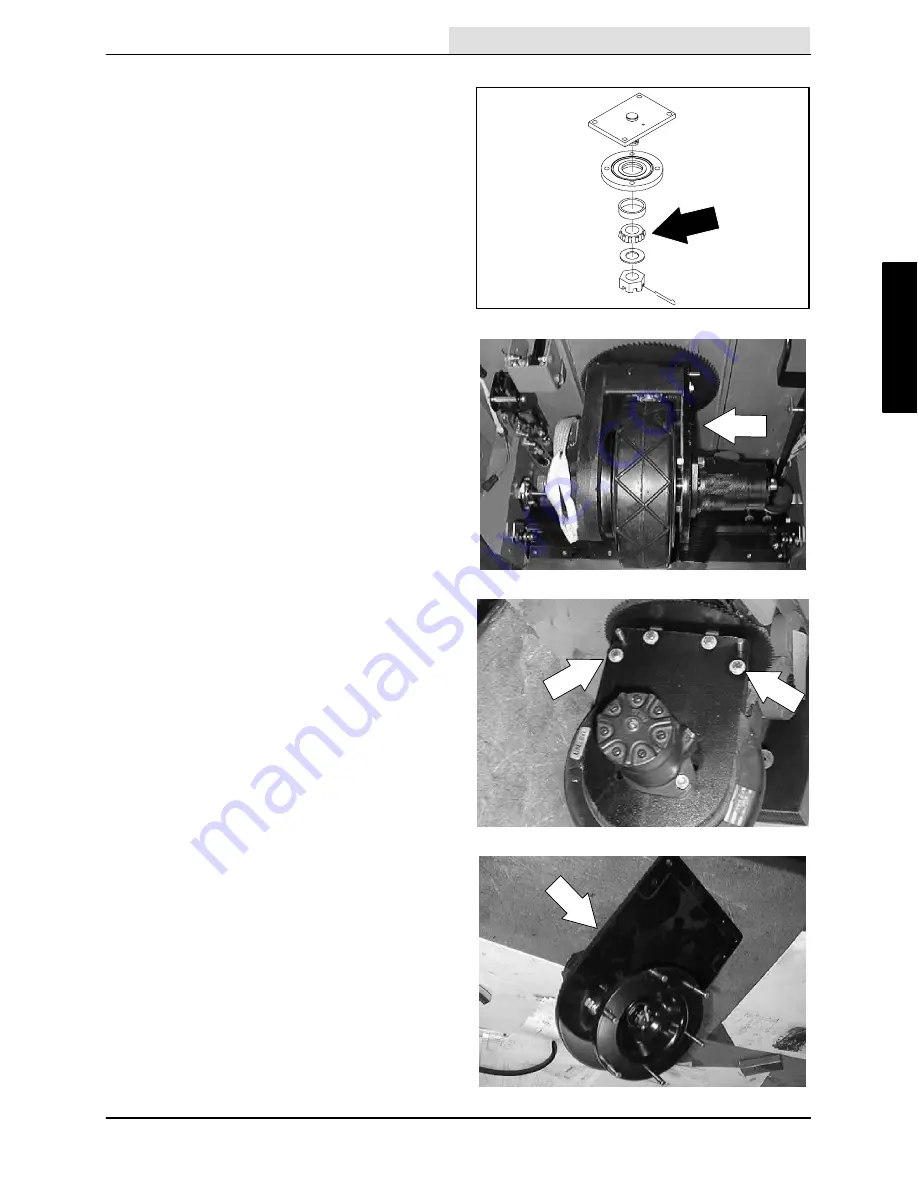
CHASSIS
2-27
6200D 330395 (8--99)
TO REPLACE DRIVE ASSEMBLY PIVOT CONE
BEARING
FOR SAFETY: Before Leaving Or
Servicing Machine; Stop On Level
Surface, Set Parking Brake.
1. Remove the drive assembly from the
machine. See TO REMOVE FRONT DRIVE
ASSEMBLY instructions.
2. Remove the four hex screws holding the
outer plate, drive motor, and drive hub
assembly to the main drive assembly.
3. Pull the drive hub, outer plate, and drive
motor assembly out of the drive wheel and
away from the drive assembly.
Summary of Contents for 6200D
Page 1: ...330395 Rev 01 6 02 Service Manual 6200D 330395 ...
Page 4: ...GENERAL INFORMATION 1 2 6200D 330395 8 99 ...
Page 18: ...GENERAL INFORMATION 1 16 6200D 330395 8 99 ...
Page 20: ...CHASSIS 2 2 6200D 330395 8 99 ...
Page 74: ...CHASSIS 2 56 6200D 330395 8 99 ...
Page 76: ...SWEEPING 3 2 6200D 330395 8 99 ...
Page 138: ...SWEEPING 3 64 6200D 330395 6 02 ...
Page 140: ...ELECTRICAL 4 2 6200D 330395 8 99 ...
Page 176: ...ELECTRICAL 6200D 330395 6 02 4 38 ELECTRICAL SCHEMATIC 353188 D ...
Page 177: ...ELECTRICAL 4 39 6200D 330395 6 02 WIRE HARNESSES GROUP 352986 353189 D ...
Page 178: ...ELECTRICAL 6200D 330395 6 02 4 40 WIRE HARNESSES GROUP 352986 353189 D ...
Page 179: ...ELECTRICAL 4 41 6200D 330395 6 02 WIRE HARNESSES GROUP 352986 353189 D ...
Page 180: ...ELECTRICAL 6200D 330395 6 02 4 42 WIRE HARNESSES GROUP 352986 353189 D ...
Page 181: ...ELECTRICAL 4 43 6200D 330395 6 02 WIRE HARNESSES GROUP 352986 353189 D ...
Page 182: ...ELECTRICAL 6200D 330395 6 02 4 44 WIRE HARNESSES GROUP 352986 353189 D ...
Page 184: ...HYDRAULICS 5 2 6200D 330395 8 99 ...
Page 212: ...HYDRAULICS 5 30 6200D 330395 8 99 HYDRAULIC SCHEMATIC PROPEL ...
Page 213: ...HYDRAULICS 5 31 6200D 330395 8 99 HYDRAULIC SCHEMATIC HOPPER LIFT ...
Page 214: ...HYDRAULICS 5 32 6200D 330395 6 02 OUT IN B A B A 2 3 4 5 6 1 HYDRAULIC HOSE DIAGRAM PROPEL ...
Page 215: ...HYDRAULICS 5 33 6200D 330395 6 02 HYDRAULIC HOSE DIAGRAM HOPPER LIFT ...
Page 220: ...2 2 General Purpose Motors ...
Page 227: ......
Page 228: ......
Page 229: ......
Page 230: ......
Page 248: ...ENGINE DIESEL 6 2 6200D 330395 8 99 ...