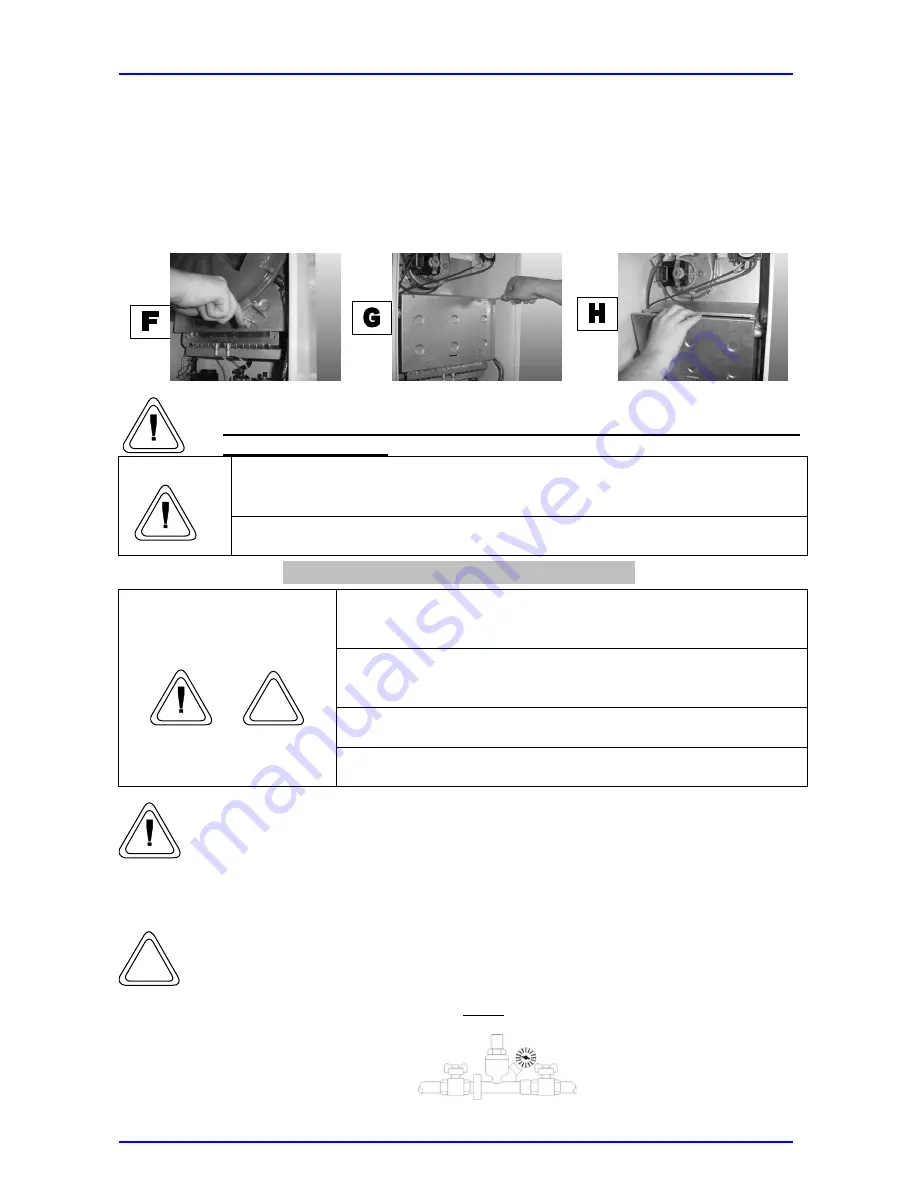
16
4. In order to access the combustion chamber:
•
Dismount the expansion tank by removing the fastening screws from the mounting
brackets (F).
•
Remove the screws (G) and pull out the front housing in order to separate it from the
lower drawbars (H) (carry out this operation very carefully to avoid damage to the
refractory panel installed there).
•
After any maintenance and/or control operations reset all initial
adjustment settings.
Before opening the boiler, empty all the components that may contain hot
water using the appropriate vent holes.
Warning
Tighten all the vent openings before carrying out gas pressure readings or
regulation.
Preparing the boiler for initial ignition
Use the externally fitted switch to cut off the power supply to
the boiler before carrying out any operation.
To guarantee the safe use of the boiler, the equipment must
be installed by a qualified registered installer, in accordance
with the corresponding regulations.
Do not carry out any operation without previously searching
for gas leaks with an appropriate device.
Warning
Do not carry out any operation without previously checking
that there are no naked flames or sparks.
While carrying out the above mentioned operations, only qualified personnel
must be present in the room where the boiler is installed.
Before the boiler ignition and functional test, perform the following checks:
•
Pre-loading of expansion tank;
•
Fill the water circuits as follows: Open the escape valve fitted in the
radiators; remove the automatic purge valve cap located on the pump;
gradually open the boiler inlet cock and close the air purge valve of the
radiators as soon as water starts to flow out. Close the inlet cock when the
water pressure gauge indicates
1 bar
.
Summary of Contents for Stella
Page 15: ...14 Electrical Layout Screw A pressure inlet ...
Page 25: ...24 ...