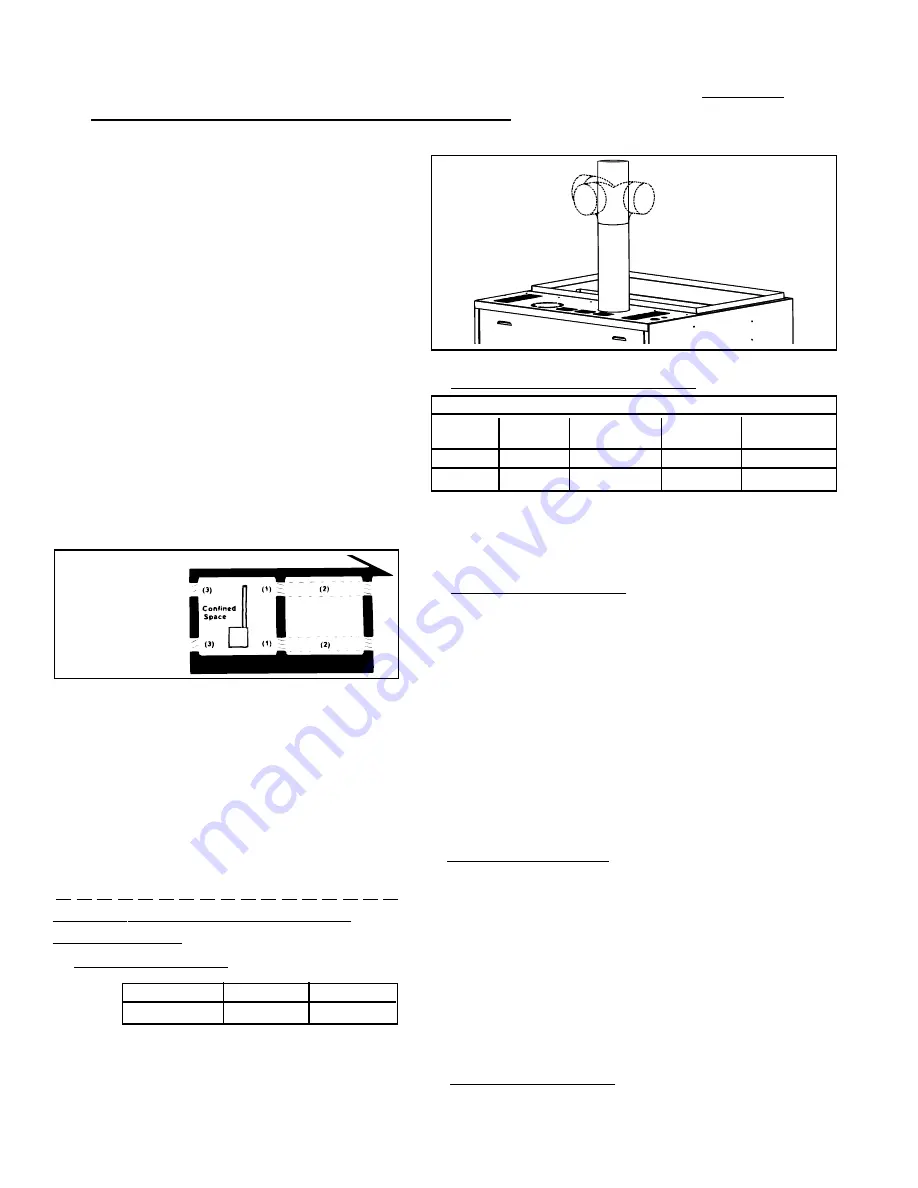
Form 405, Page 10
4) Vent System Support
Lateral runs should be supported every six feet (1.8M) using a non-combus-
tible material, such as strap steel or chain. Do not rely on the heater for
support of either horizontal or vertical vent pipe.
Figure 8 - Alternate
Vent Directions
Specific Venting Requirements (read all
before installing)
1) Venter (Flue) Outlet
Venter
Outlet
Size:
Vent in any
position above
horizontal
A minimum of 12" of
straight pipe is required
before an elbow
Model Size
150, 200, 250
300, 350, 400
Outlet Diameter
5"
6"
Venter Outlet Attachment Requirements:
•
A minimum of 12" of straight pipe is required at the venter
outlet before installing an elbow in the vent system. An elbow
should never be attached directly to the venter. An elbow
attached to the straight pipe can be in any position at or above
horizontal. See Figure 8.
7B. Venting and Combustion Air Requirements for Power Vent Drawing
Combustion Air from THE INSIDE SPACE and Venting Flue Products to
the Outdoors (vent cap is required)
If the environment has a positive pressure and is such that it is
not detrimental to combustion air, this system may be installed.
To provide combustion air to the heater sufficient air must enter
the equipment location to replace that exhausted through the
heater vent system. In the past, the infiltration of outside air
assumed in heat loss calculations (one air change per hour) was
assumed to be sufficient. However, current construction methods
using more insulation, vapor barriers, tighter fitting and gasketed
doors and windows, weather-stripping, and/or mechanical ex-
haust fans may now require the introduction of outside air through
wall openings or ductwork to the equipment room.
The requirements for combustion and ventilation air depend upon
whether the unit is located in a confined or unconfined space. An
"unconfined space" is defined as a space whose volume is not less
than 50 cubic feet per 1000 BTUH of the installed appliance.
Under all conditions, enough air must be provided to ensure
there will not be a negative pressure condition within the equip-
ment room or space. Follow the specific requirements below for
a confined space installation.
Confined Space Installation - Do not install a unit in a con-
fined space without providing wall openings leading to and from
the space. Provide openings near the floor and ceiling for ventila-
tion and air for combustion as shown in Figure 7, depending on
the combustion air source as noted in Items 1, 2, and 3 below.
Figure 7 - Confined Space:
Add total BTUH of all appliances in the confined space and
divide by figures below for square inch free area size of each (top
and bottom) opening.
1. Air from inside the building -- openings 1 square inch free
area per 1000 BTUH. Never less than 100 square inches free area
for each opening. See (1) in Figure 7.
2. Air from outside through duct -- openings 1 square inch free
area per 2000 BTUH. See (2) in Figure 7.
3. Air direct from outside -- openings 1 square inch free area per
4000 BTUH. See (3) in Figure 7.
NOTE: For further details on supplying combustion air to a
confined space, see the National Fuel Gas Code ANSI Z223.1a
(latest edition).
A space whose
volume is less than
50 cubic feet per
1000 BTUH of the
installed appliance
input rating
7. Venting and Combustion Air (cont'd)
•
Do not install dampers or any other type of flue restrictor device.
2) Vent Pipe Diameter and Length
Maximum Vent Length - minimum length is 5 ft (1.5M)
CAUA
Pipe
Maximum
90°
Elbow
45° Elbow
Diameter
Length
Equals*
Equals*
150-250
5"
50 ft (15.2M)
5 ft (1.5M)
2.5 ft (.8M)
300-400
6"
50 ft (15.2M)
5 ft (1.5M)
2.5 ft (.8M)
*Reduce by this amount for each elbow.
Note: If the system contains all vertical pipe or a combination of horizontal
and vertical vent pipe, the Maximum Permissible Vent Length may be in-
creased one foot (305mm) for each foot (305mm) of vertical rise up to a
maximum increase of ten feet (3M).
3) Vent Pipe and Joints
Provide field-supplied vent pipe as specified in the Table on page 4.
•
If using single wall, 26-gauge or heavier galvanized pipe, secure slip-fit
connections using sheet metal screws or rivets. Seal pipe joints either with
tape suitable for 550°F (such as Option FA1, P/N 98266) or high-tem-
perature silicone sealant.
•
If using Category III vent pipe, follow pipe manufacturer's instructions
for joining pipe sections. When attaching Category III pipe to the venter
outlet or the vent cap, make secure, sealed joints following a procedure
that best suits the style of Category III pipe being used.
•
If using double-wall (Type B) vent pipe (at least 1/2 of the equivalent vent
length must be vertical), follow pipe manufacturer's instructions for join-
ing pipe sections. For joining double-wall pipe to the venter outlet collar,
single-wall pipe, and/or the vent cap, follow the instructions below:
Instructions for attaching double-wall (Type B) vent pipe to the ven-
ter outlet, a single-wall pipe run, or to the vent cap (use these in-
structions for either full length double-wall or terminal only):
Hardware and Sealant Required: 3/4" long sheetmetal screws; and a tube of
high temperature silicone sealant
1 ) Look for the "flow" arrow on the vent pipe; attach according to the
arrow. Slide the pipe so that the venter outlet, the single-wall pipe, or the
vent cap is inside the double-wall pipe.
2 ) Drill a hole through the pipe into the outlet collar, the single-wall pipe,
or the vent cap. (Hole should be slightly smaller than the sheet metal
screw being used.) Using a 3/4" long sheet metal screw, attach the pipe.
Do not overtighten. Repeat, drilling and inserting two additional screws
evenly spaced (120° apart) around the pipe.
3 ) Use silicone sealant to seal any gaps. If there is an annular opening, run
a large bead of sealant in the opening. The bead of sealant must be large
enough to seal the opening, but it is not necessary to fill the full volume
of the annular area.