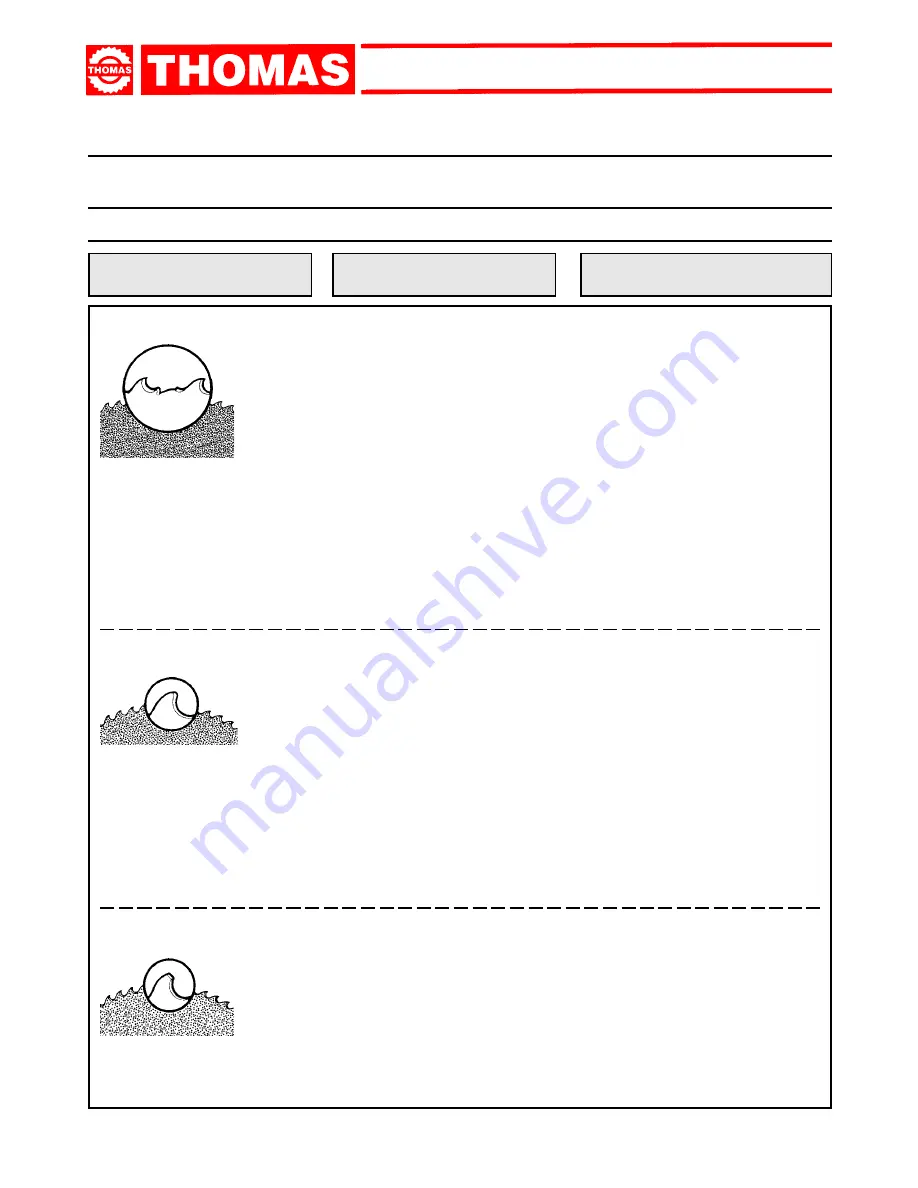
15
CUT 250
CUT 250
CUT 250
CUT 250
CUT 250
PREMATURE DISK WEAR
Wrong running in of the disk
Wrong cutting speed
Unsuitable tooth profile
Wrong tooth pitch
Low quality disk
Insufficient lubricating refrigerant
TROUBLESHOOTING
This chapter lists the probable faults and malfunctions that could occur while the machine is being used and suggests possible
remedies for solving them.
The first paragraph provides diagnosis for TOOLS and CUTS, the second for ELECTRICAL COMPONENTS.
12.1 - Blade and cut diagnosis
12
FAULT
PROBABLE CAUSE
REMEDY
TOOTH BREAKAGE
Too fast advance
Wrong cutting speed
Wrong tooth pitch
Low quality disk
Ineffective gripping of the part in the
vice.
Previously broken tooth left in the cut
Cutting resumed on a groove made
previously.
Insufficient lubricating refrigerant or
wrong emulsion
Sticky accumulation of material on
the disk.
Decrease advance, exerting less cutting
pressure
Change disk speed and/or diameter.
See Chapter
“ Material classification
and choice of disks”
and the Table of
cutting speeds according to disk diameter.
Choose a suitable disk.
See Chapter “Material classification
and choice of disks”.
Use a better quality disk.
Check the gripping of the part.
Accurately remove all the parts left in.
Make the cut elsewhere, turning the part.
Check the level of the liquid in the tank.
Increase the flow of lubricating refrigerant,
checking that the hole and the liquid outlet
pipe are not blocked.
Check the blend of lubricating coolant and
choose a better quality disk.
See Chapter “Material classification
and choice of disks”
in the paragraph
on
Running in the disk.
Change disk speed and/or diameter.
See Chapter “Material classification
and choice of disks” and the
Table of
cutting speeds according to disk diameter.
Choose a suitable disk. See Chapter
“Material classification and choice of
disks” in the paragraph on
Type of disks.
Choose a suitable disk.
See Chapter “Material classification
and choice of disks”.
Use a better quality disk.
Check the level of the liquid in the tank.
Increase the flow of lubricating refrigerant,
checking that the hole and the liquid outlet
pipe are not blocked.
CHIPPED DISK
Hardness, shape or flaws in the mate-
rial (oxides, inclusions, lack of homo-
geneity, etc..)
Wrong cutting speed
Wrong tooth pitch
Vibrations
Disk incorrectly sharpened
Low quality disk
Reduce the cutting pressure and/or the
advance.
Change disk speed and/or diameter. See
Chapter “Material classification and
choice of disks” and the
Table of
cutting speeds according to disk
diameter.
Choose a suitable disk.
See Chapter “Material classification
and choice of disks”.
Check gripping of the part.
Replace the disk with one that is more
suitable and correctly sharpened.
Use a better quality disk.