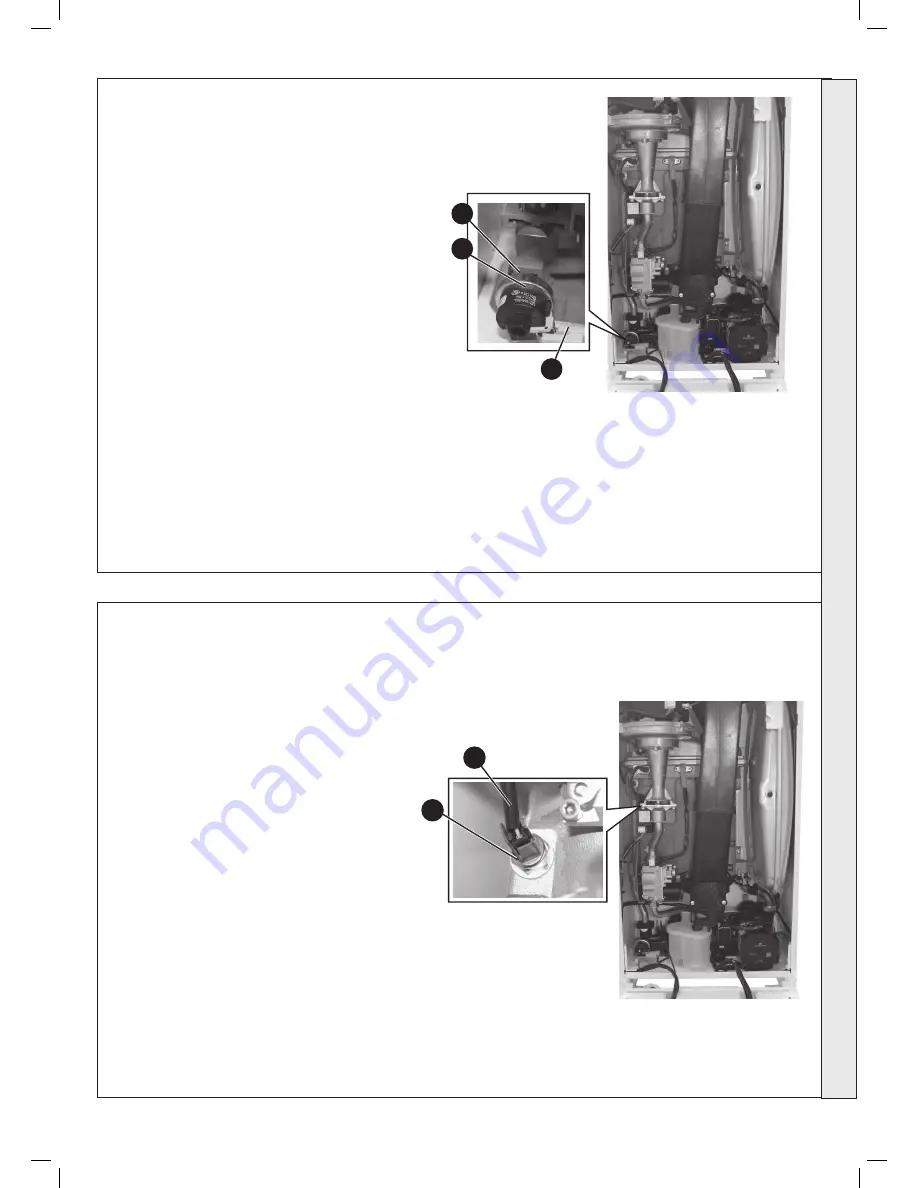
47
SERVICING
Installation and Servicing
1.
Refer to Frame 42.
2.
Drain down the boiler. Refer to Frame 55.
3.
Unplug the electrical lead.
4.
Unscrew the thermistor (to facilitate removal a
13mm socket spanner should be used).
5.
Fit the new thermistor using the sealing
washer provided.
6.
Reassemble in the reverse order.
7.
Refill the boiler. Refer to Frame 24.
8.
Check the operation of the boiler. Refer to
Frames 31 & 32.
64 CONTROL / NO FLOW THERMISTOR REPLACEMENT
63 CH WATER PRESSURE SENSOR REPLACEMENT
1. Refer to Frame 42.
2. Drain the boiler. Refer to Frame 55.
3. Pull off the two electrical connections.
4. Using a suitable tool, pull out the metal retaining clip.
5. Carefully withdraw the pressure switch.
6. Fit the new pressure switch and re-assemble in reverse
order.
7. Refill the boiler.
8. Check operation of the boiler. Refer to Frames 31 & 32.
4
3
3
4
5
SER
VICING