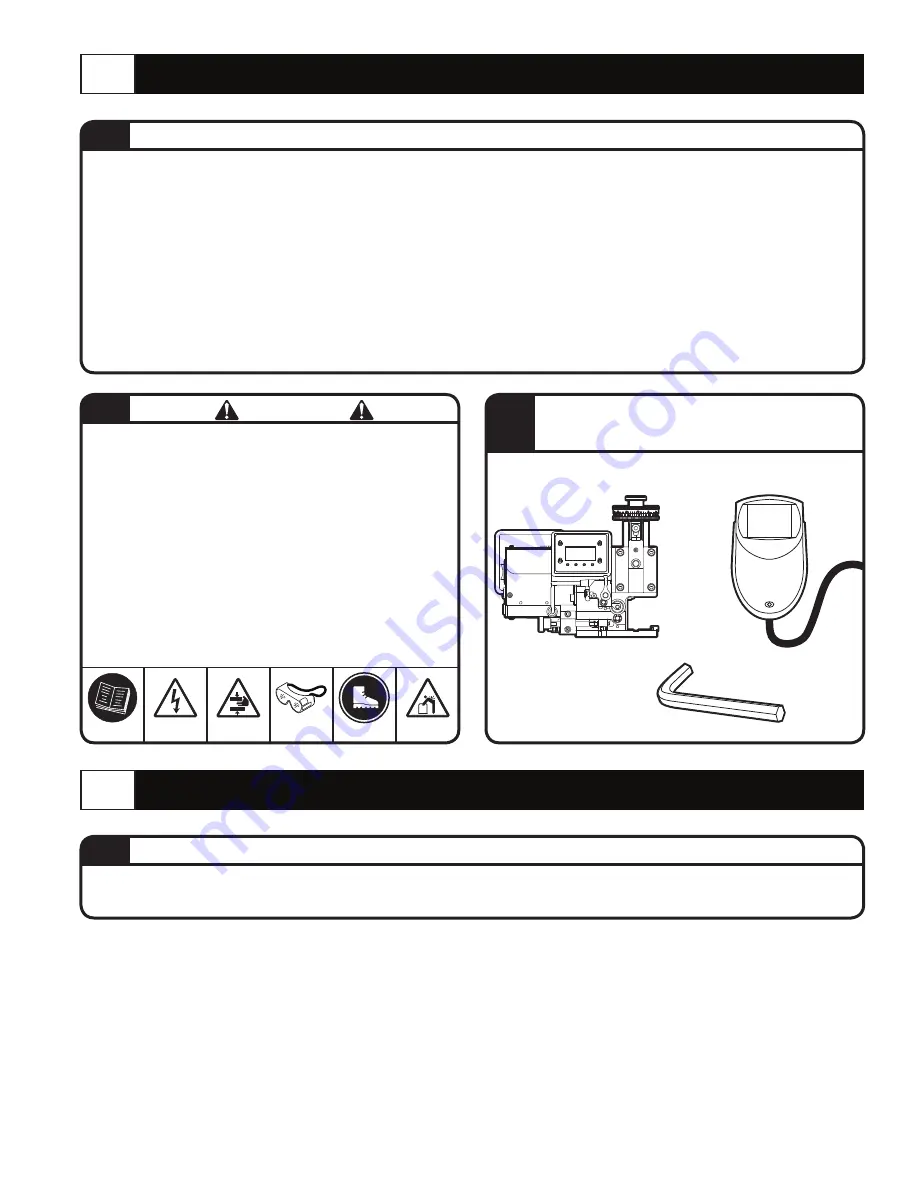
2.1
1. The QUICK-KON™ Automated Crimping System is designed be used with Thomas & Betts Press Assembly
(TNB010-press). Refer to the Press Assembly manual for proper installation.
INSTALLATION
2.0
INSTALLING AUTOMATED CRIMPING SYSTEM
1.3
1.2
ELECTRIC DIE
M5 HEX WRENCH
POWER SUPPLY
QUICK-KON™ AUTOMATED
CRIMPING SYSTEM INCLUDES
1.1
The QUICK-KON™ Automated Crimping System is a left-to-right side feed applicator which installs in most
industry standard presses, which is comprised of the Electric Die, the Stock Guide Assembly and the Ram Tool.
As a result, one unit can be used to crimp a large variety of terminals - simply through the purchase of additional
tool packs.
Unlike traditional applicators, which use mechanical designs to feed terminals, the Thomas & Betts
®
Electric Die
uses a patented feeding method that electronically performs feeding operations pre-termination. The stepper
motor driven pinch rollers engage the carrier strip and push the terminals into place for crimping. Microprocessor
based electronics, in conjunction with sensors, initiate a feeding cycle on the upward motion of the ram and
control the stepper motor to precisely position the next terminal to be crimped. A feed controller allows the
operator to set feeding parameters electronically. As a result of this superior terminal feeding system, tool packs
are readily accessible and easy to swap…set-up is quick and easy.
DESCRIPTION
4
5
6
1
2
3
WARNING
1. BEFORE USING THE TOOL, CAREFULLY READ
INSTRUCTIONS IN THIS MANUAL.
2. ALWAYS DISCONNECT POWER AND DE-ENERGIZE UNIT
WHILE PERFORMING MAINTENANCE OR TOOLING
CHANGES.
3. WHEN OPERATING THE TOOL NEVER PLACE HANDS OR
OTHER BODY PARTS BETWEEN THE CRIMPING DIES.
4. WEAR EYE PROTECTION WHEN OPERATING OR
PERFORMING MAINTENANCE.
5. WEAR FOOT PROTECTION WHEN MOVING OR
OPERATING THE UNIT.
6. CAUTION IS REQUIRED WHEN MOVING OR LIFTING THE
ELECTRIC DIE ASSEMBLY.
1.0
GENERAL CHARACTERISTICS
TA04864 E Page 2 of 13