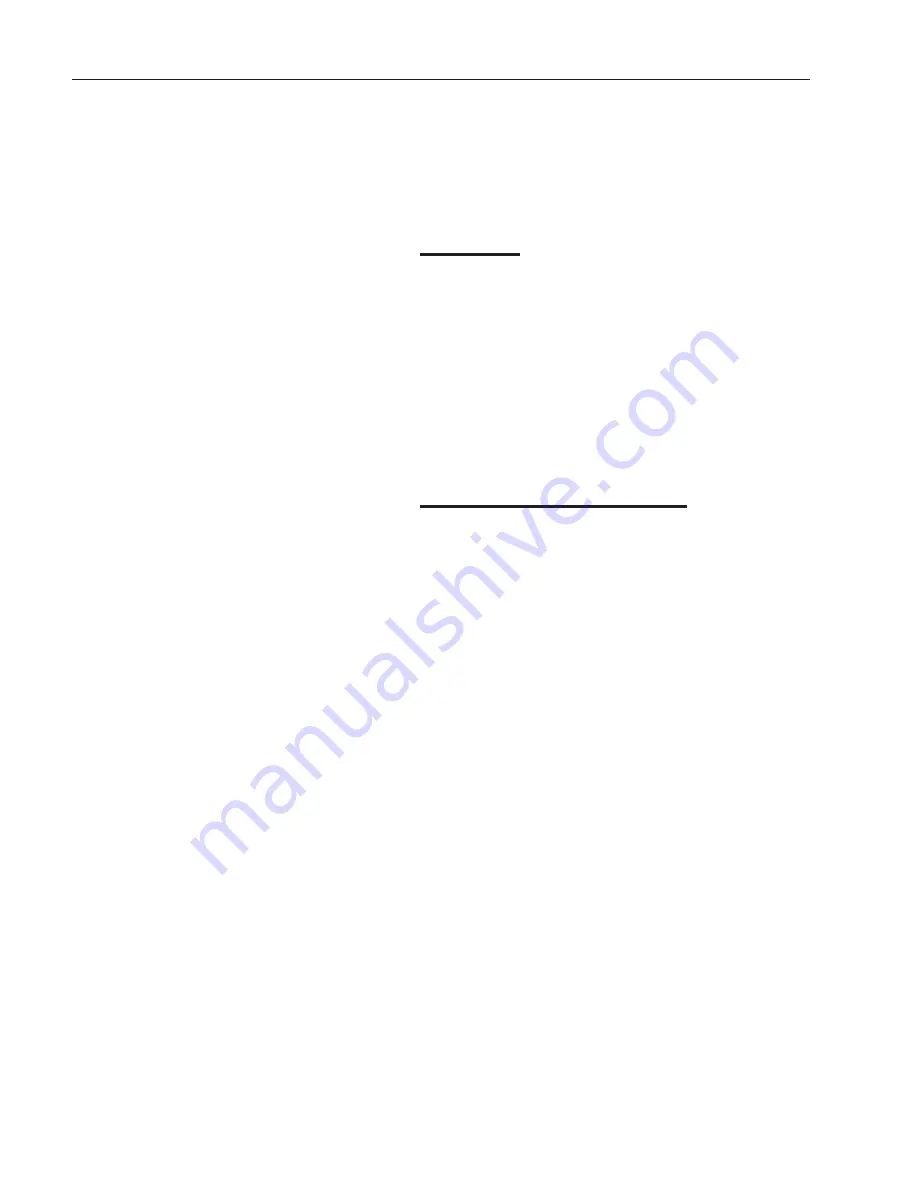
8
Controls
Power ON/OFF Switch:
Located on back wall of chamber, is used to turn power
ON or OFF to entire unit.
Keys:
Located on front panel.
MENU - Used to access controller menus.
SET
- Used to display setting.
L
INCREASE setting.
M
DECREASE setting.
Display and Indicators
DISPLAY:
(On front panel)
Displays chamber and set point temperatures in °C and
prompts from menu.
INDICATORS:
(On front panel)
DELAY:
Lights when delay start timer for compressor is
timing. Will begin timing when power is first applied or
when cooling compressor is turned off.
ALARM:
Indicates that chamber temperature is not within
limits and the safety relay is opened.
COOL:
Lit when cooling compressor is on.
HEAT:
Lights when controller demands heat.
Controls and Displays