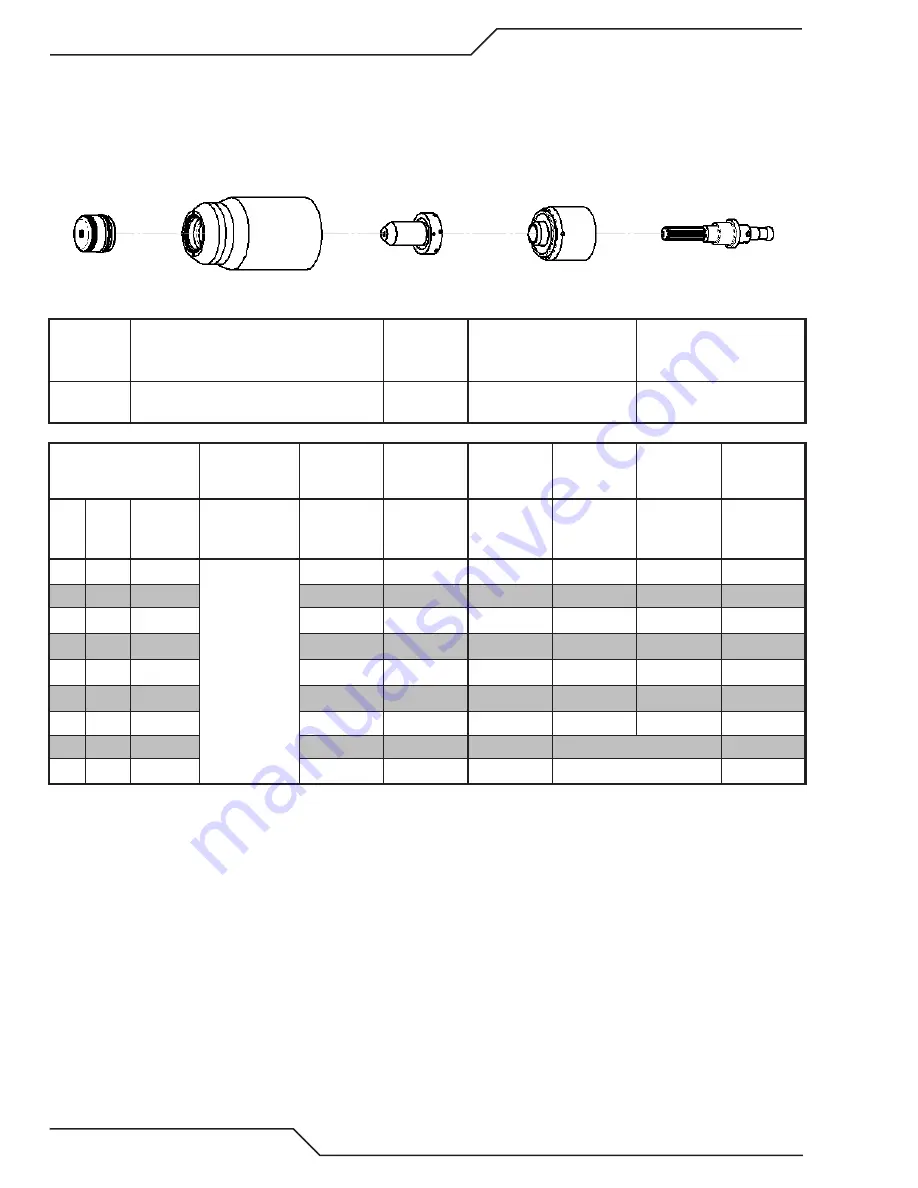
A40i, A60i
OPERATION
Manual 0-5466
4T-32
Aluminum
60A
Air Plasma / Air Shield
Shield Cap
Maximum Life Shield Cup
Tip
Starter Cartridge
Heavy Duty Starter
Cartridge
Electrode
9-8238
9-8237
9-8210
9-8213
9-8277
9-8232
Material
Thickness
Gas Pressure
(Air)
Arc Voltage
Torch
Working
Height
Travel Speed
Initial
Piercing
Height
Pierce Delay
Kerf Width
@ Rec.
Speed
(GA)
(in)
inch
PSI
(torch lead
length)
Volts
(in)
(ipm)
(in)
(sec)
(in)
16
0.064
85 (25')
90 (50')
118
0.13
350
0.25
0.00
0.07
14
0.079
118
0.13
350
0.25
0.10
0.08
11
0.120
123
0.13
275
0.25
0.10
0.08
3/16
0.188
125
0.13
140
0.25
0.20
0.08
1/4
0.250
132
0.13
80
0.25
0.30
0.08
3/8
0.375
135
0.13
45
0.25
0.50
0.08
1/2
0.500
140
0.13
26
0.25
0.80
0.08
5/8
0.625
148
0.19
18
Edge start
0.10
3/4
0.750
155
0.19
12
Edge start
0.11
Summary of Contents for A40i
Page 6: ...This Page Intentionally Blank...
Page 8: ...This Page Intentionally Blank...
Page 12: ...TABLE OF CONTENTS This Page Intentionally Blank...
Page 16: ...A40i A60i WARRANTY INFORMATION Manual 0 5466 W 2 This Page Intentionally Blank...
Page 24: ...A40i A60i INTRODUCTION Manual 0 5466 2T 4 This Page Intentionally Blank...
Page 32: ...A40i A60i INSTALLATION Manual 0 5466 3 8 This Page Intentionally Blank...
Page 34: ...A40i A60i INSTALLATION Manual 0 5466 3T 2 This Page Intentionally Blank...
Page 80: ...A40i A60i OPERATION Manual 0 5466 4T 36 This Page Intentionally Blank...
Page 95: ...A40i A60i Manual 0 5466 PARTS LIST 6 3 This Page Intentionally Blank...
Page 99: ...A40i A60i Manual 0 5466 PARTS LIST 6 7 A 07994_AB 1 4 2 3 5 6 7 8 9 10 12 11 10 13...
Page 110: ...A40i A60i APPENDIX Manual 0 5466 A 10 APPENDIX 8 SYSTEM SCHEMATIC 400V 3PHASE CE Art A 13478...
Page 111: ...A40i A60i Manual 0 5466 APPENDIX A 11 Art A 13478...
Page 112: ...A40i A60i APPENDIX Manual 0 5466 A 12 APPENDIX 9 SYSTEM SCHEMATIC 208 480V 3PHASE Art A 13479...
Page 113: ...A40i A60i Manual 0 5466 APPENDIX A 13 Art A 13479...
Page 115: ...This Page Intentionally Blank...