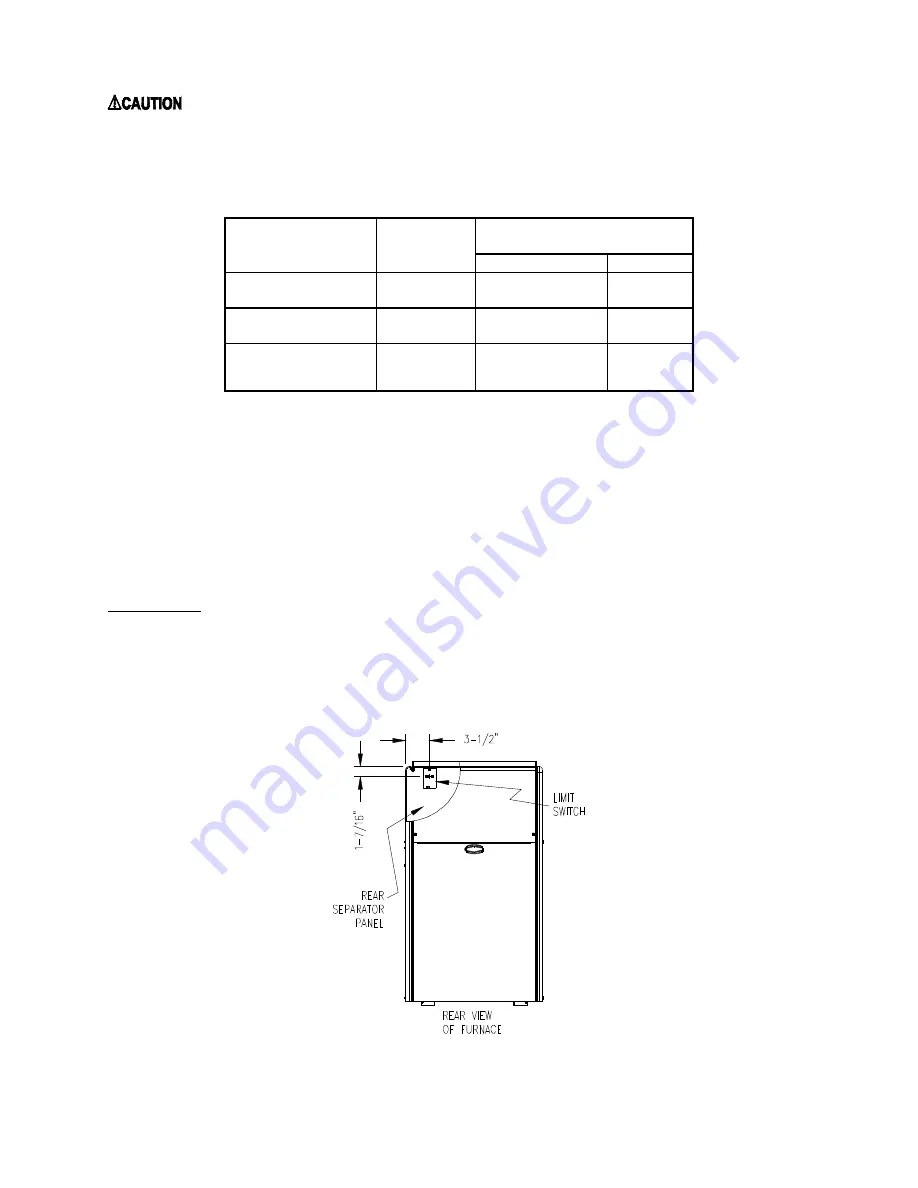
16
:
Failure to comply with minimum filter installation requirements may affect the
performance and/or void the warranty on this unit.
If a method other than internal Thermo Pride filter rack is selected for retention of the filters and/or use of
a different filter type is desired, refer to Table 4 below for minimum sizing guidelines for selecting filter for
the unit.
Filter Type
Maximum
Air Velocity
(ft/min)
Model Number
OL6
Qty
*Thermo Products
Supplied Permanent
600
280 in²
2
Standard
Permanent
500
576 in²
2
Disposable
300
960 in²
2
Table 4: Minimum Required Filter Area (in square inches)
* The Thermo Products supplied filter can be cut to size to fit other filter retention systems as
long as the maximum air velocity is not exceeded.
NOTICE: Any internal stiffeners used in the filter must not be removed, although
they can be cut to size as needed.
F. LIMIT POSITION AND LOCATION
c
WARNING:
The predetermined limit locations on all of the Thermo Pride oil fired furnaces have been
tested and approved by Thermo Products, LLC. Any attempt to relocate these safety controls or replace
these safety controls with a control that is not approved, or is incompatible, may result in personal injury,
substantial property damage or death.
The unit must have the limit control installed at the time of unit installation.
Fig. 11: Limit location for OL6
Summary of Contents for OL6FA072D48
Page 2: ......
Page 4: ......
Page 7: ...2...
Page 56: ...51 VIII Sequence of Operations Flow Chart...
Page 57: ...52...
Page 58: ...53 IX Trouble Shooting Flow Chart...
Page 59: ...54...
Page 60: ...55...
Page 61: ...56...
Page 62: ...57...