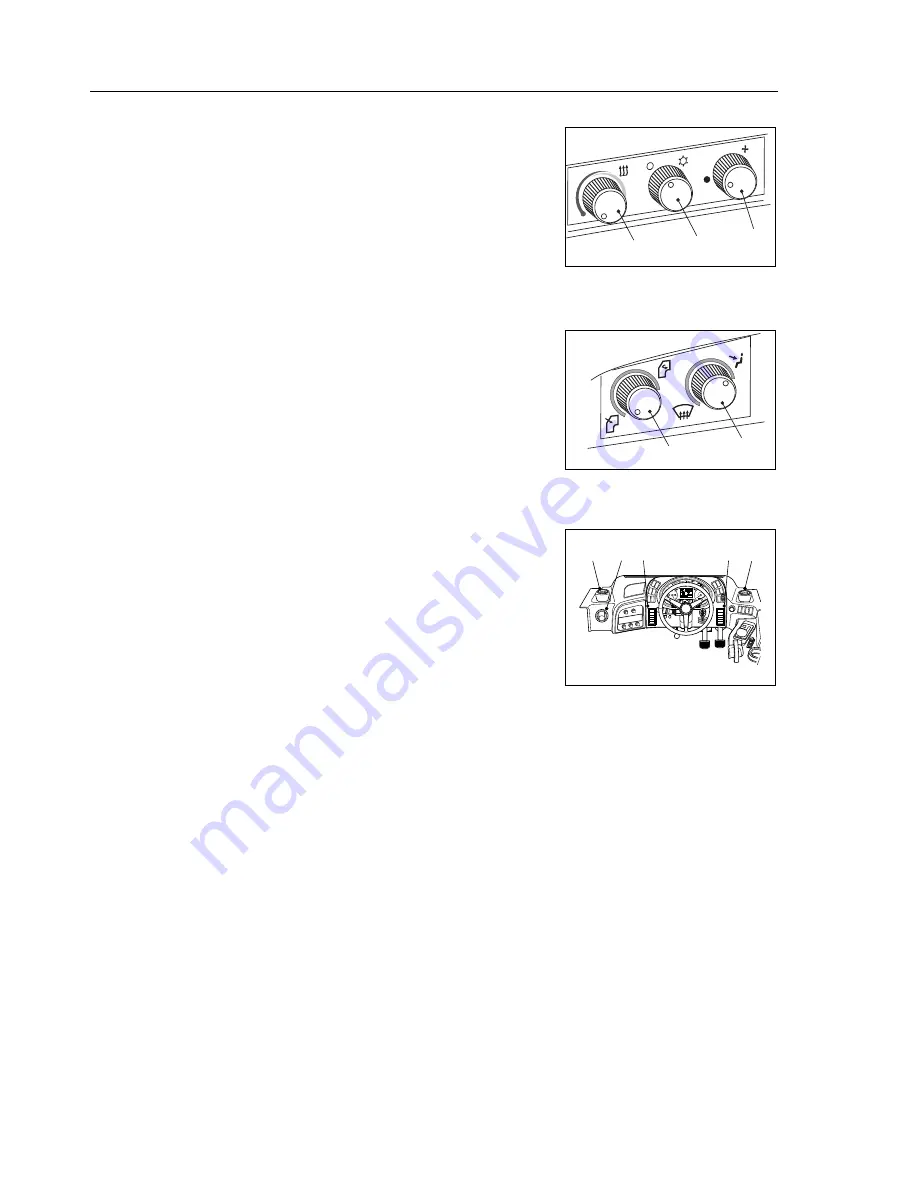
Controls and Operating
3-22
Heater
The blower control (3) is rotated to select one of three blower speeds. Air
direction can be adjusted by turning the direction controls (4 and 5).
The temperature control (1) is rotated to vary the heater output
temperature. Heater output air is unheated with the control turned fully
anticlockwise and heated by turning clockwise.
Heater/air conditioner outlets (6) may be adjusted to control the air flow
output by opening and closing the control flaps. Air direction can be
adjusted by rotating the complete outlet.
Air Conditioner
Keep all windows and vents closed.
Blower control (3) is rotated to select one of three blower speeds. The air
conditioning will not operate if the blower control is not switched on. Air
direction can be adjusted by turning the direction controls (4 and 5).
Turning control (2) to the right switches on the air conditioning. The air
conditioner output temperature can be controlled using the temperature
control (1).
The heater/air conditioner outlets (6) may be adjusted to control the air
flow output by opening and closing the control flaps. Air direction can be
adjusted by rotating the complete outlet.
NOTICE:
When the air conditioning is switched on, the engine cooling fan
automatically engages.
Air Condition Commissioning Procedure
If the machine has been idle overnight or for an extended period of time,
the refrigerant in the air conditioning unit converts from a gas to a liquid.
This puts the compressor unit under a great deal of strain trying to
compress a liquid instead of a gas, and could cause a failure of the air
conditioning unit.The following commissioning procedure allows the air
conditioning unit to achieve normal operating parameters.
1. Start the machine and allow it to run until the engine is at a normal
operating temperature of 80°C (176°F).
2. Turn the blower control to setting 1.
3. Turn on the air conditioning unit on for 5 seconds then off for
5 seconds.
4. Repeatedly switch the air conditioning on and off for at least 1 minute.
This should be at least 12 repetitions.
5. Commissioning the air conditioning unit is complete and ready for use.
NOTICE:
Follow the instructions given above, otherwise the machine may
be damaged.
1
2
3
3
2
1
1731
1730
4
5
CAN
ERROR
MCU
100%
TC
ERROR
CODE
MCU
88 : 88 : 88
ECU
TCU
OMNIA
999.9
1/h
AUTO
N
CONVERT
P
5
0
10
15
20
25
30
STOP
1
2
RE
AR
0
10
20
30
40
80
70
60
50
0
10
20
50
40
30
km/h
rpm
mph
000000
00_
6
6
6
6
6
MOT00307
Summary of Contents for TA400
Page 2: ...This page is intentionally left blank ...
Page 4: ...This page is intentionally left blank ...
Page 6: ...This page is intentionally left blank ...
Page 8: ...This page is intentionally left blank ...
Page 10: ...This page is intentionally left blank ...
Page 18: ...This Page is Intentionally Left Blank ...
Page 20: ...This Page is Intentionally Left Blank ...
Page 25: ...Safety 2 1 2 Safety ...
Page 26: ...Safety 2 2 This Page is Intentionally Left Blank ...
Page 52: ...Safety 2 28 This Page is Intentionally Left Blank ...
Page 53: ...Controls and Operating 3 1 3 Controls and Operating ...
Page 54: ...Controls and Operating 3 2 This Page is Intentionally Left Blank ...
Page 56: ...Controls and Operating 3 4 FUSE RELAY BOX ...
Page 109: ...Operating the Machine 4 1 4 Operating the Machine ...
Page 110: ...Operating the Machine 4 2 This Page is Intentionally Left Blank ...
Page 124: ...Operating the Machine 4 16 This Page is Intentionally Left Blank ...
Page 125: ...Working the Machine 5 1 5 Working the Machine ...
Page 126: ...Working the Machine 5 2 This Page is Intentionally Left Blank ...
Page 132: ...Working the Machine 5 8 This Page is Intentionally Left Blank ...
Page 133: ...Roading 6 1 6 Roading ...
Page 134: ...Roading 6 2 This Page is Intentionally Left Blank ...
Page 137: ...Moving a Disabled Machine 7 1 7 Moving a Disabled Machine ...
Page 138: ...Moving a Disabled Machine 7 2 This Page is Intentionally Left Blank ...
Page 140: ...Moving a Disabled Machine 7 4 This Page is Intentionally Left Blank ...
Page 141: ...Lubrication and Servicing 8 1 8 Lubrication and Servicing ...
Page 142: ...Lubrication and Servicing 8 2 This page is intentionally left blank ...
Page 160: ...Lubrication and Servicing 8 20 This page is intentionally left blank ...
Page 161: ...Technical Data 9 1 9 Technical Data ...
Page 162: ...Technical Data 9 2 This Page is Intentionally Left Blank ...
Page 169: ...Symbol Identification 10 1 10 Symbol Identification ...
Page 170: ...Symbol Identification 10 2 This Page is Intentionally Left Blank ...
Page 175: ...Symbol Identification 10 7 NOTES ...
Page 176: ...Symbol Identification 10 8 NOTES ...
Page 177: ...Symbol Identification 10 9 NOTES ...