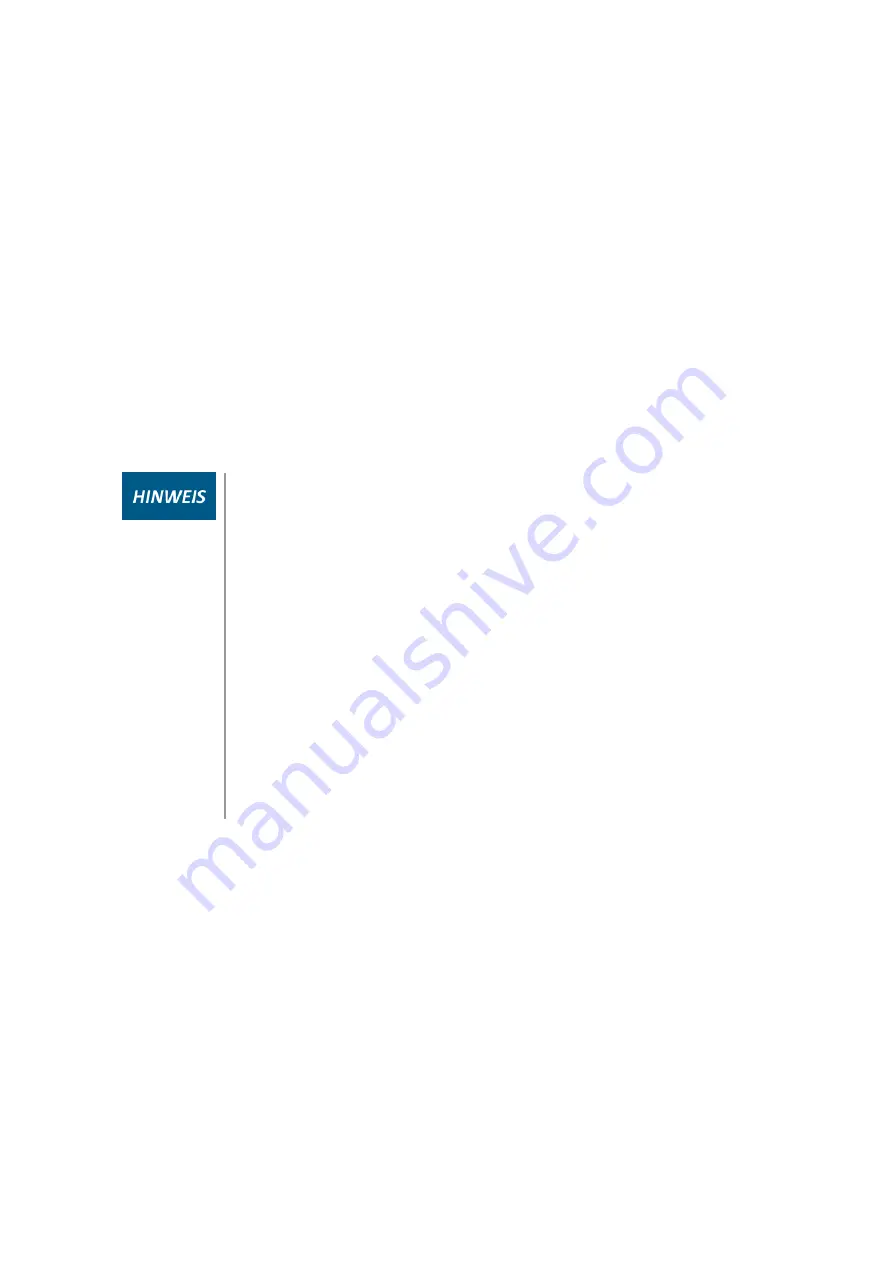
- 23 -
6.2.2
FIRST LOADING THE FURNACE
PLEASE NOTE
Handle sintering aids and insulation components with care.
Avoid vibrations and shocks.
Keep the surfaces clean and free from foreign particles or deposits.
Please find a description of how to load the furnace for the first time below:
Step
Requirements:
The furnace door is fully
open
Use sintering aids approved by the manufacturer when loading the furnace. There
are no general loading instructions. Basically, any combination is permitted,
provided you comply with the following:
Make sure that the load does not protrude over the base plate.
The maximum loading height is 70mm
The protective cover can be used as a crucible when using sintering beads. Avoid
damage to the sintering aids while sintering and ensure sufficient heat radiation from
below.
Use ceramic spacers.
Use setters when sintering without sintering beads. The surfaces are much smoother
than the surfaces of the base plates and reduce stiction significantly during sintering.
Hot spots may occur when heating and may cause high temperature gradients
that could destroy plates and crucibles.
Select extended heating and cooling rates. Power limitation in the lower
temperature range is advantageous but not required.
Do not blow plates and crucibles with cold gas.
We do not provide statutory defects liability on material and parts that are
subject to wear such as heating elements, ceramic sintering aids and fiber
material.
You agree to comply when using sintering aids for the first time.