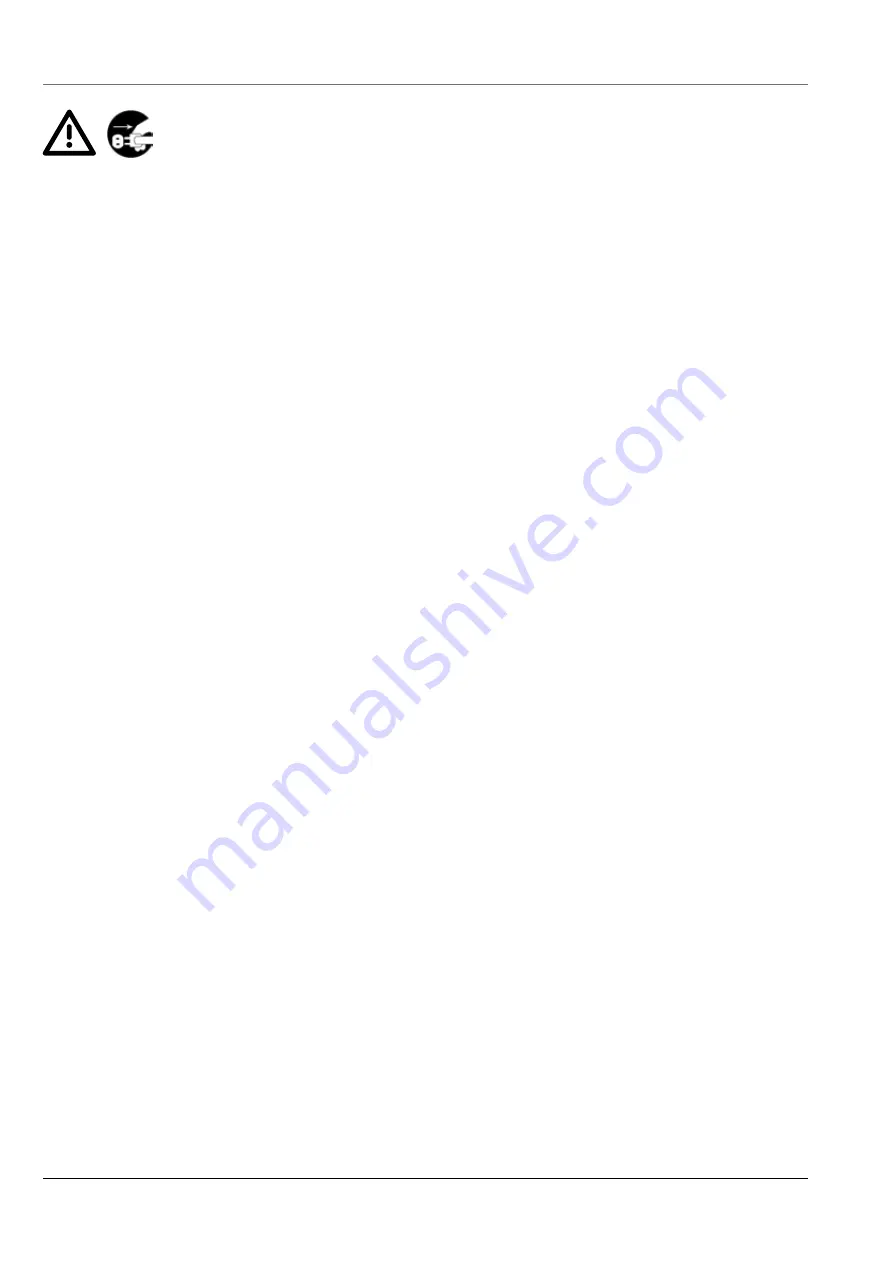
EX-TRACK
®
Operator Manual, Revision T-1
42
To keep the system in optimum condition, it is necessary to perform regular maintenance and
service. The following is a minimum requirement, dependent upon actual work conditions,
maintenance and service may need to be performed more frequently, it is advisable to setup a
maintenance schedule.
7.1. Cleaning the system
It is a requirement that the EX-TRACK
®
CNC Cutting System is checked for cleanliness prior to,
during and after the cutting process. Prior to any cleaning, isolate the electrical power supply to
the system. The drive mechanisms for the longitudinal and transverse rails needs to be checked
for any buildup of debris/dust/scale/slag, using a clean cloth/soft brush, clean down the area, do
not use abrasive cleaning tools such as a steel wire brush, this will damage the material surface,
making it more prone to contaminants sticking and building up. The track and rack should be
constantly monitored for debris buildup, use a soft brush, cloth or clean dry compressed air to
remove any contaminants, lubricants may be used on the rack, but sparingly as excessive lubricant
will attract a contaminant buildup. Keep the system main unit clean, use a soft cloth to wipe down
the CNC/operator panel, ensure that the USB port cover is fully closed when not in use and keep the
surrounding area clean.
7.2. System lubrication
Prior to each use of the system, the operator should ensure that the drive mechanisms have been
lubricated. An indication of excessive wear to the drive mechanism or rack is noted when cut parts
display an irregular edge surface.
7.3. Drive motor adjustment
After a period of use, it is normal for working parts of the system to show varying degrees of wear.
A suitably qualified person can perform adjustments to the drive motors to realign the system and
maintain cutting accuracy.
7.4. Oxy fuel nozzle maintenance
Cut quality is affected by the condition of the nozzle, in order to clean and maintain the nozzle
correctly, the nozzle should be removed from the torch, use two wrenches for this action. Inspect the
nozzle for wear, remove any spatter/dross/slag or soot buildups, do not use a steel wire brush, and
use the supplied nozzle kit to clean the nozzle. Re-fit the nozzle after cleaning, check for leaks and
make a short test cut to ensure that the nozzle is cutting true.
Summary of Contents for EX-TRACK
Page 101: ...EX TRACK Operator Manual Revision T 1 101 Shape 1 Shape 2 Shape 3...
Page 102: ...EX TRACK Operator Manual Revision T 1 102 Shape 4 Shape 5 Shape 6...
Page 103: ...EX TRACK Operator Manual Revision T 1 103 Shape 7 Shape 8 Shape 9...
Page 104: ...EX TRACK Operator Manual Revision T 1 104 Shape 10 Shape 11 Shape 12...
Page 105: ...EX TRACK Operator Manual Revision T 1 105 Shape 13 Shape 14 Shape 15...
Page 106: ...EX TRACK Operator Manual Revision T 1 106 Shape 16 Shape 17 Shape 18...
Page 107: ...EX TRACK Operator Manual Revision T 1 107 Shape 19 Shape 20 Shape 21...
Page 108: ...EX TRACK Operator Manual Revision T 1 108 Shape 22 Shape 23 Shape 24...
Page 109: ...EX TRACK Operator Manual Revision T 1 109 Shape 25 Shape 26 Shape 27...
Page 110: ...EX TRACK Operator Manual Revision T 1 110 Shape 28 Shape 29 Shape 30...
Page 111: ...EX TRACK Operator Manual Revision T 1 111 Shape 31 Shape 32 Shape 33...
Page 112: ...EX TRACK Operator Manual Revision T 1 112 Shape 34 Shape 35 Shape 36...
Page 113: ...EX TRACK Operator Manual Revision T 1 113 Shape 37 Shape 38 Shape 39...
Page 114: ...EX TRACK Operator Manual Revision T 1 114 Shape 40 Shape 41 Shape 42...
Page 115: ...EX TRACK Operator Manual Revision T 1 115 Shape 43 Shape 44 Shape 45...
Page 116: ...EX TRACK Operator Manual Revision T 1 116 Shape 46 Shape 47 Shape 48...
Page 117: ...EX TRACK Operator Manual Revision T 1 117 Shape 49 Shape 50...
Page 118: ...EX TRACK Operator Manual Revision T 1 118 Notes...