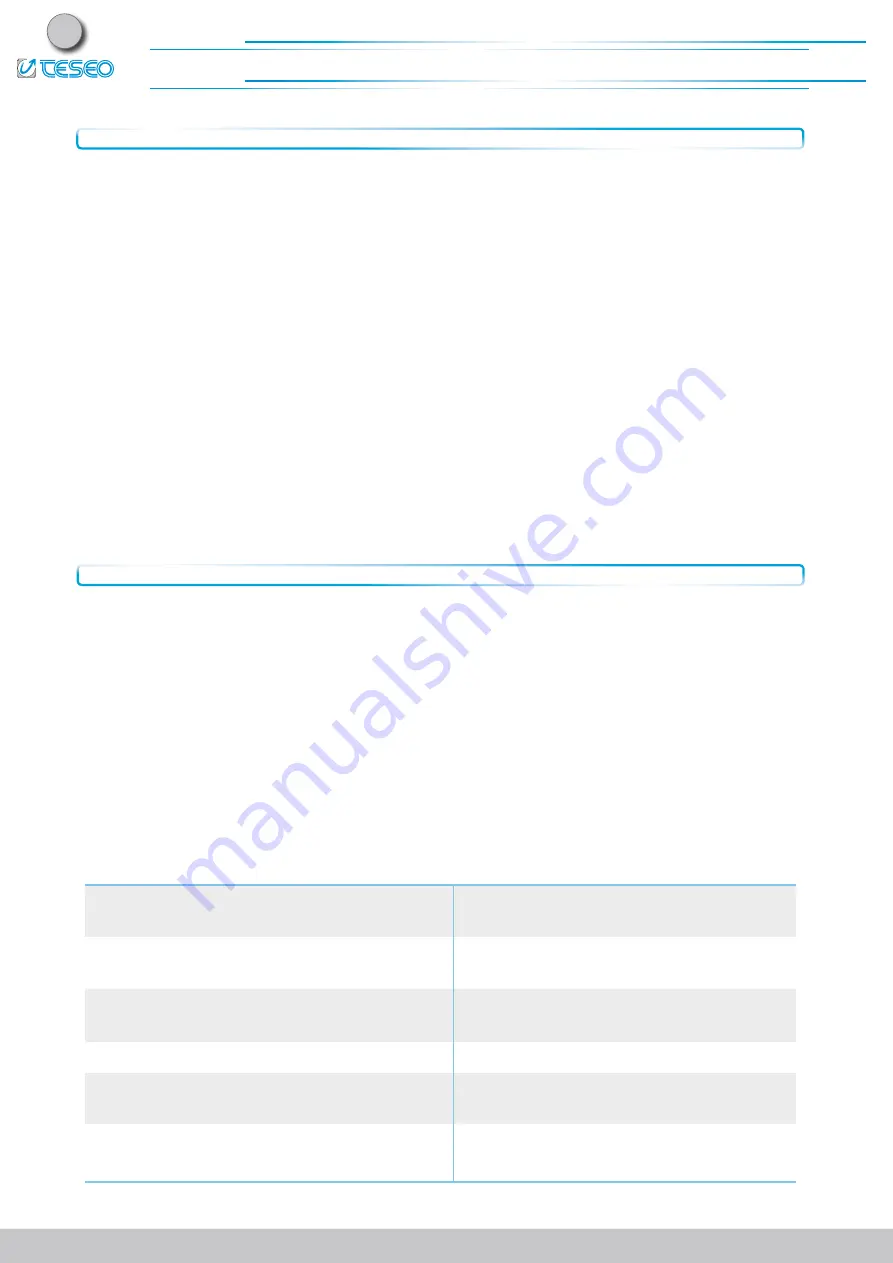
ALUMINIUM PIPEWORK - ALUMINIUM PIPEWORK - ALUMINIUM PIPEWORK - ALUMINIUM PIPEWORK - ALUMINIUM PIPEWORK - ALUMINIUM PIPEWORK
100
FLUID POWER DISTRIBUTION SYSTEMS - FLUID POWER DISTRIBUTION SYSTEMS - FLUID POWER DISTRIBUTION SYSTEMS - FLUID POWER DISTRIBUTION SYSTEMS - FLUID POWER DISTRIBUTION SYSTEMS
O ring seal damage due to incorrect installation,
or defective.
Replace the O ring seal.
Fitting or outlet plate threads damaged.
Seal with a Teflon band or replace the faulty piece.
The drilled hole on the bar is too big or misaligned.
Replace the faulty section of the hollow bar.
Extrusion blowholes into the hollow bar.
Replace the defective part.
Misaligned mounting of the joint in the corresponding
bar seats.
Disassemble the joint and realign the bars.
Defects in the seat of o ring of “l” and “T” joints.
Replace faulty joint.
CAUSE OF THE LEAK
CORRECTIVE ACTION (REMEDIAL)
8. REPAIRS AND MODIFICATIONS
8.1. Modifications to the system are quick and easy. We suggest preparing all tools in advance, next to the area
where modifications are to be made. By doing so, the downtime of the line is minimized.
8.2. If a leak is detected in the system, consult the following table where the most common causes and correspon-
ding remedies are described.
8.3. In the case of faulty pieces manufactured by TESEO, please contact our technical department.
8.4. ATTENTION: release pressure from the area of the system to be modified before carrying out re-
pairs, maintenance or modifications. Isolate the area and inform people about maintenance opera-
tions.
7. GENERAL TEST AND INSPECTION
7.1. Inspect every part of the system and check that no screw is loose, that all joints are properly in place and all
brackets are properly secured.
7.2. Check that the service valve placed between the compressor room and the line is closed.
7.3. Start the compressor and fill the tank up to the maximum pressure. If a compressor is not available, use nitro-
gen tanks and/or small portable compressors.
7.4. Open the valve and fill the system up to 1 bar approx. (15 psi); close the valve and check that no leaks are de-
tected in the system.
7.5. Increase the pressure of the system slowly until you reach the maximum pressure. Keep this pressure for
about 1 hour. Test the system when the pressure is 1.5 times higher than the working pressure.
7.6. Inspect the system again and check that no leaks or other unusual deformations are visible in the joints.
7.7. Empty the system.
7.8. ATTENTION: testing and inspection must be carried out only when no one is present in the working
area. Wear a safety helmet and protective glasses when inspecting the system. Please follow all sa-
fety precautions.