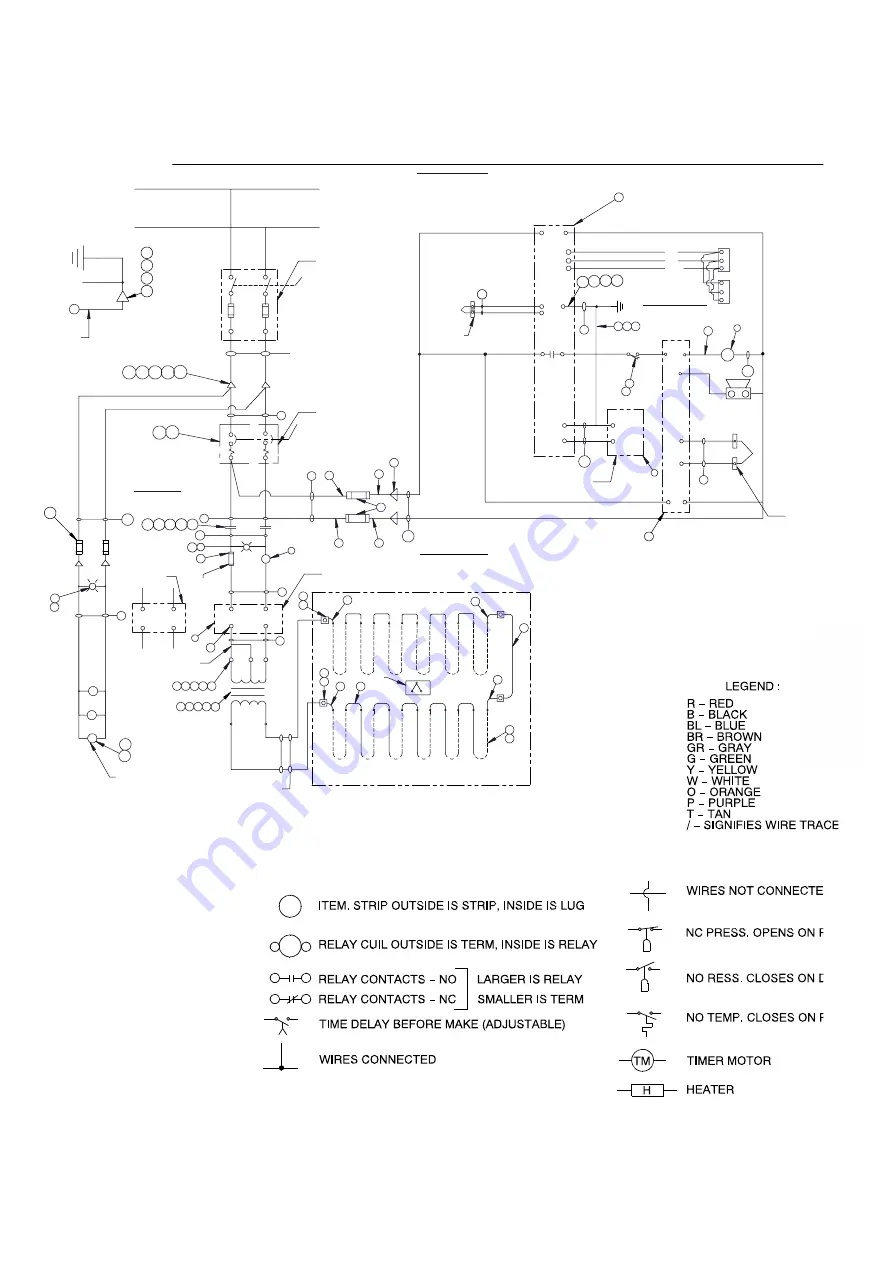
Replacement Parts
WIRING DIAGRAMS
Thermo Scientific
11-3
WIRING DIAGRAMS
Figure 8. Wiring Diagram (Sheet 1 of 2)
21
R
L1
L2
SEE NOTE "A"
FURNACE
GROUND
BY
CUSTOMER
EQUIPMENT GROUND
TO TERMINAL BAR
APPROX. 23 AMPS @ 240 VOLTS
IL2
ITB
IL1
43
61
69
76
36
1 T/C
(1 XT)
TC
-
+
RIGHT HEATING ELEMENTS
16
13
14
208/240 VOLTS, 1 PHASE, 50/60 HZ.
150
150
150
1T/C
GR
R
B
150
UT350/UP550
TEMPERATURE
CONTROLLER
151
B
8
9
23&25
27
+
-
13
12
1PM
-5
+6
CONTROL CIRCUIT
R
B
GND
OPTIONAL
DB9
COMMS
PORTS.
3
2
5
2
5
3
GND
10
CHASSIS GROUND
SEE NOTE "A"
21
22
NO ILS
UT150L
EXCESS TEMP.
IC
EXCESS TEMP OPTIONAL
14
15
13
22(22A)
151
+
1XT
-
R
B
16 +
17 -
DC O/P1
4-20 MA
7
6
EXCESS
TEMP.
+
-
24&26
41
61
69 76
34
47
SEE NOTE "G"
33
21
23
24
3
SEE NOTE"D"
151
10
9
SEE NOTE "E"
151
24
24
7
8
+
-
GR
R
21
2
151
NOTE: INDIVIDUAL WIRE
CONNECTIONS TO EACH FAN
FUSE BLOCKS. SIX WIRES TOTAL,
(1) PAIR PER FAN. (TYP)
TYP.
3
FAN
38
3A
3A
COOLING FAN
POWER
ON
ILT
4F
3F
POWER CIRCUIT
108
109
A
32
108
109
51
60
75
12
1
50
ICB
60A
RT
POLE
LT
POLE
TERMINAL SIDE
OR REAR VIEW
30
IL2
IL1
L1
L2
MAIN POWER
DISCONNECT SWITCH
WITH (2) 30 AMP FUSES
SUPPLIED BY CUSTOMER
101
102
101
102
30
38
IC
76 69 61 55
2
103
104
2LT
5F
105
106
6
25
2
FAN
1PM
30
3
30
108
107
H1
H3
H2
240V
208V
120V
X1
X2
110
111
FRONT
111
15
16
15
16
17
110
TYP.
BACK
112
17
16
3A
3A
1F
2F
22
29
150
151
3TB
68
SEE NOTE "C"
76
61 55
77 70 63 56
4
IT
7.5KVA
150
6
FURNACE DATA
5400 WATS
120 VOLTS
45 AMPS
LEFT HEATING ELEMENTS
1
FAN
8
22
10
APPROX. 45AMPS
FOR 5400W LOAD
SEE NOTE "F"
7
30
5
2TB
EFIT
SEE NOTE "J"
COMMUNICATION
OPTIONAL
SEE NOTE "H"
38
34
32
32
42
39
32
50A
AM
36
69
SEE NOTE "H"
36
36
32
32
44
42
39
SEE NOTE "H"
SEE NOTE "I"
4
3
2
1
LOAD
LINE
106
105
107
TE10A
(1PM ALTERNATE)
108
4/T2
LOAD
2/T1
3/L2
LINE
1/L1
POWER & CONTROL WIRING DIAGRAM
FOR MODEL 51634
W/UT350/UP550 CONTROLLER
WIRE DIAGRAM PART#38339I02
Summary of Contents for BF51634BC-1
Page 1: ......
Page 6: ...List of Figures ii Thermo Scientific...
Page 20: ...Safety Notes Standards and Directives 1 14 Thermo Scientific...
Page 48: ...Communication Option Auto Tuning the Controller 7 10 Thermo Scientific...
Page 64: ...Troubleshooting 10 4 Thermo Scientific...
Page 65: ......
Page 66: ......
Page 69: ...Thermo Scientific 12 1 12 Error Codes This chapter is not applicable...
Page 70: ...Error Codes 12 2 Thermo Scientific...
Page 72: ...WEEE Compliance 13 2 Thermo Scientific...
Page 73: ...Thermo Scientific 14 1 14 14 Spare Parts and Accessories This chapter is not applicable...
Page 74: ...Spare Parts and Accessories 14 2 Thermo Scientific...