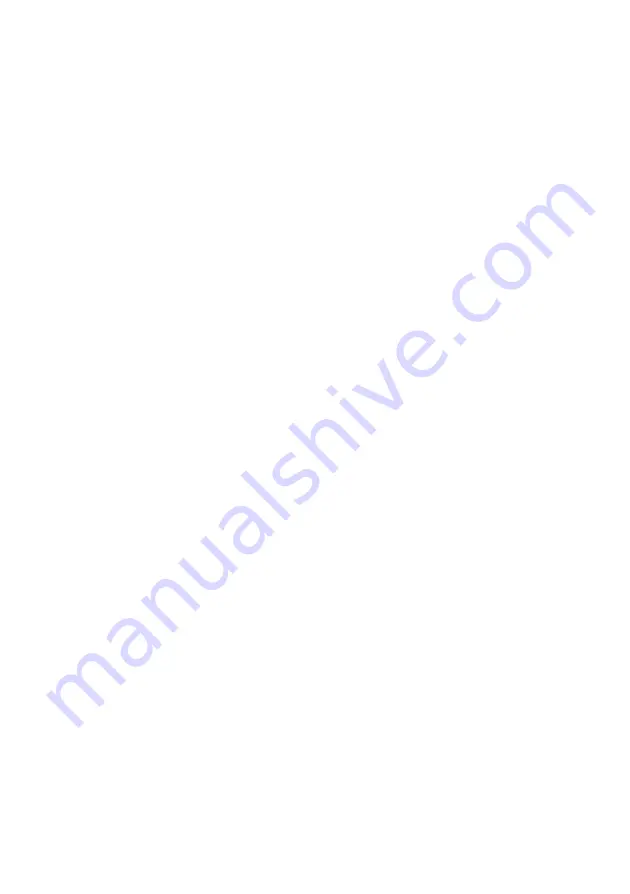
permitted limits.
frequency and voltage
CUTTING
Cutting mode:
WITH THE TORCH it is necessary to work with the
NOZZLE IN CONTACT
WARNING!
-Making an unprepared contact cut will cause rapid wear of
the torch nozzle. Bring the torch nozzle near the edge of the
workpiece (= 3 mm.), press the torch button; after approx.
0.5 seconds (pre-air) the pilot arc is struck (max duration 2
seconds). If the distance is correct, the pilot arc immediately
transfers to the workpiece causing the cutting arc to be
struck.
Move the torch on the surface of the workpiece making
steady progress along the ideal cutting line. Adjust the
cutting speed according to the thickness and the selected
current, and check that the arc coming out of the lower
surface of the workpiece has an inclination of 5-10° to the
vertical in the opposite direction to the cutting direction.
moving forward, arc tilting
- An excessive distance torch-piece or the absence of
material (end cut) causes the immediate interruption of
7. AIR PRESSURE FAULT (YELLOW SIGNAL LED AND
the arc.
RED SIGNAL LED - GENERAL ALARM“ON”
- Interruption of arc (cutting or pilot) is obtained by releasing
AT THE SAME TIME ) (Fig.C-7)
torch button.
- When lit it indicates that air pressure is not enough for
- Piercing: If you have to make this operation or if you have
proper functioning.
to start from the center of the piece, ignite keeping the
- During this phase, the functioning of the machine is
torch tilted and bring it to an upright position with a smooth
inhibited.
movement.
- Restoration is automatic (the led turn off) after pressure
- This procedure avoids that returns of arc or melted parts
has lowered within required limits.
spoil the hole of the nozzle reducing its functionality.
8 TECHNICAL DATA TABLE (Fig.I)
a
Cutting circuit data
Figure (F) the drawing shows the starting with
-No-Load voltage (U
0
).
tilted torch
-Cutting voltage and current (l
2
/ U
2
)
Piercing of parts with a thickness of
25 % of max. usuable
-Use intermittence ratio (X)
foreseen, may be carried out directly.
b
Mains Data
For peculiar uses (ex. cutting of pierced sheets or cutting
-Phase number,
with mechanized torch ) contact our AFTER- SALE
-Case protection degree
service and you will receive detailed instructions.
-Absorbed current (l
1
)
-Delayed fuses to be used.
COMMONEST CUTTING FAULTS
During cutting operations performance faults may arise
TORCH
which are not caused by plant malfunctioning but by other
- The torch button is the only control device which can start
operational faults such as:
and stop cutting operations.
a
Insufficient penetration or excessive scoria settlement:
- When button is released the cycle is immediately and
-too high cutting speed,
always stopped with the exception of cooling air (post-air).
-torch is too tilted,
- Accidental manoeuvres
: in order to start cycle button
-piece is too thick,
must be pushed at least 500 ms.
-electrode and nozzle are worn out.
b
Interruption of cutting arc:
5. CUTTING OPERATIONS
-cutting speed too low.
-excessive distance between torch and piece,
PRELIMINARIES.
-electrode is worn out,
Check and follow instructions as foreseen in the
- intervention of the protections
paragraphs
1 SAFETY and 2 INSTALLATION of the
C
Tilted cutting (not perpendicular)
present instruction manual.
-torch position not correct
- Close (bring to position
I
) automatic mains switch and
-asymmetric wear of nozzle hole and/or wrong
general machine switch in sequence.
assemblage of torch parts.
- Choose, by turning the cutting current potentiometer, the
d
Excessive wear of nozzle and electrode:
most suitable position to the work to be performed.
-air pressure too low,
- Push and release torch button causing air outflow (
³
30s
-contaminated air (humidity-oil),
post air).
(Fig.C-8)
.
-nozzle holder damaged,
- During this phase, set air pressure till gauge indicates
-excessive pilot arc ignitions in the air.
value in “bar” requested according to the torch in use (see
TECHNICAL DATA).
- Let air outflow terminate spontaneously to facilitate
6. MAINTENANCE
removal of condense which settled on the torch.
WARNING !
NEVER ACCESS INSIDE THE MACHINE (PANEL
REMOVAL) OR TOUCH THE TORCH (DISASSEMBLAGE)
WITHOUT HAVING DISCONNECTED POWER PLUG.
ANY INSPECTION PERFORMED UNDER VOLTAGE
INSIDE THE MACHINE OR INSIDE THE TORCH MAY
CAUSE SEVERE ELECTRIC SHOCKS CAUSED BY
DIRECT CONTACT WITH PARTS UNDER VOLTAGE:
TORCH
Periodically, according to its use or to cutting faults (see
Paragraph 5) verify wear of the par ts connected to plasma
arc:
1. NOZZLE HOLDER.
Unscrew manually from head of the torch. Clean throughly
and replace if damaged (burns, distortions or cracks). Verify
integrity of superior metal sector (actuator torch safety).
2. NOZZLE.
Check wear of plasma arc hole and of inner and outer
Figure (E) the drawing shows torch position on part
surfaces.
(U )
1
- 12 -
Summary of Contents for PLASMA 30
Page 52: ...FIG A FIG B 52 ...