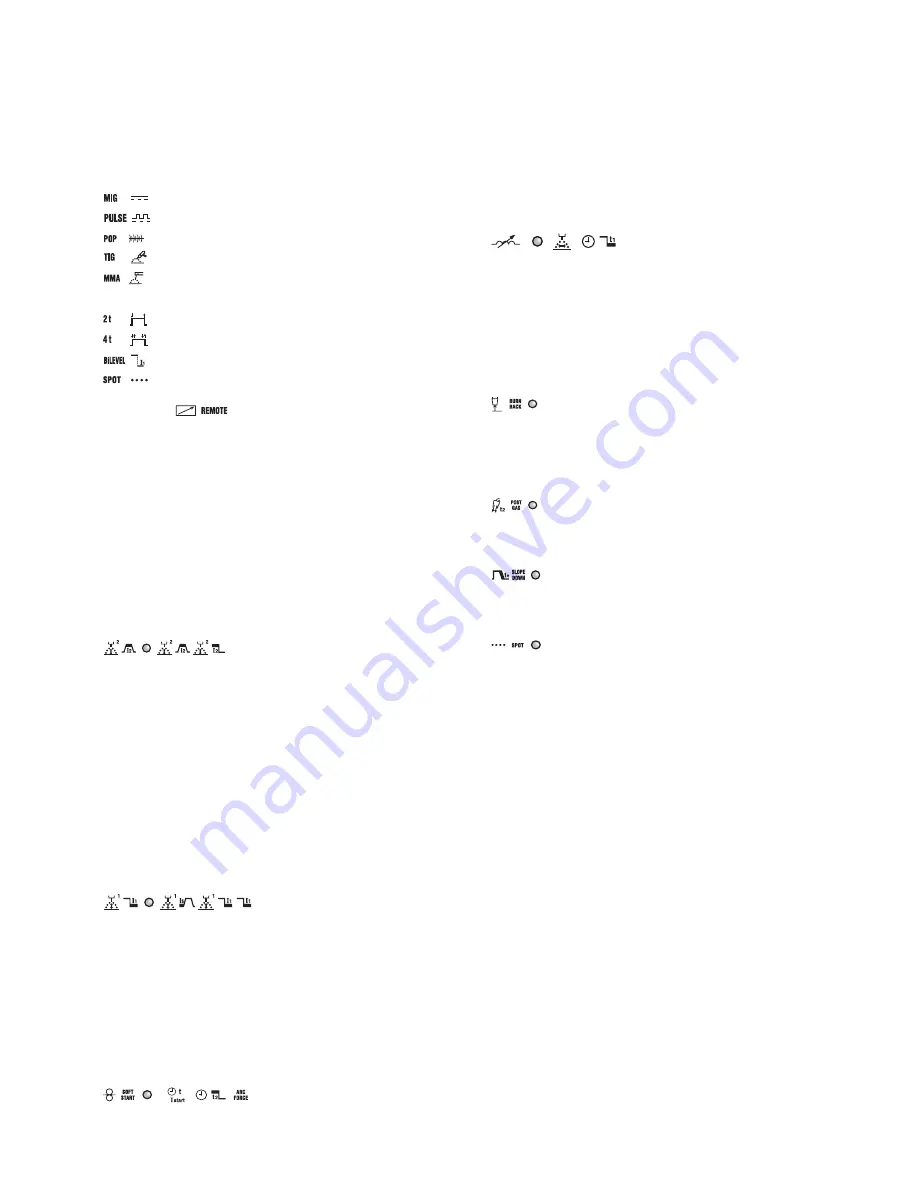
- 7 -
show for a few seconds..
2- LED indicating that the TORCH OR ELECTRODE IS POWERED.
3- LED indicating WELDING MACHINE PROGRAMMING.
4 - RECALL key for downloading customised welding programmes (see
section 4.3.2.4).
5- SAVE key for saving customised welding programmes (see section 4.3.2.3).
6- Welding programme selection key and 2-digit display.
As the key is pressed repeatedly, the display will show the numbers from “0” to
“54”. Each number between “1” and “54” is associated with a synergic welding
programme
(see TAB. 3)
while “0” is associated with manual welding machine
operation, where the operator is able to insert settings for all the parameters
(only for MIG-MAG SHORT and SPRAY ARC).
7- Key for selecting welding procedure.
When this key is pressed the LED corresponding to the intended welding mode
will light up:
: MIG-MAG with “SHORT/SPRAY ARC” mode.
: MIG-MAG with “PULSE ARC” mode.
: MIG-MAG with “PULSE ON PULSE” mode.
: TIG.
: MMA electrode.
8- Key for selecting MIG-MAG torch button control mode.
When this key is pressed the LED will light up corresponding to:
: 2- stroke operation, ON-OFF with button pressed.
: 4- stroke operation, ON-OFF with button released.
: bi-level operation for MIG-MAG, TIG.
: MIG-MAG SPOT welding.
9- Key for switching on remote control.
When the LED
is lit, adjustments can only be made by remote
control, i.e.:
a) single potentiometer control (only MMA and TIG):
replaces the function of
the encoder knob
(14).
b) control by two potentiometers:
replaces the function of encoder knobs
(14)
and
(13)
.
c) pedal control (only MMA and TIG):
replaces the function of the encoder
knob
(14)
.
NOTE: It is only possible to select REMOTE if a remote control is actually
connected to the corresponding socket.
10- Key for selecting welding parameters.
Pressing the key repeatedly will light up one of the LED’s from (10a) to (10h),
each associated with a specific parameter. The setting for each activated
parameter is made using the knob (13) and is shown on the display (15). While
making these settings knob (14) adjusts the value of the main welding level
shown on the display (16), either current or wire feed rate (see description at
point (14)), except for LED (10b).
Knob (14) can only be used to adjust the secondary level when LED (10b) is ON
(see description of LED (10b)).
Note: Parameters that cannot be modified by the operator, depending on whether
you are working with a synergic programme or in manual mode (“PRG” 0) are
automatically excluded so that they cannot be selected; the corresponding LED
will not light up.
10a-
• MIG-MAG
This parameter is displayed automatically during MIG-MAG welding operations,
and shows the actual arc voltage (LED (15a) is ON).
• MIG-MAG Pulse Arc
When setting a MIG-MAG Pulse Arc synergic programme this parameter is
used to set the correction to be made to the arc length as calculated in synergy
(range from -5% to +5%) (LED (15c) ON).
In the same mode, setting bi-level, pulse on pulse or Tstart mode will cause the
parameter to take the value of arc length correction at the main welding level
as calculated in synergy as above (range from -5% to +5%) (LED (15c) ON).
• MIG-MAG Short Arc
When setting a MIG-MAG Short Arc synergic programme this parameter is
used to set the correction to be made to the arc length as calculated in synergy
(range from -5% to +5%) (LED (15c) ON).
In the same mode, setting bi-level mode will cause the parameter to take the
value of arc length correction at the main welding level as calculated in synergy
as above (range from -5% to +5%) (LED (15c) ON).
• MIG-MAG Short Arc “PRG 0”
Also in MIG-MAG Short Arc mode, manual programming (“PRG 0”), this
parameter used to set the actual arc voltage (range 10-40) (LED (15a) ON).
In the same mode, setting bi-level mode will cause the parameter to take the
value of actual arc length at the main welding level as calculated in synergy as
above (range 10-40) (LED15a ON).
10b-
• MIG-MAG Pulse Arc
In MIG-MAG pulse arc mode, setting bi-level, pulse on pulse or Tstart mode will
enable adjustment of currents I
1
and I
s
(I
start
) (using knob (14)) and correction of
arc length (using knob (13)) for the secondary welding level, as calculated in
synergy (range from -5% to +5%)(LED (15c) ON).).
• MIG-MAG Short Arc
For synergic MIG-MAG short arc programmes, setting bi-level mode will make
it possible to adjust the current/wire feed rate (using knob (14)) and to correct
arc length (using knob (13)) for the secondary welding level as calculated in
synergy (range from -5% to +5%) (LED (15c) ON).
• Bi-level “PRG 0”
When manual programming “PRG 0” is selected with bi-level mode, this
parameter is used to adjust wire feed rate (using knob (14), (LED 16c) ON) and
actual arc voltage (using knob (13)) for the secondary welding level I
1
(range
10-40) ((LED (15a) ON)
.
In TIG bi-level mode this parameter is used to adjust the welding current
second level (I
1
).
10c-
• MIG-MAG “PRG 0”
In manual mode,“PRG 0”, this parameter is used to adjust wire feed rate as
welding starts, in order to optimise arc strike (adjustment 1-100% and LED
(15c) ON).
• MIG-MAG Pulse Arc 2-STROKE
In MIG-MAG Pulse Arc 2-STROKE mode this parameter is used to adjust the
length of start current time (T
start
). If the parameter is set to zero, the function
is disabled, while with any setting greater than zero (adjustment range 0.1-
3 seconds) it is possible to select LED (10b) in order to set the arc voltage
correction and the start current value (secondary level). The start current
can be set at a higher or lower value than the main welding value; a higher
start current is very useful, especially when welding aluminium and its alloys,
making it possible to heat the piece more quickly (“Hot start”).
• MIG-MAG Pulse on Pulse
In MIG-MAG Pulse on Pulse mode the parameter can be used to adjust the
length of main welding current time (adjustment range 0.1-10 seconds and
LED (15b) ON).
• MMA
With MMA electrode operation, the parameter takes the value of “Arc force”,
so that it is possible to make the setting for dynamic overcurrent (adjustment
range 0-100% and LED (15c) ON). Duing MMA welding, the display (15) will
show the actual arc voltage (LED (15a) ON), and LED (10c) still remains on so
that Arc force can also be adjusted during welding.
10d-
• MIG-MAG Pulse Arc
In MIG-MAG pulse arc mode the parameter determines arc pinch-off. The
higher the value the more concentrated will be the arc during welding. In a
welding mode using two current levels (bi-level, pulse on pulse or Tstart) arc
pinch-off has the same setting for both levels (+1% / -1%).
• MIG-MAG “PRG 0”
In MIG-MAG “PRG 0” manual mode the parameter is used to adjust electronic
reactance (adjustment range 20-80% and LED (15c) ON). The higher the
value, the hotter will be the weld pool. In bi-level mode electronic reactance
has the same setting for both levels.
• MIG-MAG Pulse on Pulse
In MIG-MAG Pulse on Pulse mode the parameter can be used to adjust the
length of secondary welding current time (adjustment range 0.1-10 seconds
and LED (15b) ON).
10e-
Wire BURN-BACK time when welding stops.
This parameter is used to adjust wire burn-back time at the end of welding. An
appropriate setting will prevent the wire from sticking to the piece in manual
mode (PRG 0) - MIG-MAG SHORT ARC (adjustment range 0.01-1 seconds and
LED (15b) ON).
When setting a MIG-MAG synergic programme this parameter is used to set the
correction to be made to BURN_BACK TIME as calculated in synergy (range
from -1% to +1%, LED (15c) ON).
10f-
POST-GAS MIG-MAG SHORT ARC and TIG.
In any MIG-MAG SHORT ARC and TIG mode this parameter corresponds to
“Post-gas” time, so that it is possible to adjust the time for which protective gas
will flow after welding stops (adjustment range 0.1-10 seconds and LED (15b)
(ON).
10g-
Welding current SLOPE DOWN.
This is enabled only and exclusively when using MIG-MAG PULSE ARC or
SHORT ARC synergic programmes (“PRG” from “1” to “54”) or TIG welding.
It is used to reduce the current gradually when the torch button is released
(adjustment range 0-3 seconds and LED (15b) ON).
10h-
SPOT WELDING TIME.
This is enabled only and exclusively if “SPOT” mode has been selected with key
(8). It is used for MIG-MAG spot welding with welding time control (adjustment
range 0.1-10 seconds and LED (15b) ON).
11- Key for manual activation of gas solenoid valve.
This button causes gas outflow (piping discharge – flow rate adjustment) without
having to operate the torch button; the action of the button is momentary.
12- Key for manual wire feed.
This button is used to feed the wire along the torch hose without having to
operate the torch button; the action is momentary and feed rate is fixed.
13- Encoder knob for adjusting welding parameters (see 10a-10h).
14- Encoder knob.
The knob adjusts:
- Welding current (LED (16a) ON).
- Wire feed rate (LED (16c) ON) in Short/Spray arc mode.
- The thickness of the piece being welded (LED (16b) on) if selected with key
(17), piece thickness in mm.
In a welding mode using two current levels (bi-level, pulse on pulse or Tstart),
with LED (10b) ON the knob adjusts:
- Welding current I
1
(LED (16a) ON) for the secondary level in Pulse arc mode.
- Wire feed rate for the secondary welding level (LED (16c) ON) in Short/Spray
arc mode.
15- 3-digit alphanumeric display. This shows:
- welding parameter values (see from (10a) to (10h)) in no-load operation.
- the actual arc voltage during welding.
NOTE: when welding stops, the display automatically switches to the setting
value.
- an alarm indicator (see point 1).
15a, 15b, 15c- LED’s indicating current unit of measurement (volts, seconds,
percentage).
16- 3-digit alphanumeric display.
This shows:
- the value of the setting made using the encoder knob (14).
- the actual current during welding.
NOTE: when welding stops, the display automatically switches to the setting
value.
- an alarm indicator (see point 1).
16a, 16b, 16c- LED’s indicating current unit of measurement (current in amps
(A), thickness in millimetres (mm) and wire feed rate metres/minute (m/
min)).
17- Key for selecting unit of measurement – Amps, mm, mm/min (LED’s (16a)
(16b) (16c)).
Used to set weld material thickness, welding current and wire feed rate
respectively, using the encoder (14).
“PRG 0” manual selection: the setting for each individual parameter is
independent of the settings for the other parameters.
Programmes from “1” to “54”: the setting for each individual parameter (e.g.
material thickness) automatically defines the values of the other parameters (e.g.
welding current and wire feed rate).