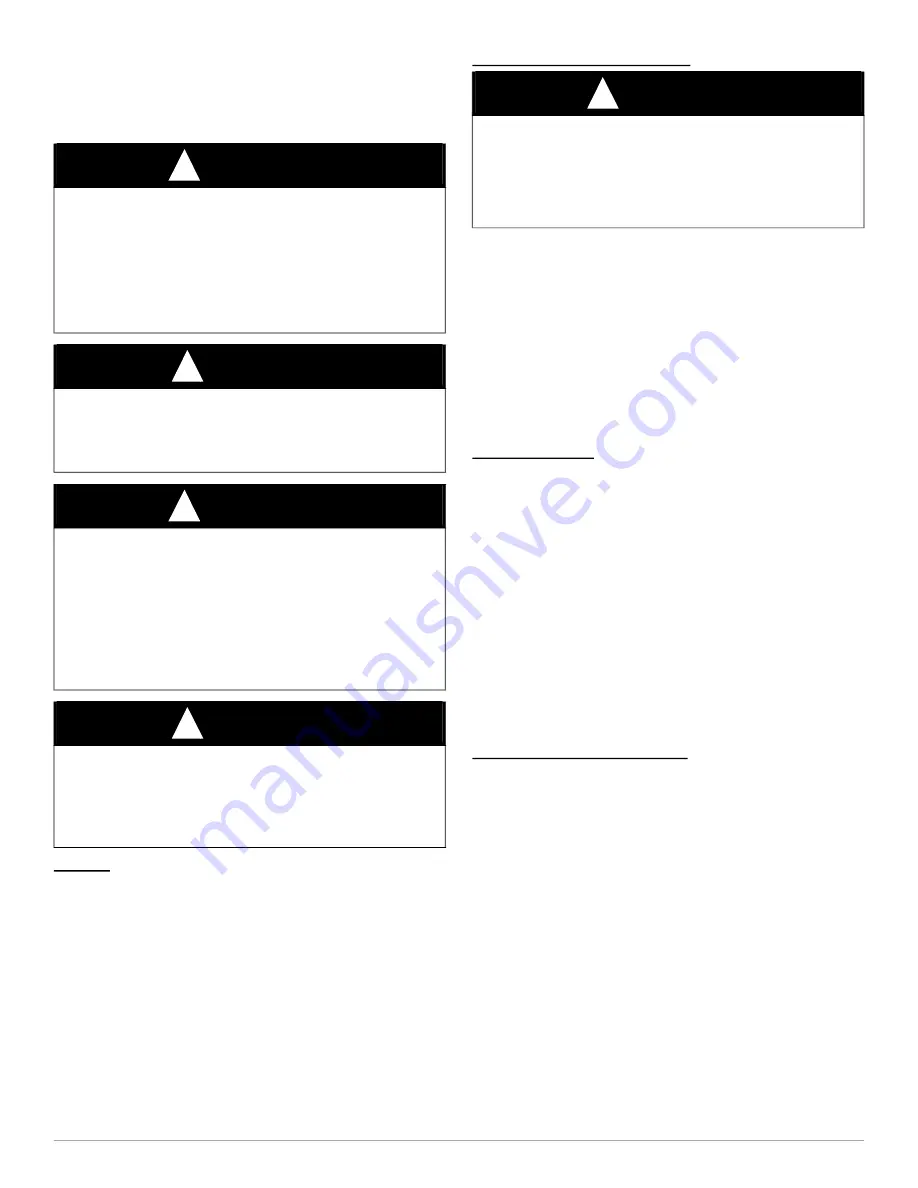
F97CMN and G97CMN: Installation, Start-up, Operating and Service and Maintenance Instructions
Manufacturer reserves the right to change, at any time, specifications and designs without notice and without obligations.
58
SERVICE AND MAINTENANCE PROCEDURES
Untrained personnel can perform basic maintenance functions such as
cleaning and replacing air filters. All other operations must be performed
by trained service personnel. A qualified service person should inspect
the furnace once a year.
General
These instructions are written as if the furnace is installed in an upflow
application. An upflow furnace application is where the blower is
located below the combustion and controls section of the furnace, and
conditioned air is discharged upward. Since this furnace can be installed
in any of the 4 positions shown in
, you must revise your
orientation to component location accordingly.
Electrical Controls and Wiring
The electrical ground and polarity for 115-v wiring must be properly
maintained. Refer to
for field wiring information and to
for furnace wiring information.
NOTE:
If the polarity is not correct, the STATUS LED on the control
will flash code 10 and prevent the furnace from heating. The control
system also requires an earth ground for proper operation of the control
and flame-sensing electrode.
The 24-v circuit contains an automotive-type, 3-amp. fuse located on the
control, see
. Any shorts of the 24-v wiring during installation,
service, or maintenance will cause this fuse to blow. If fuse replacement
is required, use ONLY a 3-amp. fuse. The control LED will be off when
fuse needs to be replaced.
Troubleshooting
Refer to the service label, see
The Troubleshooting Guide can be a useful tool in isolating furnace
operation problems. Beginning with the word “Start,” answer each
question and follow the appropriate arrow to the next item, see
.
The Guide will help to identify the problem or failed component. After
replacing any component, verify correct operation sequence.
Proper instrumentation is required to service electrical controls. The
control in this furnace is equipped with a Status Code LED
(Light-Emitting Diode) to aid in installation, servicing, and
troubleshooting. Status codes can be viewed at the indicator in blower
door. The amber furnace control LED is either
.
heartbeat, off or a code
composed of 1 or 2 digits. The first digit is the number of short flashes,
the second digit is the number of long flashes.
For an explanation of status codes, refer to service label located on
control door or
, and the troubleshooting guide which can be
obtained from your distributor.
Retrieving Stored Fault Codes
The stored status codes will NOT be erased from the control memory,
when 115- or 24-v power is interrupted. The control will store up to the
last 7 Status Codes in order of occurrence.
1. To retrieve status codes, proceed with the following:
NOTE:
NO thermostat signal may be present at control, and all
blower-OFF delays must be completed.
a. Leave 115-v power to furnace turned on.
b. Look into blower door indicator for current LED status.
c. Remove blower door.
NOTE:
The Status Codes cannot be retrieved by disconnecting the limit
switch. To retrieve Status Codes, follow the procedure below.
2. Turn Setup Switch, SW1-1 “ON.”
3. Manually close blower door switch.
4. Control will flash up to 7 Status Codes.
5. The last Status Code, or 8th Code, will be a heartbeat.
6. Turn SW1-1 “OFF.”
7. A continuously-lit Amber LED will appear and indicates proper
operation.
8. Release blower door switch, install blower door and refer to the
SERVICE label on the control door for more information.
WARNING
!
FIRE, INJURY OR DEATH HAZARD
Failure to follow this warning could result in personal injury, death
and/or property damage.
The ability to properly perform maintenance on this equipment requires
certain knowledge, mechanical skills, tools, and equipment. If you do
not possess these, do not attempt to perform any service and
maintenance on this equipment other than those procedures
recommended in the Owner’s Manual.
CAUTION
!
ENVIRONMENTAL HAZARD
Failure to follow this caution may result in environmental pollution.
Remove and recycle all components or materials (i.e. oil, refrigerant,
control board, etc.) before unit final disposal.
WARNING
!
ELECTRICAL SHOCK, FIRE OR EXPLOSION HAZARD
Failure to follow this warning could result in personal injury or death,
or property damage.
Before installing, modifying, or servicing system, main electrical
disconnect switch must be in the OFF position and install a lockout tag.
There may be more than one disconnect switch. Lock out and tag
switch with a suitable warning label. Verify proper operation after
servicing. Always reinstall access doors after completing service and
maintenance.
CAUTION
!
ELECTRICAL OPERATION HAZARD
Failure to follow this caution may result in improper furnace operation
or failure of furnace.
Label all wires prior to disconnection when servicing controls. Wiring
errors can cause improper and dangerous operation.
WARNING
!
ELECTRICAL SHOCK HAZARD
Failure to follow this warning could result in personal injury or death.
There may be more than one electrical supply to the furnace. Check
accessories and cooling unit for additional electrical supplies that must
be shut off during furnace servicing. Lock out and tag switch with a
suitable warning label.