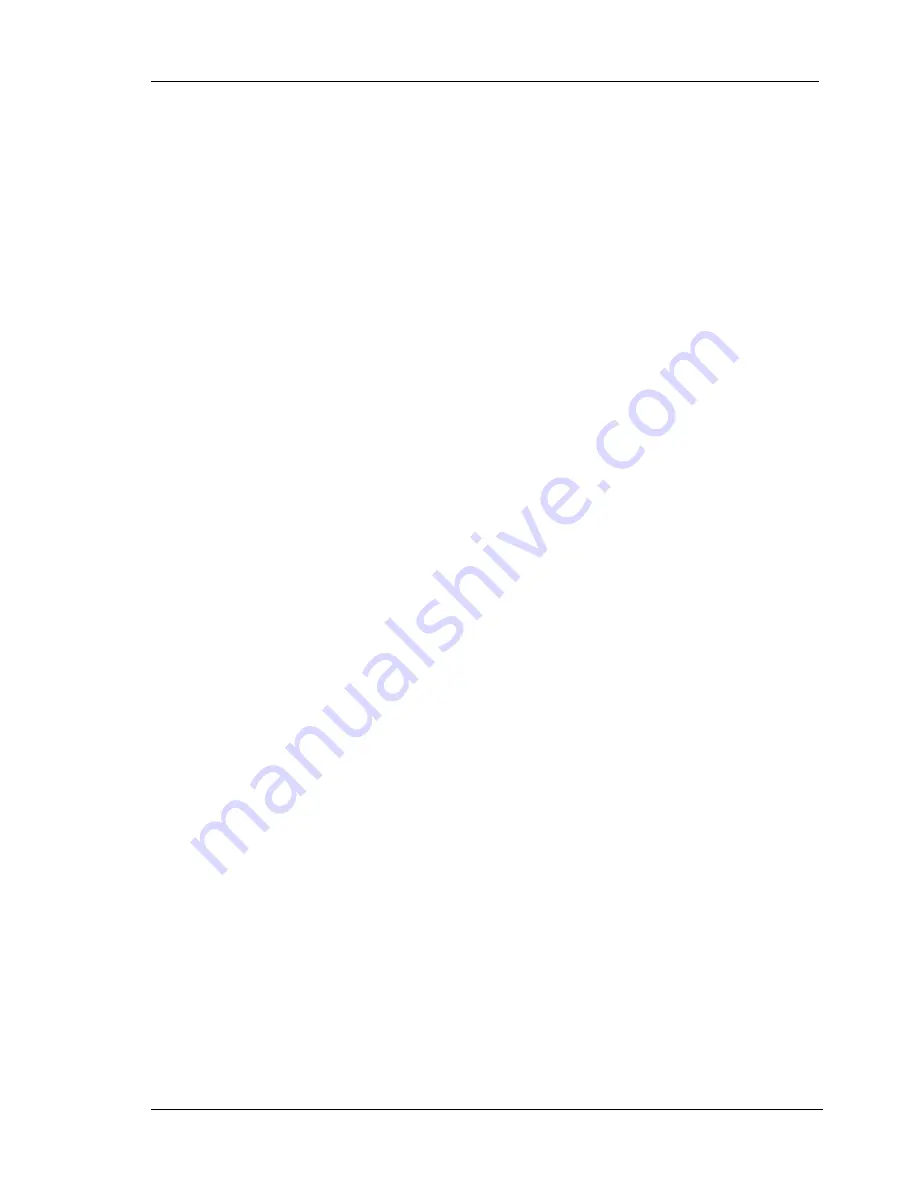
3200 Series
User Manual
Part No HA028651 Issue 11.0 July-12 61
11.3
Tuning
In tuning, you match the characteristics (PID parameters) of the controller to those of the process being controlled in
order to obtain good control. Good control means:
•
Stable, ‘straight-line’ control of the PV at setpoint without fluctuation
•
No overshoot, or undershoot, of the PV setpoint
•
Quick response to deviations from the setpoint caused by external disturbances, thereby rapidly restoring the PV to
the setpoint value.
Tuning involves setting the following parameters:-
Proportional Band ‘PB’, Integral Time ‘TI’, Derivative Time ‘TD’, Cutback High ‘CBHI’, Cutback Low ‘CBLO’, and Relative
Cool Gain ‘R2G’ (applicable to heat/cool systems only).
The controller is shipped with these parameters set to default values. In many cases the default values will give adequate
stable straight line control, however, the response of the loop may not be ideal. Because the process characteristics are
fixed by the design of the process it is necessary to adjust the control parameters in the controller to achieve best
control. To determine the optimum values for any particular loop or process it is necessary to carry out a procedure
called loop tuning. If significant changes are later made to the process which affect the way in which it responds it may
be necessary to retune the loop.
Users have the choice of tuning the loop automatically or manually. Both procedures require the loop to oscillate and
both are described in the following sections.
11.3.1
Loop Response
If we ignore the situation of loop oscillation, there are three categories of loop performance:
Under Damped
- In this situation the terms are set to prevent oscillation but do lead to an overshoot of the Process
Value followed by decaying oscillation to finally settle at the Setpoint. This type of response can give a minimum time to
Setpoint but overshoot may cause problems in certain situations and the loop may be sensitive to sudden changes in
Process Value. This will result in further decaying oscillations before settling once again.
Critically Damped
- This represents an ideal situation where overshoot to small step changes does not occur and the
process responds to changes in a controlled, non oscillatory manner.
Over Damped
- In this situation the loop responds in a controlled but sluggish manner which will result in a loop
performance which is non ideal and unnecessarily slow.
The balancing of the P, I and D terms depends totally upon the nature of the process to be controlled.
In a plastics extruder, for example, a barrel zone will have a different response to a die, casting roll, drive loop, thickness
control loop or pressure loop. In order to achieve the best performance from an extrusion line all loop tuning
parameters must be set to their optimum values.
11.3.2
Initial Settings
In addition to the tuning parameters listed in section 11.3 above, there are a number of other parameters which can have
an effect on the way in which the loop responds. Ensure that these are set before either manual or automatic tuning is
initiated. Parameters include, but are not limited to:-
Setpoint
. Set this as closely as practicable to the actual setpoint in normal operation.
Load Conditions.
Set the load conditions as closely as possible to those which will be met in practice. For example, in a
furnace or oven application a representative load should be included, an extruder should be running, etc.
Heat/Cool Limits.
The minimum and maximum power delivered to the process may be limited by the parameters
‘OUTPUT LOW’ and ‘OUTPUT HIGH’ both of which are found in the Control list. For a heat only controller the default
values are 0 and 100%. For a heat/cool controller the defaults are -100 and 100%. Although it is expected that most
processes will be designed to work between these limits there may be instances where it is desirable to limit the power
delivered to the process. For example, if driving a 220V heater from a 240V source the heat limit may be set 80% to
ensure that the heater does not dissipate more than its maximum power.
☺
The measured value
must
oscillate to some degree for the tuner to be able to calculate values. The limits must be
set to allow oscillation about the setpoint.
Summary of Contents for XST-2-0-12-1V1-E28
Page 16: ...12 FURNACE TROUBLE SHOOTING ...
Page 27: ...ɸ ...
Page 28: ...ɸ ...
Page 29: ......
Page 30: ......
Page 31: ...3216 3208 3204 User Manual 3200 Range Process Controller HA028651 11 Aug 2012 ...
Page 170: ...User Manual 3200 Series 138 Part No HA028651 Issue 11 0 July 12 21 Certificate of Conformity ...
Page 171: ......
Page 173: ...Model 2416 Process Controller User Manual Part No HA025041_12 Date August 2014 ...
Page 174: ...This page is intentionally blank ...
Page 259: ...This page is intentionally blank ...