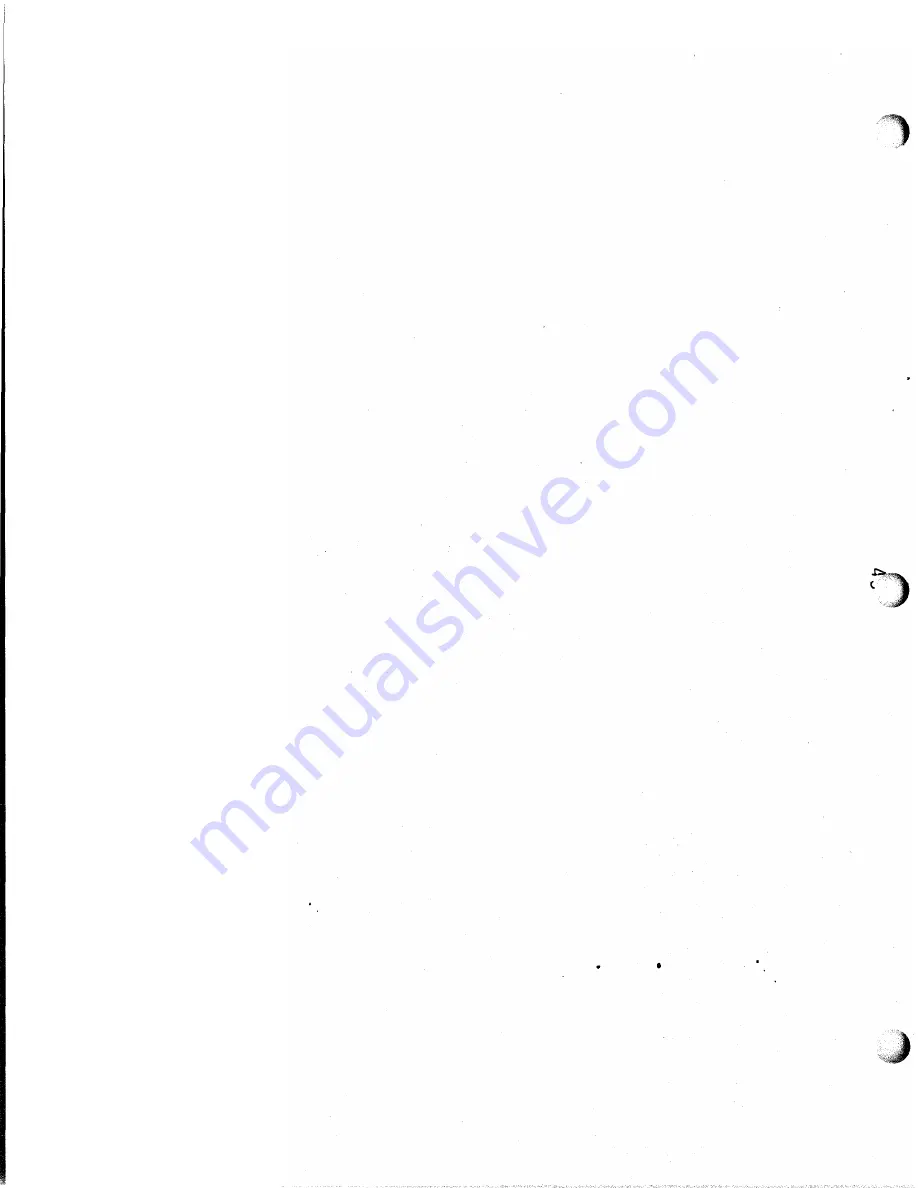
- 8-
(B-138)
the
.040"
c learance, the plq in the ribbon reverse bail s hould be taken up
in
a direction to make the clearance a
maximum.
To adjust, position the ribbon
reverse sha:fts links
by
means of their set screws. At the same time, make·
certain that the ribbon reverse pawl links do not bind at their shoulder screws
and that the right ribbon reverse shaft link clamping screw does not interfere
with the screw which anchors the ribbon feed ratchet friction spring
to
the
carriage casting.
RIBBON SPOOL CUPS
AND
RIBBON aEVERSE
ARK
BACKSTOP ADJUSTMENT*
The centers of the ribbon rollers should be
3/4"
to
7/8"
in
front of
a
line through the centers
ot
the ribbon spool shafts (Figure
9).
With the
ribbon reverse arms held against their backstops (Figure lOB), approximately'
3/4
of the tooth on each ribbon reverse pawl shoUld
be
in a position
to
be
engaged
by
the ribbon reverse bail (Figure
11).
There should be no bind between
the ribbon spool shaft spur gears and the vertical ribbon feed shaft spur gears
at
a.ey
point in their engagement.
To adjust, position the ribbon spool cups
and
ribbon reverse
arm
backstops
by
means of the nuts on the ribbon spool cup
bushings (Figure
8).
When t ightening the nuts, take up the play between the
ribbon spool cup bushings and the ribbon spool brackets in a direction
to
make
the plq between the spur gears a
maximum.
RIBBON REVERSE
ARM YIELD
SPRING TENSION
ADJUS'l'MENT
(Figure lOB)*
Position the ribbon reverse bail
so
that it will block the full
travel of the ribbon reverse arm, and with the ribbon reverse pawl resting
against the ribbon reverse
bail
(Figure
11),
apply the push end of an
8
oz.
scale, held at a right angle to the ribbon reverse arm at the center where the
ribbon is threaded.
It should require
1-1/2
to
4-1/2
ozs. to start the ribbon
reverse arm moving.
To increase or decrease the tension, remove the spring and
adjust
by
bending.
RIBBON
REVERSE
PAWL SPRING TENSION (Figure
11)
See Note
(A)
With the ribbon feed shaft in its lef't position
and
the pull bar bail
in its extreme forward posi. tion, hold the carriage
so
th at the ribbon spool cups
are lowermost.
Then hook an
8
oz. scale in the notch of the left reverse pawl
and pull horizontally toward the rear of t he carriage. It should require l
to
2
ozs.
to
start the pawl
mving.
Move the ribbon feed shaft to its right posi
ti
on and,
in the same
mann
er, check the tension of the right ribbon reverse
pawl spring.
'
RIBBON
REVl!RSE
BAIL SPRING COMPRESSION (Figure
11)
See Note (A)
With the type bar carriage held so that the ribbon spoo_ cups are
lowermst, and the pull bar bail plunger is
in
its extreme forward position,
*
*
*
(A)
These requirements should be cheeked with the type bar carriage
removed.
*
This adjustment applies only
to
units equipped with a ribbon reverse
yield mechanism.
(j')
-J
N
�
�
�