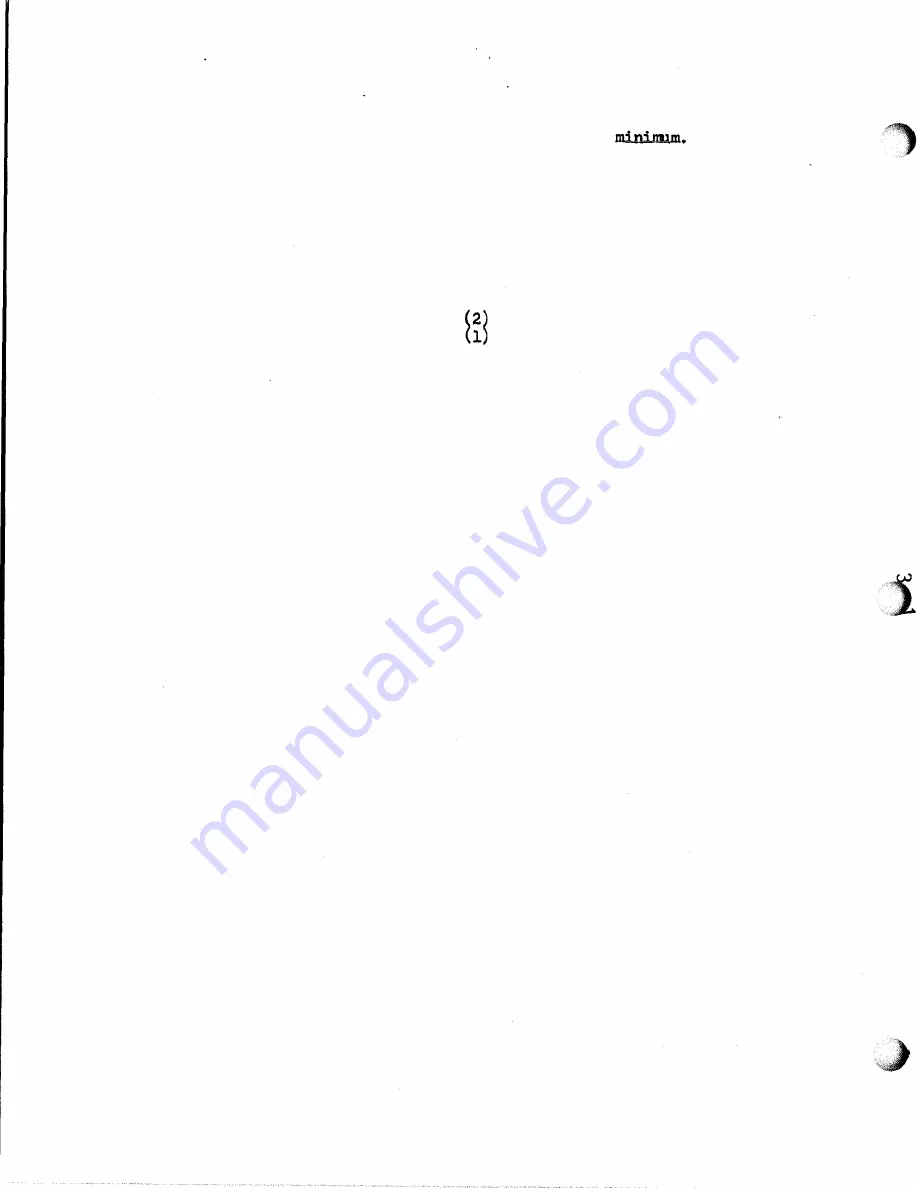
-44-
(B-138)
motor and carefully readjust the vertical position of the mtor pinion
by'
means
of the adjusting screw until the gear noise is reduced to a
Tighten
the three motor plate mounting screws
am
the adjusting screw lock nut.
Recheck
the backlash between the gears.
CAUTION: Care should be exercised in adjusting the vertical position of the
motor pinion while the .mtor is running in order
to
avoid damaging
the
main
shaft gear or reducing the speed of the mtor as the result
of too close a mesh between the gear alli the pinion.
NOTE: When printers are equipped with mtors having elongated mounting
holes: Make adjustments (l)
and
as described in the foregoing,
except that
in
making adjustment
the motor must be shifted until
the center line of the gear also passes through the center of the
hole in the motor pinion as nearly as it is possible
to
determine
b,y
f!P,{e.
SEND-�EIVE RESET LEVER
UPPER
ADJUSTING SCRE« ADJUSTMENT
(Figure 65B)**
There should be
.004"
to .006" clearance between the upper edge of
the intermediate lever toe
and
the bottom of the blank function lever extension
under the following condi tiona}
With the printing bail in its extreme rear position
and
the send
receive lever
in
the
SEND
position (up), move the toe of the intermediate lever
under the blank run::tion lever extension. Then select the T combination
and
rotate the motor un til the intermediate lever is rooved to a position where the
blank
function lever extension overlaps the toe of the intermediate lever
b;y
one half the thickness of the blank function lever exten sion
and
check for the
required clearance. Adjust
b,y
setting the height of the reset lever upper
adjusting screw.
RESET LEVER LOVIER
ADJUSTING
SCREW
ADJUSTMENT
(Figure 66A.) (*) (**)
With the platen
in
the
UNSHIFT
position {down), the motor stop
combination selected and the motor rotated until the printing bail is in its
extreme forward position, there should be
some
clearance, not roo re then
.002",
between the head of the lower adjusting screw and the lower surface of the
front
extension of the motor stop function lever when the send-receive lever
is in the
SEND
position
(up)
•
.
Adjust the height of the lower adjusting screw
to regulate this clearance.
RESET LEVER
DOWN STOP SCREW ADJUSTkENT
(Figure 66A ani B)*
With the send-receive handle in the
SEND
position (up)
am
the toe ot
t he intermediate lever under the blank function lever extension, select the
BLANK combination and rotate the main shaft until the function bail roller just
leaves
the cam surface of the
blank
function lever. Then depress the break ke7
*
*
*
*
Omit when typing unit is not equipped with mechanical motor stop
mechanism..
**
Omit when unit is not equipped
with
SEnd-receive
.11'18Chaniam.
en
-J
N
�
o::J
0