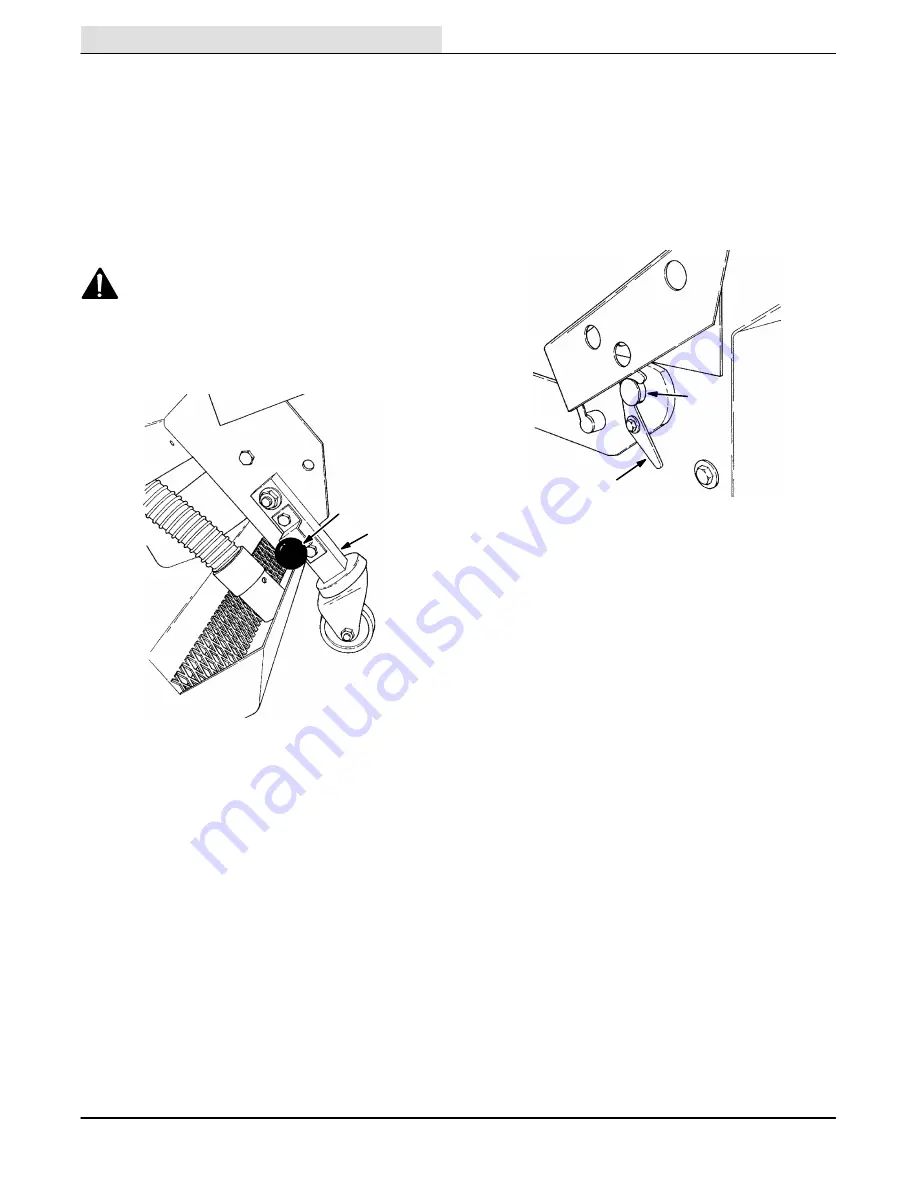
OPERATION
242E MM243 (5---92)
2-26
5. Pull the retaining pin keeper out and remove
the two squeegee assembly retaining pins.
Release the pin keeper.
6. Slide the squeegee assembly out from the
machine.
7. Start the machine, raise the scrub attachment,
and engage the hopper support bar. Turn off
the machine.
WARNING: Raised Hopper May Fall.
Engage Hopper Support Bar.
8. Pull out locking knobs on the two (2) rear
support legs, swing the legs down into the
“down” position, and release the knobs.
A
B
02754
SCRUB ATTACHMENT LEG
A. Locking Knob
B. Leg
9. Loosen the scrub locking cam on the right lift
arm, and rotate it away from the bracket on the
scrub attachment, to free the scrub attachment.
Tighten the cam bolt.
10. Start the machine, raise the scrub attachment,
place the hopper support bar in its storage
location, and lower the scrub attachment. Turn
off the machine.
11. Raise the front bumper.
12. Start the machine, raise the scrub attachment
slightly.
13. Pull out locking knobs on the two (2) front
support legs, swing the legs down into the
“down” position, and release the knobs.
14. Lower the scrub attachment to the floor. Turn
off the machine.
15. Tilt the lift arm hooks back away from the lift
arm pins.
A
B
02752
LIFT ARM HOOK
A. Pin
B. Hook
16. Push the lift arms down to clear the lift arm
pins.
17. Disconnect the electric cable and the single
wire between the scrub attachment and the
machine.
18. Roll the scrub attachment out of the machine to
its storage location.
19. Replace the side scrub brush with a sweeping
variety side brush as described in
TO REPLACE
SIDE BRUSH
.
20. Replace the main brush with a sweeping variety
main brush as described in
TO REPLACE MAIN
BRUSH
.
21. Install the hopper as described in
TO INSTALL
THE HOPPER WITH DOLLY
.
Summary of Contents for 242E
Page 1: ......
Page 10: ...SPECIFICATIONS 242E MM243 9 89 1 2 ...
Page 14: ...SPECIFICATIONS 242E MM243 9 89 1 6 ...
Page 16: ...OPERATION 242E MM243 5 92 2 2 ...
Page 62: ...MAINTENANCE 242E MM243 5 92 3 22 05805 ELECTRIC SCHEMATIC ...
Page 88: ...MAINTENANCE 242E MM243 5 92 3 48 ...
Page 90: ...APPENDIX 242E MM243 9 89 4 2 ...