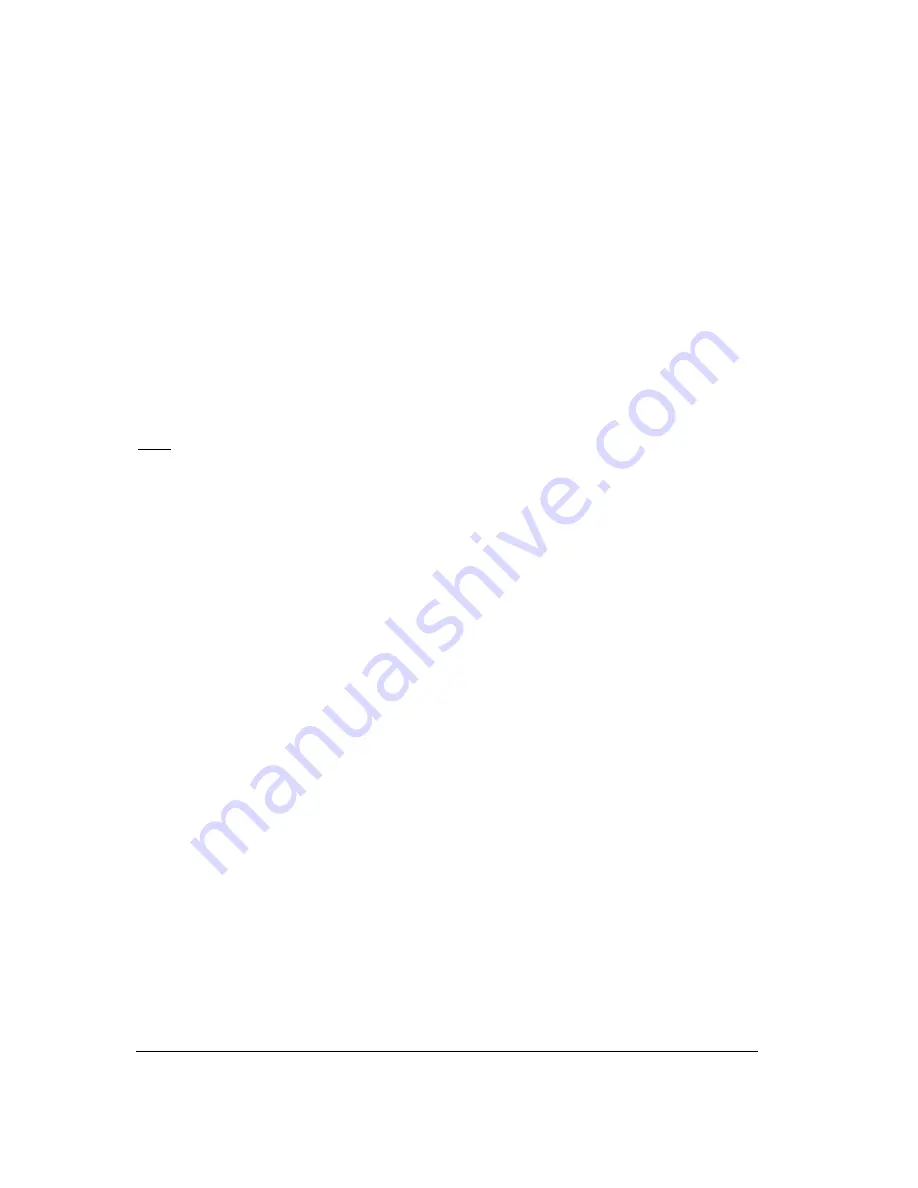
DTH Electric Boilers USE & CARE MANUAL
(Revision June 2014)
, Page
7.
Use only clean, new piping for boiler water lines.
Local codes or regulations shall govern the
exact type of material to be used.
Insulate all pipes containing hot water,
especially in unheated areas.
Install shutoff (ball) valves for servicing
convenience. Thermometer(s) should be
installed on the boiler water supply and return
lines.
Cap or plug unused connections on the boiler.
Do not cap the pressure relief valve on the
boiler since it will damage and shorten the life of
the boiler and may endanger life and property.
3.4.2 Flow check valve
If the heating system includes a single pump,
then to minimize flow by gravity and heat loss
during non-draw periods, a flow check valve
must be installed.
3.4.3 Pressure relief valve
An automatic pressure relief valve must be
installed during boiler setup. The pressure
rating of the relief valve must not exceed the
pressure design of the boiler as shown on the
pressure vessel name plate. The safety relief
valve must meet the requirements of the ASME
Boiler and Pressure Vessel Code and limit the
maximum operating boiler pressure. It is a
safety device, not an operating control.
The BTU per hour rating of the relief valve must
equal or exceed the BTU per hour input of the
boiler(s) or heat source(s) as marked on the
boiler(s) rating plate.
Connect the outlet of the relief valve to a
discharge line with its lower tip at most 6” above
a floor drain, well clear of any live electrical
parts. The discharge line must pitch downward
from the valve to allow complete draining by
gravity of the relief valve and discharge line, and
be of a diameter no smaller than that of the
valve outlet. The tip of the discharge line should
not be threaded or concealed and should be
protected from freezing. No valve of any type,
restriction or reducer coupling should be
installed on the discharge line. Local codes
shall govern the installation of relief valves.
3.4.4 System pressure control and
expansion tank
Pressure control devices within the system
ensure that each component operates within
minimum and maximum allowable pressures
and maintain minimum pressure for all normal
operating temperatures. They also allow air
bleeding, prevent cavitation at the pump inlet
and prevent water from boiling within the
system; all this is accomplished with minimal
addition of new water.
The increase in boiler water volume resulting
from higher temperature is stored in the
expansion tank during periods of high operating
temperature and is returned to the system when
the temperature decreases.
The expansion tank must be able to store the
required volume of boiler water during maximum
design operating temperature without exceeding
the maximum allowable operating pressure, and
to maintain the required minimum pressure
when the system is cold. Contact your installing
contractor, plumbing supply house, or local
plumbing inspector for assistance.
The point where the expansion tank is
connected should be carefully selected to avoid
the possibility that normal operation of automatic
check or manual valves will isolate the tank from
a hot boiler or any part of the system. Pre-
charged diaphragm expansion tanks are
preferable to air control (see section 3.4.6).
These tanks incorporate a balloon-like bladder
or diaphragm. It is inflated, prior to filling the
system, to a pressure equal to the setting of the
water pressure makeup regulator.
The expansion tank should be located on the
suction or intake side of the pump. The pump
can be located either just upstream or just
downstream from the boiler.
3.4.5 Water pressure makeup regulator
Make-up systems must be employed as
required by codes. An automatic fill valve
must be used with a backflow preventer as
required, to maintain minimum system pressure
by supplying water to make up for leakage.
3.4.6 Air bleeder
Oxygen should be excluded from the system to
prevent corrosion. As hinted at in section 3.4.4,
this precludes the use of air in direct contact with
the boiler water as a pressurization means.
Installation of manual or automatic air vent
devices prevents air from accumulating in the
system. Air vents should be installed at all high
points to remove trapped air during initial setup
and to ensure that the system is tight. Regularly
purge the air out of the system while taking care
to avoid personal injuries or property damage
caused by hot boiler water spray.