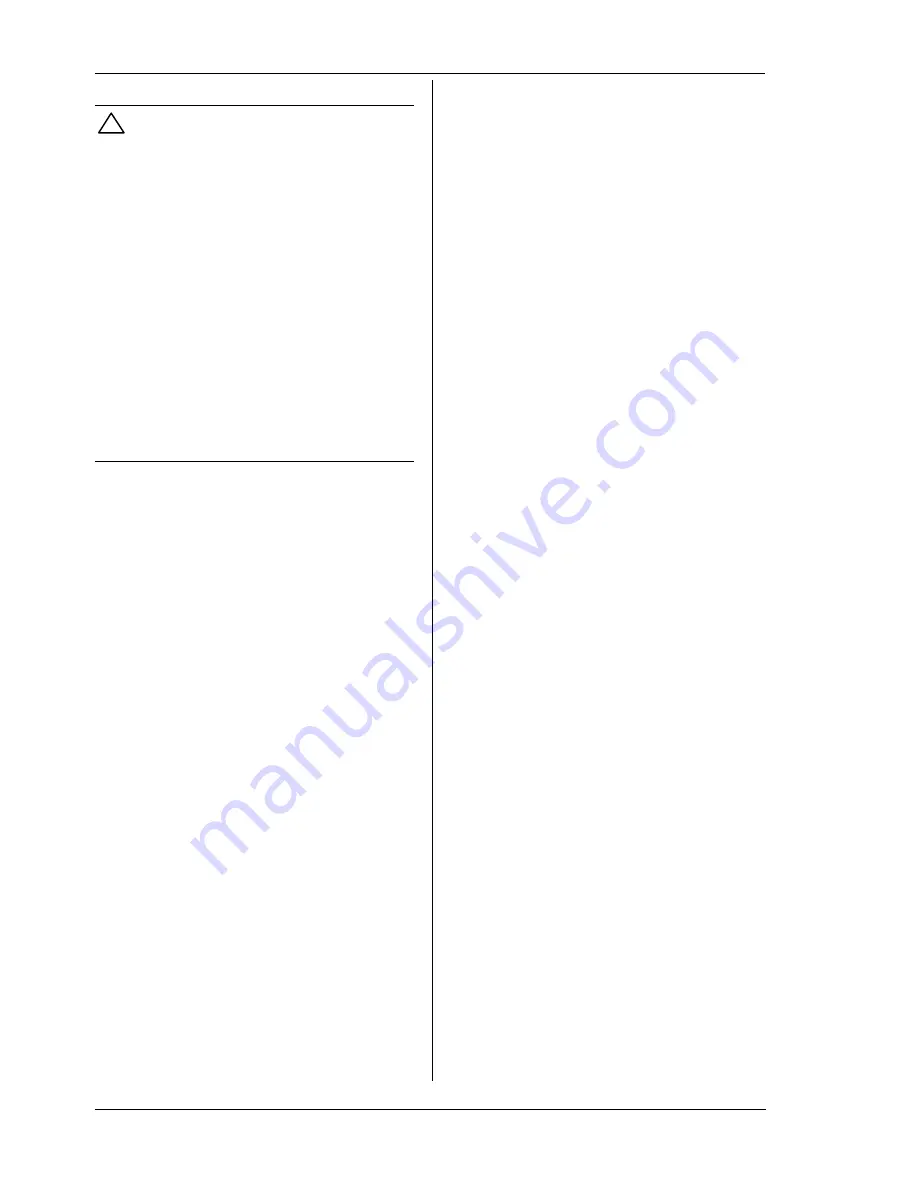
User Manual
3200 Series
92 Part No HA028651 Issue 11.0 July-12
15.3
EEPROM Write Cycles
!
Warning
In common with most instruments in its class, the
3200 Range uses a non-volatile memory with a
limited number of specified writes. Non-volatile
memory is used to hold information that must be
retained over a power cycle. Typically, this includes
setpoint and status information, including alarm
latch status.
Please ensure that parameters which do not require
updating on a regular basis (for example, setpoints,
alarm trip levels, hysteresis, etc) are only written to
when a change in the parameter value occurs.
Failure to do this could result in permanent damage
to the internal EEPROM.
When using the 3200 range, use the ‘AltSP’ variable
at Modbus address 26, which has no write
restrictions, if you need to write to a temperature
setpoint. A local trim value may also be applied
using the ‘SPTrim’ parameter at Modbus address 27.
Some examples of parameters which could cause this
limit to be exceeded over a period of time are given
below.
Setpoint Ramping
Continuous changing of setpoint via digital
communications – for example a ramping value – is the
most common cause of EEPROM wear.
One solution, as stated above, is to enable the “Alternate
Setpoint” (address 276), then write values directly to the
“Alternate Setpoint, AltSP” (address 26). These
parameters may be found in the SP list in iTools and are
L-R
and
REM.SP
in the controller. Note that an
approximately 5 second timeout is applied to writes to
Modbus address 26. This, therefore requires regular
updating which, for setpoint ramping, is ideally suited.
In other applications where regular updating may not be
ideal, this may be avoided by writing to the “Target
Setpoint” at address 02. The Alternate Setpoint must
also be enabled at address 276. The value written to
address 02 will then be written permanently to address
26. Note, however, that any value written to the Target
Setpoint will not be retained over a power fail since the
controller then reverts to the setpoint selected (for
example, SP1 or SP2).
It is
critically
important
to select the Alternate Setpoint
if updating the setpoint on a regular basis otherwise the
setpoint change will be saved to non-volatile memory
and EEPROM wear will result.
Alarms and other Status Changes
Alarm status is saved in non-volatile memory and this
includes status alarms such as sensor break, loop break,
remote fail and individual alarm and alarm latching
status. Every transition into and out of an alarm
condition triggers an EEPROM write. Thus, if there is any
fast toggling of an alarm status, EEPROM wear can result
within the expected lifetime of an instrument.
An example of this is where event alarms are used to
provide an on/off control loop. 3200 instruments should
on no account be used in this manner since the toggling
of the output will rapidly use up the 100,000 writes. The
On/Off control in the PID algorithm should be used
instead. However, any situation where alarm states can
change rapidly should be avoided.
Mode and Timer/Programmer Changes
Rapid changes to instrument mode (Auto/Manual) or the
Timer/Programmer operation can cause EEPROM wear
because the status (run/hold/reset) or the segment
number are stored in EEPROM on each transition.
In normal use where segments or timer sequences are
relatively long, it is unlikely that problems will be seen.
However, in some applications where a sequence is run
frequently, EEPROM wear will occur. An example of this
is where a digital input is used in an application to trigger
a timer sequence and the operation is performed as fast
as possible by the operator.
Digital Inputs
Care should be taken with any rapid cycling digital
inputs. Typically a digital input triggering timer or mode
changes (as above) should be carefully considered so
that they do not switch more than 100,000 times during
the expected lifetime of the instrument.
.
Summary of Contents for XST-2-0-12-1V1-E28
Page 16: ...12 FURNACE TROUBLE SHOOTING ...
Page 27: ...ɸ ...
Page 28: ...ɸ ...
Page 29: ......
Page 30: ......
Page 31: ...3216 3208 3204 User Manual 3200 Range Process Controller HA028651 11 Aug 2012 ...
Page 170: ...User Manual 3200 Series 138 Part No HA028651 Issue 11 0 July 12 21 Certificate of Conformity ...
Page 171: ......
Page 173: ...Model 2416 Process Controller User Manual Part No HA025041_12 Date August 2014 ...
Page 174: ...This page is intentionally blank ...
Page 259: ...This page is intentionally blank ...