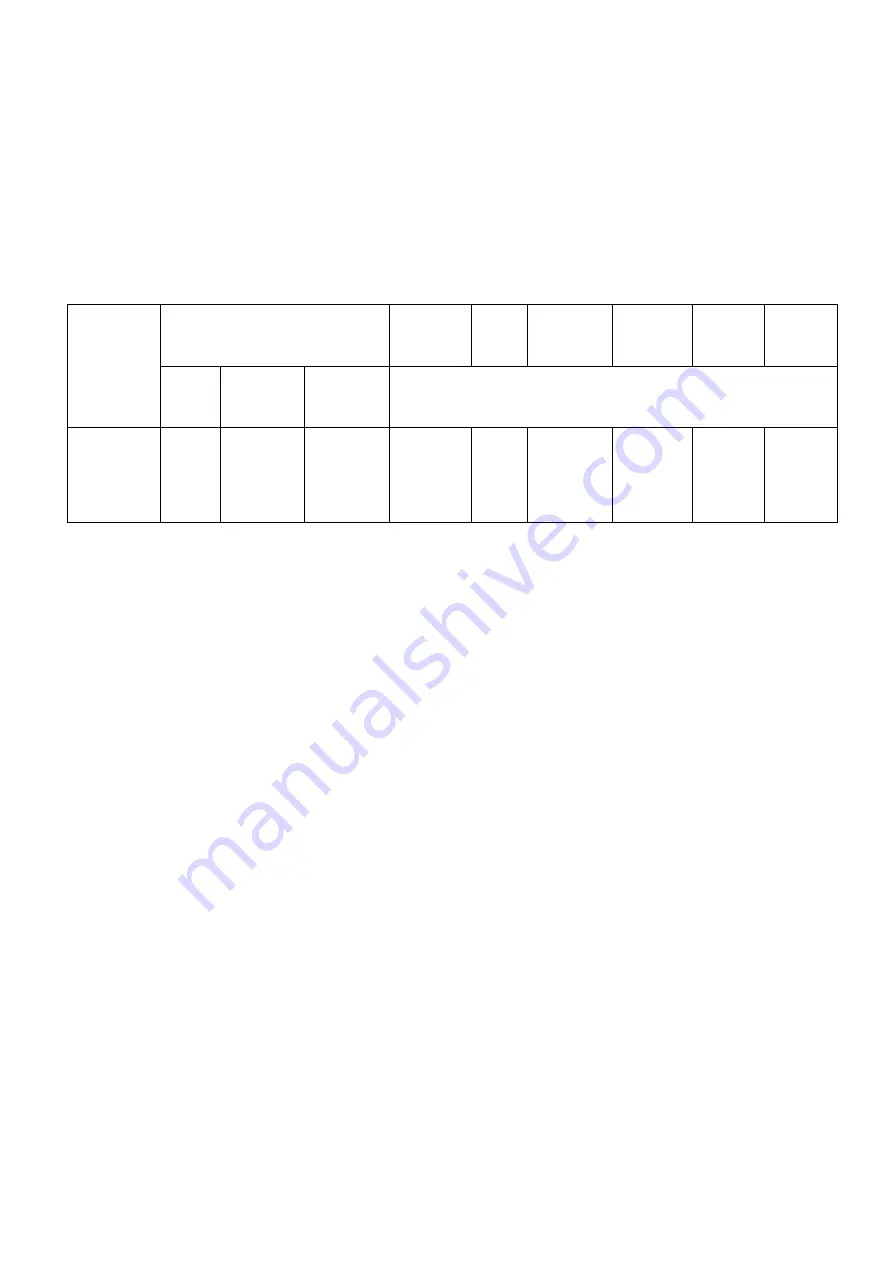
Introduction
Specification
2-2
Thermo Scientific
• Double wall construction.
• Front control panel is recessed at the top. This feature provides easy viewing
of the control LED and protection for the control instrumentation.
Specification
Table 1. BF51841 Laboratory Box Furnaces
The BF51841BC model has adjustable over-temperature control.
Model
Dimension
WXF-BXH in.(cm)
Maximum
Operating
Temp
Watts
Thermoco
uple
Voltage
Integral
Control
Shipping
Weight
lbs (kg)
Cham
ber
Exterior
Shipping
(Approxim
ate)
BF51841C
BF51841BC
15x15
x15
(38.1x
38.1x3
8.1)
29x28x33
(73.6x71.1
x83.8)
30x34x31
(6835x78.
6x71)
1200 °C
5800
Type PL II
208/240
VAC
50/60 Hz
single
phase
Single
setpoint
280
(127)
Summary of Contents for BF51841BC
Page 1: ......
Page 6: ...List of Figures ii Thermo Scientific ...
Page 18: ...Safety Notes Standards and Directives 1 12 Thermo Scientific ...
Page 22: ...Unpacking Unpacking 3 2 Thermo Scientific ...
Page 28: ...Installation Shelf Installation in Box Furnaces 4 6 Thermo Scientific ...
Page 38: ...Correction of Temperature Overshoot 6 8 Thermo Scientific ...
Page 48: ...Communication Option Addresses for Multiple Controllers 8 6 Thermo Scientific ...
Page 57: ...Maintenance Right Hand Door Conversion Thermo Scientific 9 9 Figure 12 Door Hinge Sheet 2 2 ...
Page 63: ...Replacement Parts Thermo Scientific 11 3 Figure 13 Wiring Diagram ...
Page 64: ...Replacement Parts 11 4 Thermo Scientific ...
Page 65: ...Thermo Scientific 12 1 12 Error Codes This chapter is not applicable ...
Page 66: ...Error Codes 12 2 Thermo Scientific ...
Page 68: ...WEEE Compliance 13 2 Thermo Scientific ...
Page 69: ...Thermo Scientific 14 1 14 14 Spare Parts and Accessories This chapter is not applicable ...
Page 70: ...Spare Parts and Accessories 14 2 Thermo Scientific ...